Solutions
Electrical & Electronic
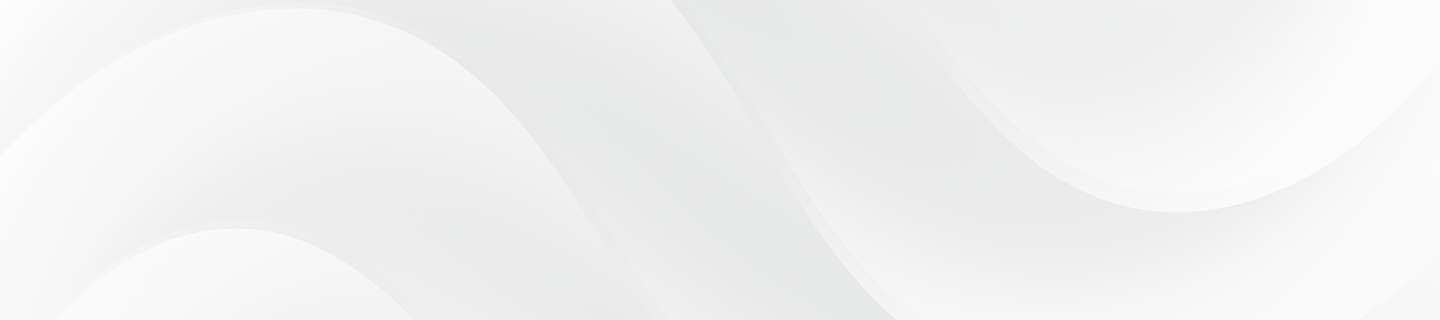
Precise screw tightening
Two robots work together to transfer the flexible workpiece (FPC: flexible printed circuit) and tighten the screws. Force sensors are used to detect position shifts and abnormalities to prevent damage.
Precise screw tightening example
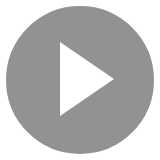
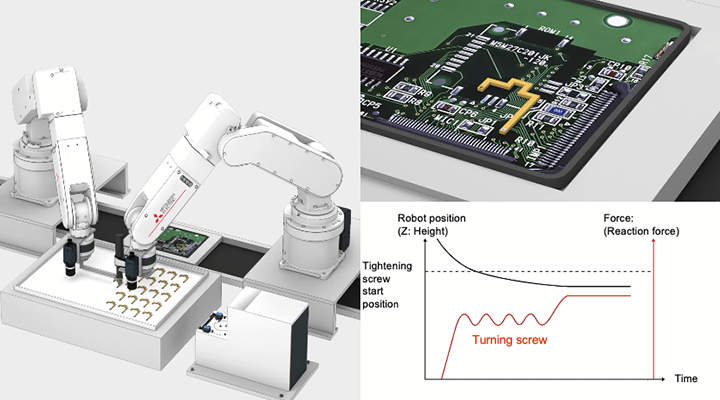
Solutions to the Issues
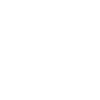
Issues
More robots with greater flexibility are being utilized in screw tightening processes, which are often part of the manufacturing processes in the electrical/electronics industry. Consideration is also increasing for the automating complex operations using multiple robots.
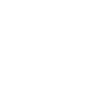
Solutions
- Two robots work together to transfer the FPC (flexible printed circuit).
- Robot takes out a screw from the screw supply machine.
- Vision sensor checks the workpiece position.
- Robot calculates the work position internally using vector calculation method and moves the screwdriver tip close to the compensated position.
- Force sensors detect positioning error and control the pressing force during screw tightening.
- Electric screwdriver mounted near tip/flange of the robot tightens the screw.
- Interference between multiple robots or with surrounding equipment is automatically avoided throughout the above process.
Points
- 【Co-rotation prevention】
- Screw tightening is performed while maintaining position of lightweight workpiece.
- 【Angular operation supported】
- Screw tightening from various angles is supported by freedom of the 6-axis robot.
- 【Synchronized motion with screw insertion】
- Force control is utilized to maintain constant pressing force even while tightening the screw.
- 【Flexible material transfer】
- Lightweight flexible workpieces (FPCs, etc.) are transferred and positioned by multiple robots.
- 【Interference avoidance】
- Programless interference avoidance is achieved through real-time monitoring.
- 【Precision product/screw hole protection】
- Force sensors detect abnormalities and stop motion to prevent product damage.
When an abnormality occurs due to positioning shift
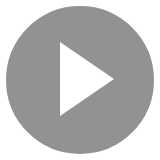
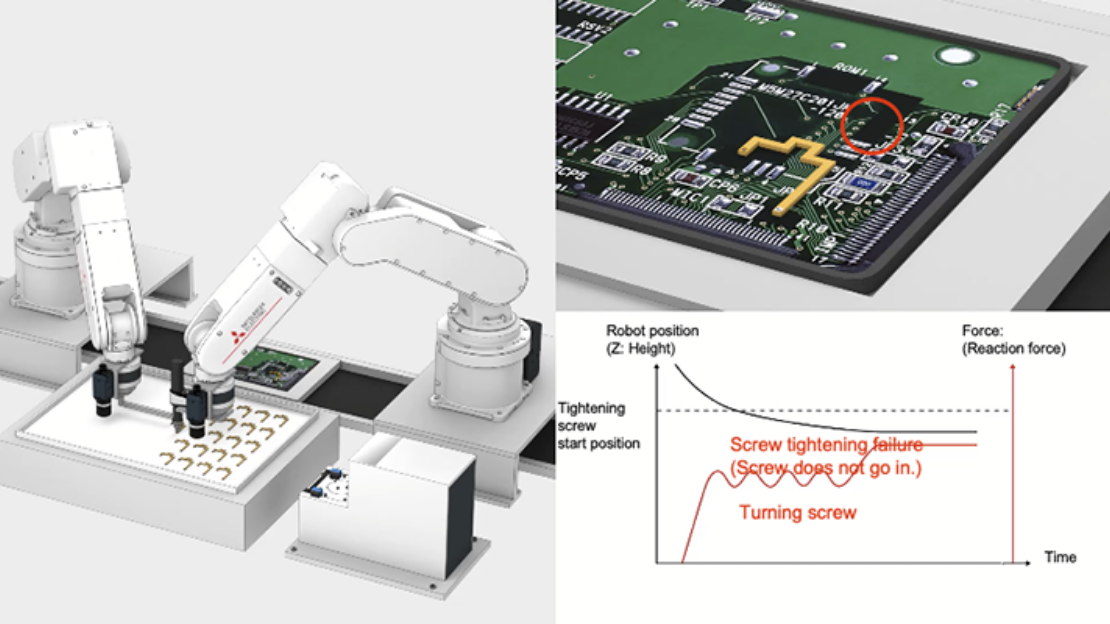
Hole position shift caused by faulty workpiece.
Force sensors detect abnormality and prevent the screw from being tightened in the wrong position, protecting the product.