SolutionsTotal Maintenance
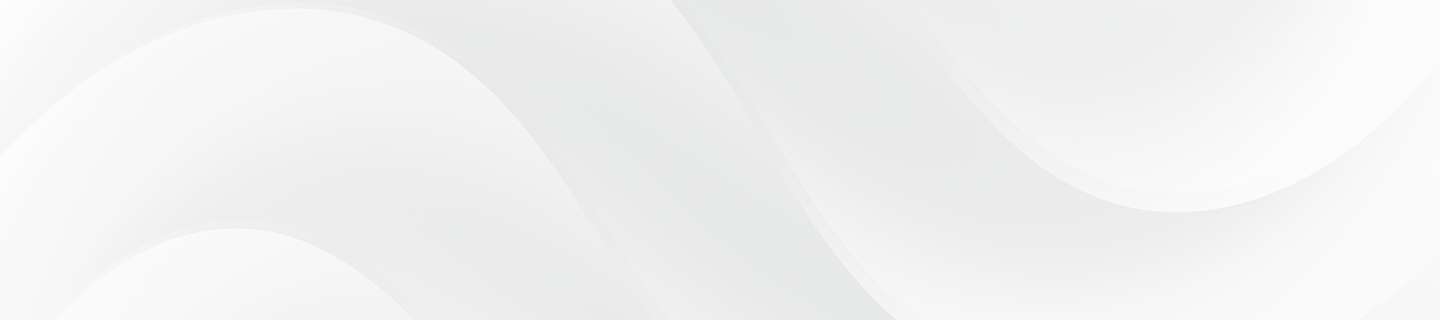
In today’s dramatically changing business environment, the impact of sudden equipment downtime on corporate profits is enormous, and an increasing number of businesses are implementing planned equipment maintenance with the aim of achieving non-stop factories.
Meanwhile, the manufacturing industry faces another major issue of passing down the expertise of highly experienced employees.
Case07Conducting maintenance before robots fail
Predictive
Maintenance・Preventive
Maintenance
Device level
Need to conduct scheduled maintenance appropriate with a robot's operational status.
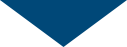
Detect part faults and deterioration by utilizing AI, and notify users of the maintenance periods that are calculated from the operational status.
- Failing or deteriorating robot parts can be detected at an early stage.
- The recommended maintenance period can be calculated with the robot operation pattern data alone at an equipment startup.
- The repair/replacement period for each component is notified in advance, thus achieving efficient maintenance.
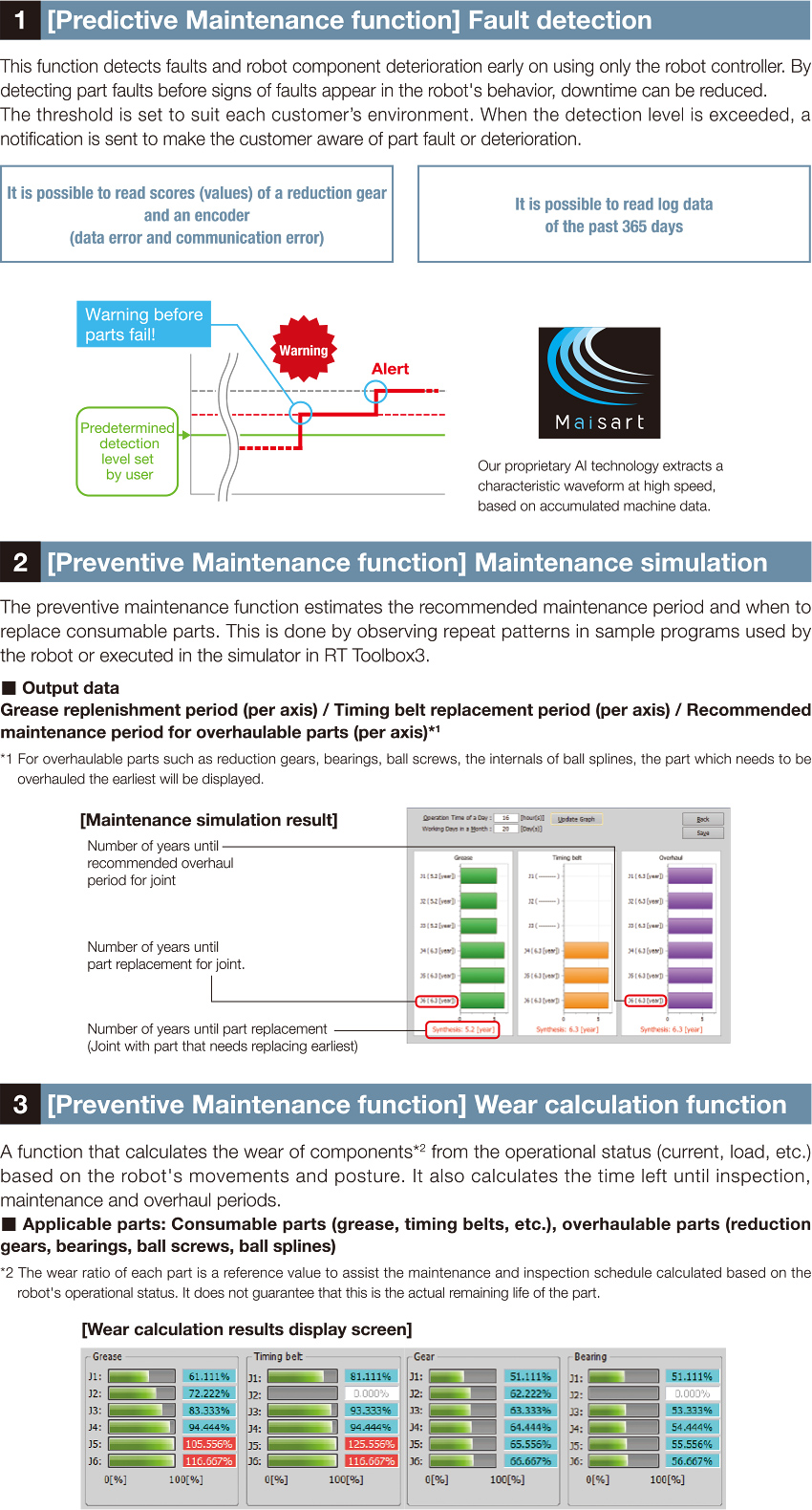
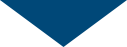
The AI technology detects signs of failures, enabling maintenance before robots fail.
The recommended maintenance periods are simulated from the operation pattern, which helps users schedule maintenance properly.
The wear of robot parts is calculated from the operation pattern, and the maintenance periods are notified.