SolutionsTotal Maintenance
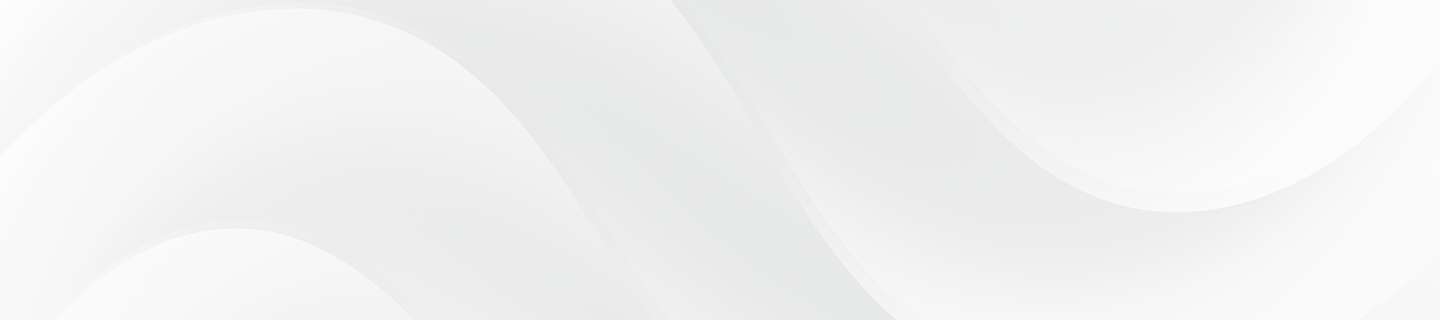
In today’s dramatically changing business environment, the impact of sudden equipment downtime on corporate profits is enormous, and an increasing number of businesses are implementing planned equipment maintenance with the aim of achieving non-stop factories.
Meanwhile, the manufacturing industry faces another major issue of passing down the expertise of highly experienced employees.
Case02Detecting machining defects and preventing the outflow of defective products
Predictive
Maintenance
Equipment level
The bonding in the metal fin caulking process is weak, leading to fins becoming detached due to defective bonding occurs in later processes.
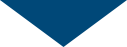
Utilize AI to prevent bonding defects in the caulking process
Use the similar waveform recognition function of MELSOFT MaiLab to create diagnostic rules by learning the waveform data of press loads during normal operation and correlating it with bonding defects.
Press load data is collected in real time by the MELIPC industrial-use PC and then diagnosed based on rules using MELSOFT MaiLab, allowing for bonding defects to be detected, which are then fed back to the equipment (causing equipment to stop).
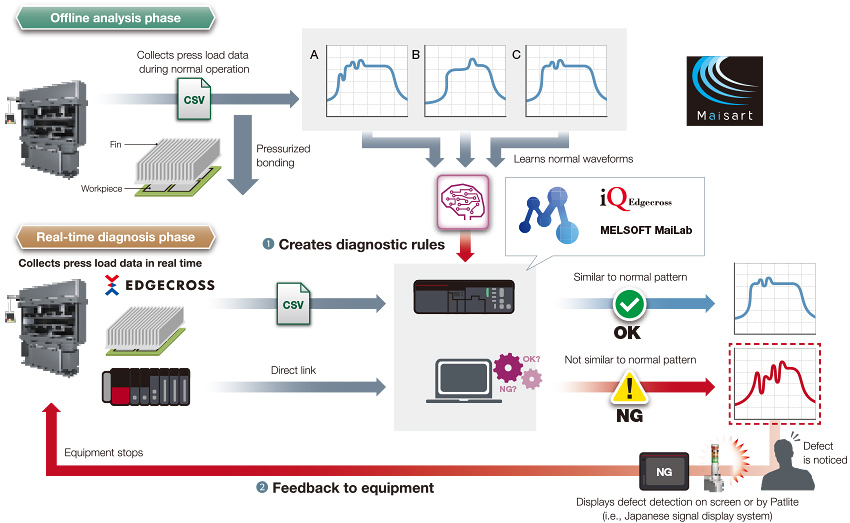
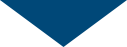
Defect outflows to later processes are prevented through real-time detection of bonding defects.