News Release Archives
Note that the releases are accurate at the time of publication but may be subject to change without notice.
FOR IMMEDIATE RELEASE No. 2727
Mitsubishi Electric Develops Ultra-High Resolution 3D Shape Representation Technology
Operators can evaluate surface textures without conducting high-grade processing tests
TOKYO, February 12, 2013 - Mitsubishi Electric Corporation (TOKYO: 6503) announced today it has developed ultra-high resolution 3D shape representation technology for numerically controlled (NC) machine tools. The technology displays detailed shapes of machined surfaces down to a resolution of 1 micrometer (um) in a 3D machining simulation, which machine operators can use to evaluate surface textures without trial cutting through a high quality machining process.
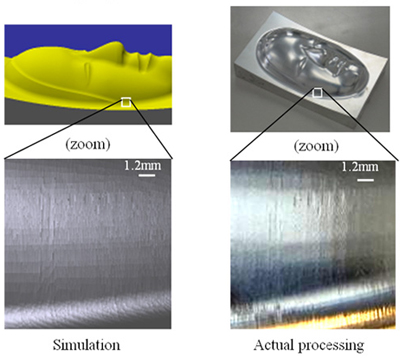

Surface Quality of Simulation Versus Actual Processing

Key Features
1) Ultra-high-resolution reproduction of processing
|
|||||
![]() |
|||||
2) Highly manageable ultra-high-resolution 3D simulation data
|

Features | Resolution | Required memory size (In the case of the sample shown in the figure above under the same condition of 1 um resolution) |
|
New | Simulation-based evaluation of processed surface properties | 1 um | Less than 50 MB |
Old | Simulation-based shape evaluation of processed material and operations | 0.1 mm | Approx. 16 GBin theory |

Multi-ADF
The 3D representation of multi-ADF proprietary technology developed recently by Mitsubishi Electric uses less than 1% of the storage capacity required by conventional, high-resolution geometric model resolutions at the 1 micron level. Multi-ADF represents 3D shapes with a set of tiny cubes each with refined descriptions of multiple surfaces on them. This technology makes it possible to display dents and scratches on machined surfaces down to a resolution of one micrometer using fewer cubes, allowing high-speed simulations that require little memory.

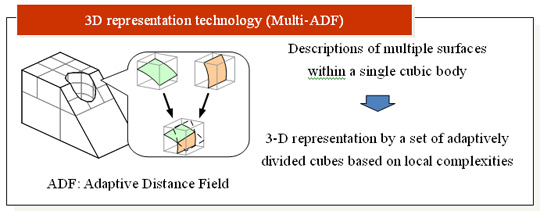

3D representation technology (Multi-ADF)

Development Background
In recent years, the mold processing sector has pursued ways to reduce time by using high-precision, high-quality machining methods that do not require polishing. Further, direct processing is being used increasingly instead of die-mold production, which has raised the demand for high-quality finishing by cutting.
Cutting devices are controlled by machining programs generated by computer-aided design (CAD) and computer-aided manufacturing (CAM) programs. Actual machining tests are normally done to verify the integrity of machining programs. This requires a lengthy process of repeated trial cutting to confirm that high-precision and high-quality machining results are achieved.
Mitsubishi Electric's new technology enables high-precision, high-definition finishing by simulating 3D machining, which leads to more efficient production by permitting operators to evaluate surface texture outcomes, as well as by eliminating the need for tests of actual high-grade machining.