The Inside View
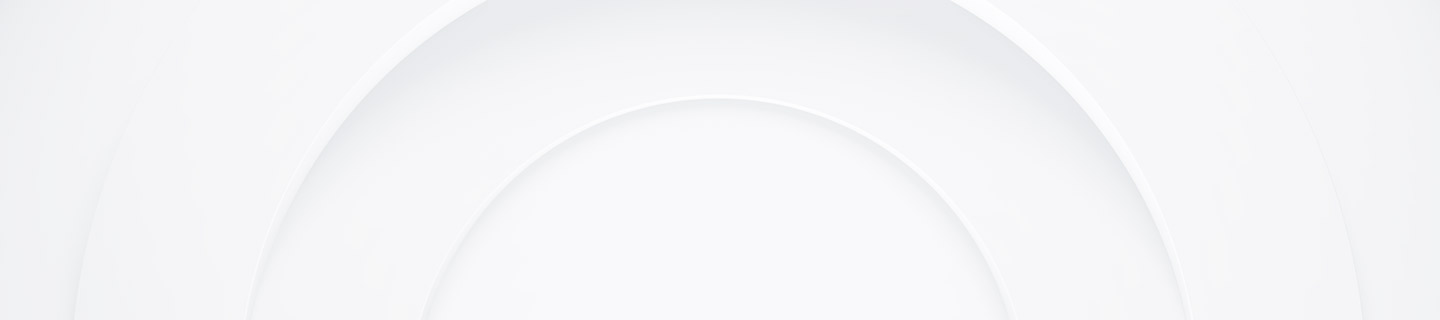
Is ‘change’ the new norm for manufacturers?
Published in September 2023
During the Covid pandemic, a ‘new norm’ was formed. Hajime Sugiyama, who at the time was the Industrial IoT Evangelist for Mitsubishi Electric Factory Automation, made some predictions about what manufacturing would be like in the future. Here we review those comments on 2020 to see how accurate they were, and to see how much of that change, if any, remains. In this review it’s worth pointing out that we are only looking at the impact on manufacturing and not making any value judgements on the decisions of governments and authorities.
Last article by Sugiyama: Manufacturing in the new normal
EN
https://www.mitsubishielectric.com/fa/magazine/pdf/03_issue/art_of_manufacturing_magazine_03_en.pdf
Did Covid affect manufacturing?
A good starting point for this evaluation is the title of Sugiyama’s piece, ‘Manufacturing in the new norm’. At first glance this seems like a fairly innocuous thing to say. However, if we consider the specifics of the ‘new norm’ there is actually a whole other story to consider.
The pandemic created a totally new set of challenges and circumstances which manufacturers had to deal with, and these could quite rightly be called a new norm. But since then, it seems manufacturers have had several further iterations of the ‘new norm’.
One of the global impacts of the reaction to Covid was the initial shutting down of Chinese manufacturing for several months, as a measure to stop the spread of the virus. This cut off the supply of vital components and parts to the rest of the world’s manufacturing base, creating shortages, and disrupting manufacturing in countries where Covid was still yet to emerge.
In parallel to this, shipping also became difficult. Containers, shipping, airliners and other transportation were often in the wrong place, yet the need to get remaining stocks from China as rapidly as possible meant there was an increase in demand. The effects were most strongly seen in discreet industries but process and hybrid industries, such as food and beverage and pharmaceutical were also impacted.
One effect of this was that some manufacturers and politicians started to question their reliance on a single manufacturing hub like China. In some countries, including the USA, a whole discussion began around the topic of re-shoring – creating new local parallel supply chains. The market research company CBInsights noted in a 2022 report that “In 2020, there were 109K jobs re-shored to the US, with 46% of these positions coming from China...”
As a result, people looked at their local manufacturing infrastructure and often found that either it hadn't been maintained, as it wasn’t required at the time, or that it was not able to react quickly enough. This led to the conclusion that big reinvestments were required.
Further research by CBInsights and Deloitte noted that initially in 2020, 38% of manufacturers surveyed claimed Covid had reduced their investments in smart factories and digital technologies. However, additional research by Plex in 2021 reported this was quickly reversed, with 80% of manufacturers now claiming investment in these areas was critical to their survival.
The report also noted that investment in these technologies was at its greatest level since 2017, with the USA leading the way at 39% closely followed by China at 23%.
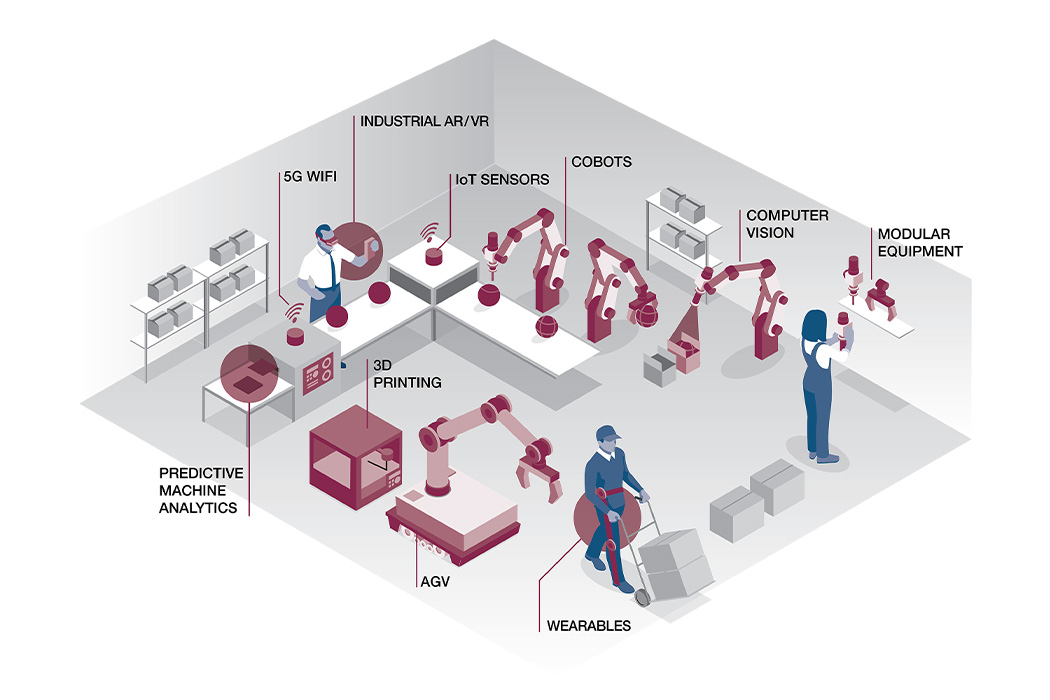
A very relatable and visible example of the market change, and need to react, was the sudden demand for consumer electronics and hence microprocessors, memory devices etc. This was fuelled by a second indirect impact of Covid, i.e. workers and consumers who were now spending more time at home due to restrictions, wanting more home IT or entertainment devices. Forbes succinctly summarized this as follows “The pandemic accelerated supply chain volatility as many electronics teams executed re-shoring, near-shoring, line moves, and other methods of supply chain diversification to improve agility and avoid total production stall-out,” but perhaps we should look a little deeper.
The Covid virus itself created a new norm for manufacturing with new safety measures, which we will discuss later. The indirect effect was the disruption of the global supply chain, which in itself created a ‘new norm’.
Since then, recent geo-political tensions have added more pressures and more iterations of the ‘new norm’. For instance, as the availability of energy became potentially unstable, additional transportation route issues arose, while for some specific industries like food and beverage, selected foodstuffs (edible oils and wheat etc.) became difficult to source.
What we can conclude is that perhaps manufacturing’s ‘new norm’ is not triggered by a single specific event like Covid, but actually manufacturing’s new norm is coping and adapting to instability in a timely and flexible way, i.e. change is the new norm for manufacturers.
Social distancing and PPE on the shopfloor
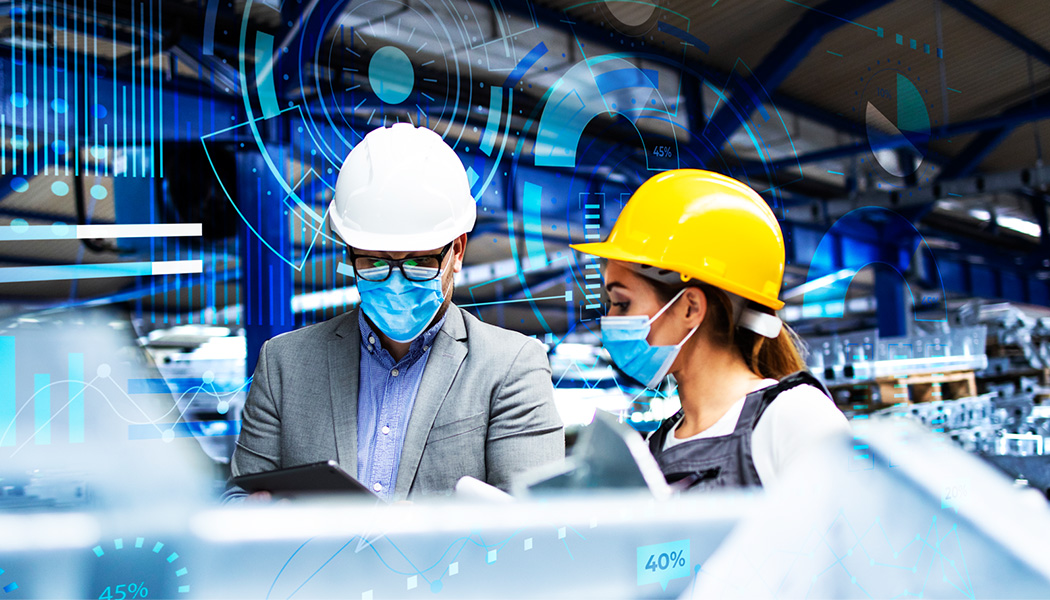
Let’s move onto the first detailed remark by Sugiyama, “How do you implement social distancing in a factory?”. In the process of answering his own question, Sugiyama took a 360-degree look at how protecting workers from Covid could be implemented. Naturally, the use of PPE (Personal Protective Equipment) was mentioned along with potential issues of its use in specific industries. Other solutions, such as work shift patterns were also mentioned.
So, looking at what actually happened, did PPE get used? Yes it did, even to the extent that several manufacturers, including Mitsubishi Electric, set up their own temporary facilities to produce PPE. Additionally, it became common to see plastic partitions in many public places, and it’s no surprise that similar barriers were also implemented in manufacturing facilities. As conditions have now improved the continued use of both PPE and physical barriers is reducing, so this change really was one closely linked to the actual Covid conditions.
Changes in manufacturing work practices
Work patterns in many manufacturing facilities also changed, but in a much more fragmented way. For factory workers the introduction of multi-shifts instead of single shift working, reduced personal contact, as did staggered start-finish times.
Remote working became commonplace, particularly among office workers, for many of whom flexible working practices still continue. Some companies have tried to reimplement full office work and met with a backlash with many people unwilling to revert back to the old norms. For factory floor workers there has been discussion around four-day weeks with several countries like the UK and Portugal, implementing national experiments.
The UK pilot project ended in early 2023, and despite it not being universally successful, many companies decided to continue with the reforms, or have adapted them to meet their own circumstances. So Covid led to significant working changes, for some but not all people.
Rise of the cobots
Sugiyama’s third area of review was the use of collaborative robots or cobots. In his original piece, Sugiyama suggested that cobots would come into their own, supporting workers and manufacturers as they dealt with Covid, changing work patterns and social distancing. They would also be useful as a countermeasure to skills- and know-how losses. This proved to be accurate, as evidenced by increasing numbers of cobot installations.
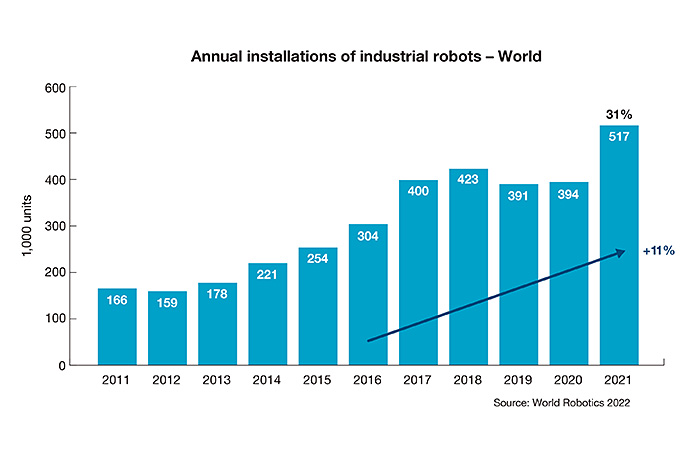
According to the Association for Advancing Automation, robot sales in general in the USA for the period Q3 ’20 to Q3 ’21 increased by 32%. The International Federation of Robotics saw almost no change in global industrial robot sales in total over 2019 and 2020 but a rapid pick up in 2022, reaching an “all time high” of over half a million robots installed, representing a growth of 31% year-on-year.
Interact Analysis concur, reporting specifically industrial cobot sales dropped modestly between 2019 and 2020 to US$602.1m, but then grew through 2022 to around US$1,046m. So, it is clear Sugiyama was right with his comment that robots, and specifically cobots, are a key element that is changing the world of digital manufacturing.
Remote working – is it here to stay?
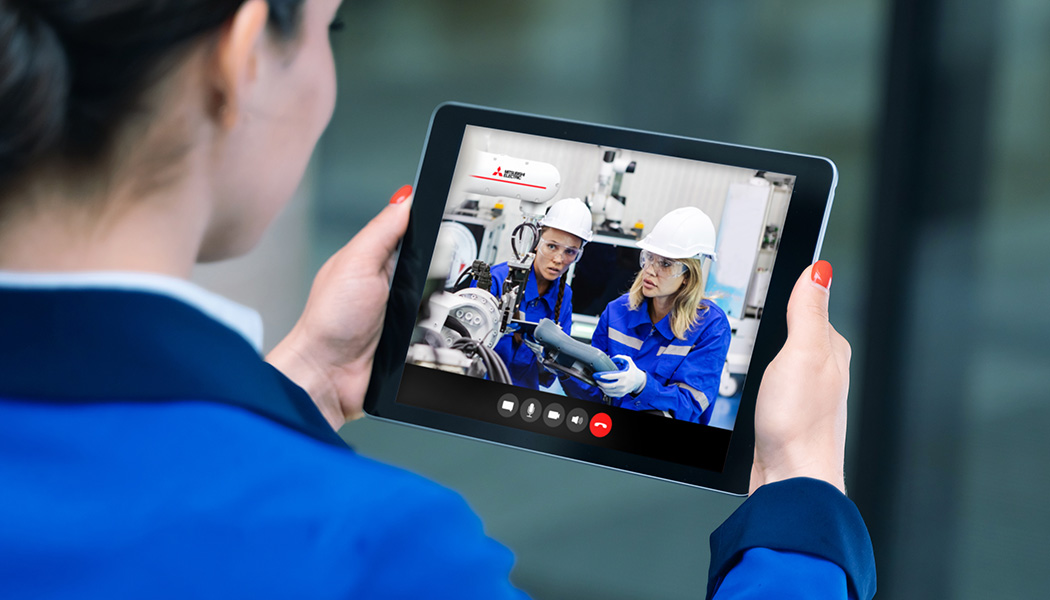
The fourth and final area of Sugiyama’s observations was the use of remote working. His focus was specifically the remote access and maintenance of factories and production environments. This has been a growing trend for some years and Covid has accelerated it, with two developments aiding its implementation.
The first is the near-universal enablement of remote, face to face meetings using video conferencing tools. The second is the expansion of BYOD (bring your own device) that has been enabled by changes in approaches to cyber security. The combination of these two elements has supported the use of remote monitoring tools as it has meant that expert ‘help’ can be provided to remote locations in real time, often with ‘live’ views of machinery etc.
Forbes further noted that: “This, in turn, accelerated the adoption of cloud-based tools for line and supply chain management and remote collaboration.”
Meticulous Research go further and noted in its analysis that SCADA sales dropped in line with other automation sales at the start of the pandemic but recovered in 2021. They go on to say, “This is due to the need for minimum human contact with the newly manufactured products to prevent spread of the virus and control the operations through automated control solutions.”
Closing thoughts
Sugiyama’s analysis of changes in manufacturing trends due to Covid has proved accurate. And now with the passage of time, we can look back and see other significant changes that were either indirectly felt or were experienced in succession. However, perhaps the PNC Financial Services Group said it best: “Manufacturers are adapters by heart. When something goes wrong, they find ways to circumvent the issue or develop new solutions. The pandemic provided the perfect environment to put this ingenuity on full display.”
What better way to highlight that ‘change’ is indeed the manufacturing sector’s new norm.
If you would like to read Sugiyama’s original column, please click here.
EN
https://www.mitsubishielectric.com/fa/magazine/pdf/03_issue/art_of_manufacturing_magazine_03_en.pdf