The Inside View
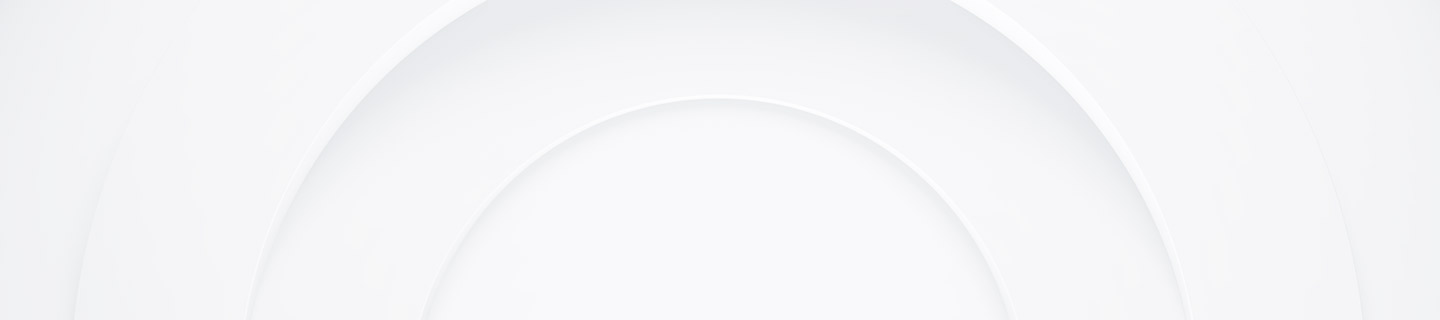
How Mitsubishi Electric servos earned a leading position in the Japanese marketSeisuke Tsutsumi
First Published in Japanese in February 2023 [3 parts]
Part 1: “All digital” systems transformed the potential of servos
Servo systems are used in the main drive units of manufacturing equipment. As a result, the functions and performance of the servo affect the added value and productivity of the equipment. As products and manufacturing requirements have developed over time, more sophisticated functions and performance are required. Let's take surface-mount technology (SMT) component placement systems as an example. Rising sales of products like smartphones, the increasing number of electronic components mounted on a single product, plus the demand for ever more compact devices, have led to constantly growing pressure to improve productivity. This in turn requires servo technologies that enable ever faster and more precise positioning. If a machine builder doesn't select the right servo, there is little hope of providing a solution to meet these challenges.
Mitsubishi Electric released its first general-purpose (non-numerical control) servo system in 1983. Many of our competitors in Japan were already offering servos, and we were actually among the later manufacturers to enter the market. I began working on servo development the following year. We have worked hard to catch up and surpass our competitors, developing many industry-leading technologies along the way. This sustained effort has resulted in the loyal customer base that we enjoy today.
I would like to mention some of the innovative technologies that have helped us gain our customers' trust, and how they were developed.
Vibration control: The technology behind our customer's bid for the top
Vibration is an unavoidable factor in machines, but it is the greatest challenge when it comes to those requiring micron-level precision, such as electronic component mounting systems. In the past, users would usually try to prevent vibration on the mechanical side, but attempts to suppress vibration by increasing rigidity resulted in heavier equipment and also affected the cost. That's why we started working on ways to control vibration on the software side. Our challenge was to create an "all digital servo".
Specifically, this meant developing software to analyze vibration and eliminate the factors that cause it. In the past, these tasks had been carried out by the manufacturer of the equipment where the servo was installed. All-digital servos allow vibration control to be handled on the servo side, reducing work for the equipment manufacturer. However, although we knew it was theoretically possible, the actual development was complex, and it took about four years during which we worked closely with our partners to reach the quality levels we wanted before advancing to practical application.
The idea for developing vibration control originally came after an enquiry from an equipment manufacturer. This customer wanted to produce machines that would make them the world's top manufacturer in their sector, we wanted to help them, and that's what prompted us to start developing this technology.
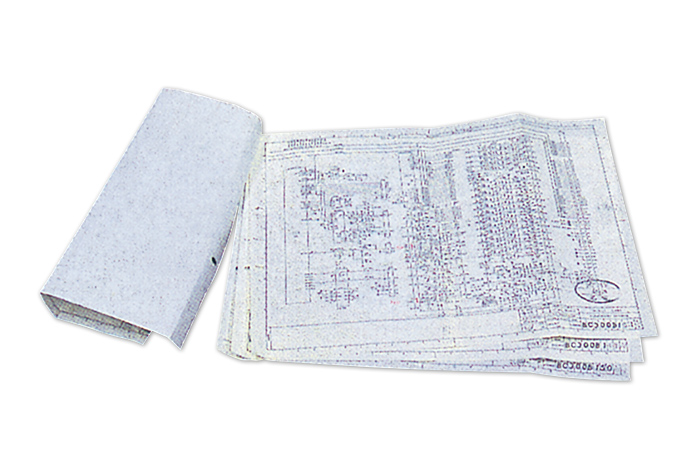
Image of basic specifications
We started with a competitor analysis. When we looked at the equipment that was considered the best in the world at that time, we realized that although the mechanisms were excellent, vibration control depended on the hardware. We decided, "The only way to beat them is with software," and the result was our vibration control function. This was one factor behind the incredible success of our customer's equipment, which ended up gaining a top global market share. There is no feeling quite like the joy of being part of a project where you have worked hard to help make a customer's ambition a reality.
Real-time auto tuning: Replicating the "magic touch"
Servo systems require tuning of the control parameters to ensure the equipment will operate as intended. This is a job that needs considerable expertise, so servo manufacturers send out engineers to perform on-site tuning. Once, when I was performing tuning for a system start-up and got it right first time, the customer said I had the "magic touch". Although I was pleased by this praise, it came as quite a shock. If we had to keep providing "magic" to keep up with sales, even if business expanded, it would never make a profit.
We therefore set out to develop real-time auto tuning: a function allowing the servo to automatically tune itself. Values including the inertia of the equipment are calculated in real-time, based on the current and speed, and control parameters are automatically configured to ensure stable and highly responsive operation, taking these calculations into account. We were the first company in the world to provide this function in a general-purpose product.
Real-time auto tuning is based on a control method called Reference Model Following Control, which uses a 2-DOF (two degrees of freedom) control method. The reference control target is modeled, and the equipment is operated in accordance with this model. When we were developing this function, we had issues with insufficient CPU performance at the time, but improvements have meant even complex models can now be computed at high speed. The performance of real-time auto tuning has also increased dramatically through experience gained in a wide variety of applications.
Our latest servo system, the MELSERVO-J5 series, includes an even more advanced version of this function, with a full range of tuning functions for different purposes. Even if the servo is required to perform more complex control operations, startup is possible without relying on an expert engineer to tune the system. This is something that customers will always appreciate, which is why I believe auto tuning will be required more than ever.