The Inside View
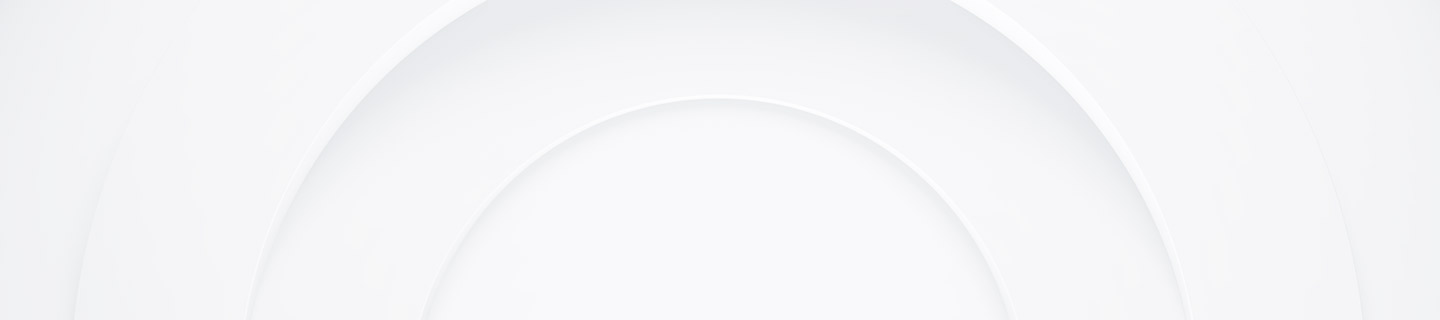
How Mitsubishi Electric servos earned a leading position in the Japanese marketSeisuke Tsutsumi
First Published in Japanese in February 2023 [3 parts]
Part 2: Bringing the latest technology to general-purpose servo systems
The real-time auto tuning function mentioned in Part 1 is based on a control technology called 2-DOF (two degrees of freedom) control. Mitsubishi Electric was the first manufacturer to introduce this control technology to general-purpose servos.
The 2-DOF control method that we developed for general-purpose servos is made up of both a model and a real-loop control section. The model control section adjusts responsiveness to commands, while the real-loop control section adjusts responsiveness to machine friction and other external characteristics. Highly responsive and stable tuning of each of these factors can optimize the performance of the machine.
However, there was one problem: this method involves a lot more parameters than a conventional control method, meaning adjustments take longer. The parameters of a servo need to be altered to the individual equipment to achieve the best performance, so a higher number of parameters has a major effect on the amount of corrections involved.
Real-time auto tuning is based on the idea that most parameters can be determined by modelling. By identifying the model in real-time through observation of the operating status of the servo, the parameters can be automatically determined to allow highly responsive and stable operation of both the model and the real-loop control sections, reducing the need for manual adjustment.
The theory of 2-DOF control has long been established and incorporated into actual servo systems, but in reality, this was restricted to servo systems for special use cases. Expanding the application of the limited 2-DOF control theory to general-purpose servos by establishing real-time auto tuning was a significant development.
However, the level of tuning depends on the accuracy of the model. The next function I want to talk about is the machine analyzer, which we developed to provide better tuning in a shorter timeframe.
Machine analyzer: Analyzing equipment characteristics from the servo
To get the most from a piece of equipment, the user needs to understand it in great detail. The usual way to find out vibration characteristics is to install multiple sensors on the equipment and perform hammering to identify the transmission attributes through analysis. One problem is the high cost of the measuring equipment to perform this analysis, and there is also a lot of preparatory work, such as installing the sensors. This means that when analyzing the characteristics of equipment during development, for example to investigate the cause of tuning difficulties, it takes a long time before an analysis can be started, which reduces development efficiency. Furthermore, when investigating the cause of an error while the equipment is in operation, this method involves long periods of down time, significantly reducing production efficiency.
To tackle this issue, we developed the machine analyzer function: a system where data is analyzed directly from the servo, rather than the equipment itself. The signal from the servo amplifier is evaluated on a PC. When a servo amplifier applies a current containing various frequency components to a motor to operate the equipment, the motor reflects the operating status of the equipment. The machine analyzer uses this to ascertain the transmission characteristics.
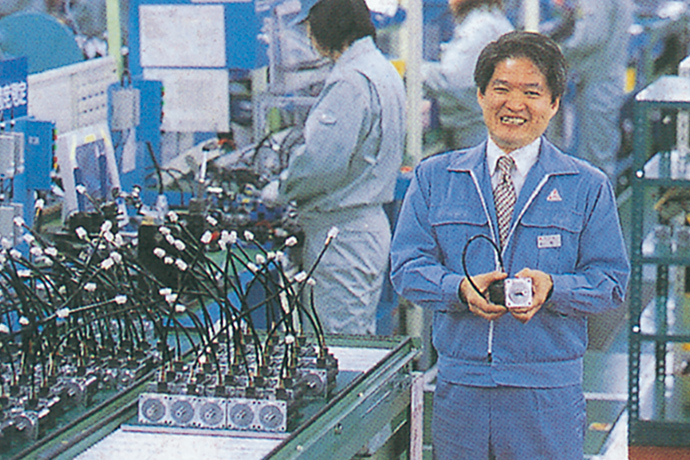
Seisuke Tsutsumi on the MELSERVO assembly line
The machine analyzer function does not require any particular preparation work such as installing sensors, allowing on-site analysis to start straight away. Although it cannot completely replace measuring instruments – for example, it is difficult to apply when the motor is installed at a distance from the equipment – the ability to immediately investigate and address a problem is a huge benefit. Another advantage is that the right parameters for the setup can be quickly determined during equipment development.
This analysis involves complex matrix operations. When we first developed this function, PCs had less processing power, which meant it took around 30 minutes of computing time to obtain the analysis results. As PC performance improved, the process became more effective, but it took about 10 years before it could be put into practice. These days, it is a valuable function that can be used without having to worry about PC processing time.
Digitalization enables synchronization of up to 256 axes per controller module
Mitsubishi Electric provides many other functions and products around servo systems that incorporate cutting-edge technologies. These include high-speed servo networks that are controlled using digital data rather than pulse signals, enabling the synchronization of up to 256 axes per controller module. Other devices include high-resolution encoders with more quantum bits for increased accuracy and small, high-torque motors. With the high-speed servo network, the servo feeds back the current position, speed, etc. to the controller, allowing the equipment status to be monitored. Since improved encoder performance is vital to increasing the functionality of servo systems, we decided to develop a new encoder in-house, rather than using products developed by specialized manufacturers. The result is our high-resolution encoder.
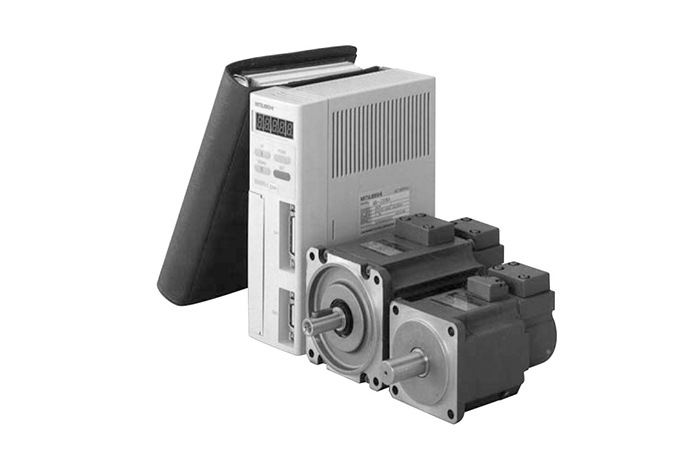
Ultra-small servo
Customers know that Mitsubishi Electric has the advanced technology to make these functions a reality. I think that is one reason we have achieved a high market share for servos, even though we were late coming to the market. Recognizing the servo as the main drive unit of equipment, we will continue to refine our technologies and develop innovative solutions to meet the expectations of machine builders.