Factory Automation
Case study
Intelligent
manufacturing
through
production
control
visualization
and traceability
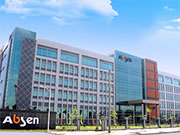
Absen
LED display Industry, China
Background / Issues
Improve production control targeting No.1 status in the industry
Absen is a Chinese manufacturer of large LED displays to the global market. Its products are widely used for high-impact performance displays in shopping malls and theme parks, as well as for high-definition information displays in monitor/control rooms and broadcasting studios.
At Absen’s factory, the production control method was dated, and there were major problems in information flow between the production site and production controllers. Additionally, Absen were considering how to increase their production levels with the aim of becoming the industries number one supplier.
Solution
Realization of data conversion and traceability
Absen needed a solution which leveraged deep industry knowledge and offered a far-reaching system of collaboration which together could realize an intelligent manufacturing model that was appropriate for them. So Absen turned to Mitsubishi Electric and their e-F@ctory concept.
Working together they first determined the data they needed to collect, then defined and interpreted the key parameters of each device or machine. Next, the automatic reading of traceability data and results of quality control inspections were added. As a final step, visual control was deployed. By controlling each device’s processes in real time it became possible to prevent defects due to human factors and to stop abnormal situations in their tracks.
Effect
Data can be used both upstream and downstream
Through collecting, analyzing, and visualizing production data, the management team could grasp the status of equipment and production in real time. With the realization of collaboration between downstream and upstream production in the company, close alignment between procurement and sales as well as production could be achieved, thus realizing consistent intelligent manufacturing.
Image: Continuous visualization, analysis and improvement was made possible
SMKL
Digitizing production equipment made data available to the whole company
Level D
Optimize
Making ROI bigger step by step by using SMKL.
Level C
Analyze
Level B
Visualize
Level A
Collect
Level 1
Worker
Level 2
Workplace
Level 3
Factory
Level 4
Supply Chain

“Maturity Model” is a known type of analysis, it also makes the reader think of higher management analysis so is the right way to describe this….because it is actually a maturity model!

Just to make continuous investment is probably a bad business decision but to make that investment sustainable means that it pays for its self and continues to drive value – simply investing continuously does not guarantee benefit – only cost
Traceability
-
STEP IA1 :Data collection
-
STEP IIB3 :Application to the entire factory
By determining and collecting relevant data at activity, machine and line levels in real-time, a complete picture of the current operations could be grasped. Combining this with tracking each product through the production cycle via a unique code, enabled full production traceability to be achieved. As a final step, this data can be used in downstream and upstream production in the company.
Customer's voice
Mitsubishi Electric is our partner for intelligent manufacturing
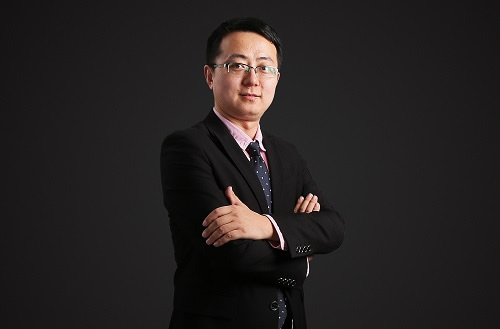
Ding Chongbin, Vice President of Absen
In 2019, due to its successful understanding and implementation of digital transformation, Absen was selected for inclusion in the 2019 China Digital Transformation Newcomer List published by the Institute for Global Industry at Tsinghua University. At that time, Vice President Ding Chongbin was also awarded the 2019 China Digital Transformation Pioneer prize, noting happily that, “We have been recognized by the industry for our strenuous efforts."
Furthermore, he mentioned creating a "Customer-Centered Organizational Process" was critical and went on to describe the need for transformation in the manufacturing industry and the essentiality of intelligence in manufacturing.
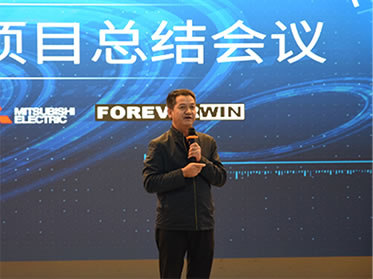
Ding Yanhui, Chairman of Absen
Chairman Ding Yanhui noted that Mitsubishi Electric focused on human resource development as part of the realization of intelligent manufacturing and that this was an important factor when selecting them as a partner.