News Release Archives
Note that the releases are accurate at the time of publication but may be subject to change without notice.
FOR IMMEDIATE RELEASE No. 2907
Mitsubishi Electric Develops Cutting Tool Position-control Method for Machine Tools
Facilitates high-speed, high-accuracy machining of complex geometries
TOKYO, February 17, 2015 - Mitsubishi Electric Corporation (TOKYO: 6503) announced today it has developed an advanced numerical-control method for compensating tool position error in predicted target tool paths. In five-axis machining tests, Mitsubishi Electric verified that the new method reduces machining time by 10.4% for improved productivity in machining complex geometries.


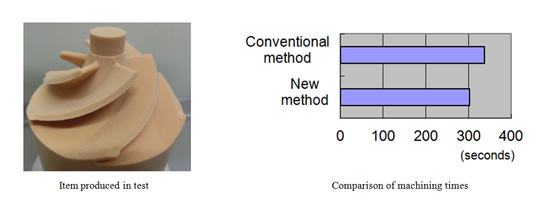
A computerized numerical controller (CNC) moves a machine tool along a target tool path during cutting. The CNC commands the tool's successive positions on the target path by controlling the motors that move the tool. Errors can occur between the specified and actual positions of the tool, but CNC is used to compensate for such errors. Curved paths require more extensive control of the tool as it moves quickly, which can lead to greater position error due to overcompensation or vibration from the cutting machine.

Mitsubishi Electric's new numerical control method compensates error based on target-path prediction rather than command tool position. The method reduces the amount of compensation required, resulting in less machine vibration and faster machining.

Market demands are increasing for cutting work, so manufacturers are looking for ways to raise productivity through faster cutting. Mitsubishi Electric's new cutting tool position-control method is expected to meet these demands by offering a key solution to the technical challenges that have hindered faster cutting.

Patents
Pending patents for the technology announced in this news release number five in Japan and three abroad.

Mitsubishi Electric's new numerical control method compensates error based on target-path prediction rather than command tool position. The method reduces the amount of compensation required, resulting in less machine vibration and faster machining.

Market demands are increasing for cutting work, so manufacturers are looking for ways to raise productivity through faster cutting. Mitsubishi Electric's new cutting tool position-control method is expected to meet these demands by offering a key solution to the technical challenges that have hindered faster cutting.

Patents
Pending patents for the technology announced in this news release number five in Japan and three abroad.
Inquiry
Customer Inquiries
Mitsubishi Electric Corporation