Simulation tools MELSOFT Gemini
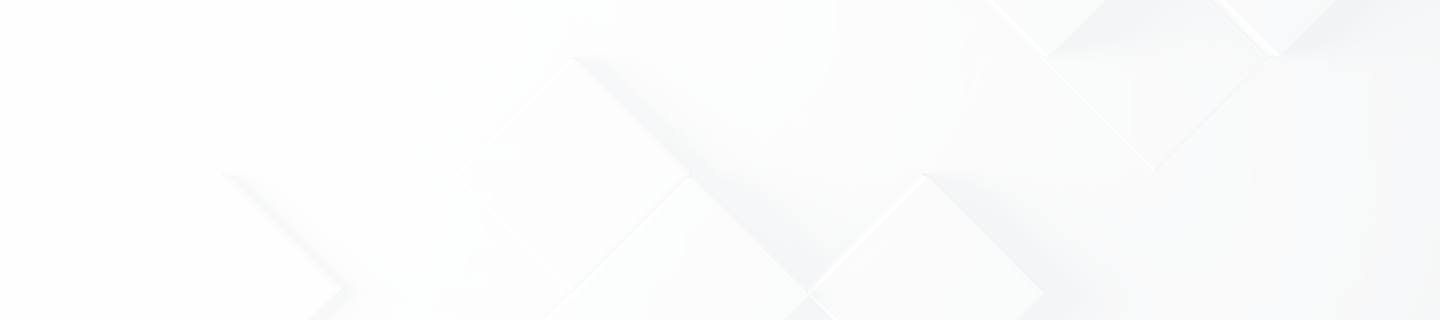
3D Simulators Are Ideal for Users with the Below Types of Concerns.
Introduction example01
Line Simulation EditionConstructed a system to increase production and reduced cycle time from 128 minutes per unit to 92 minutes per unit! (actual operation)
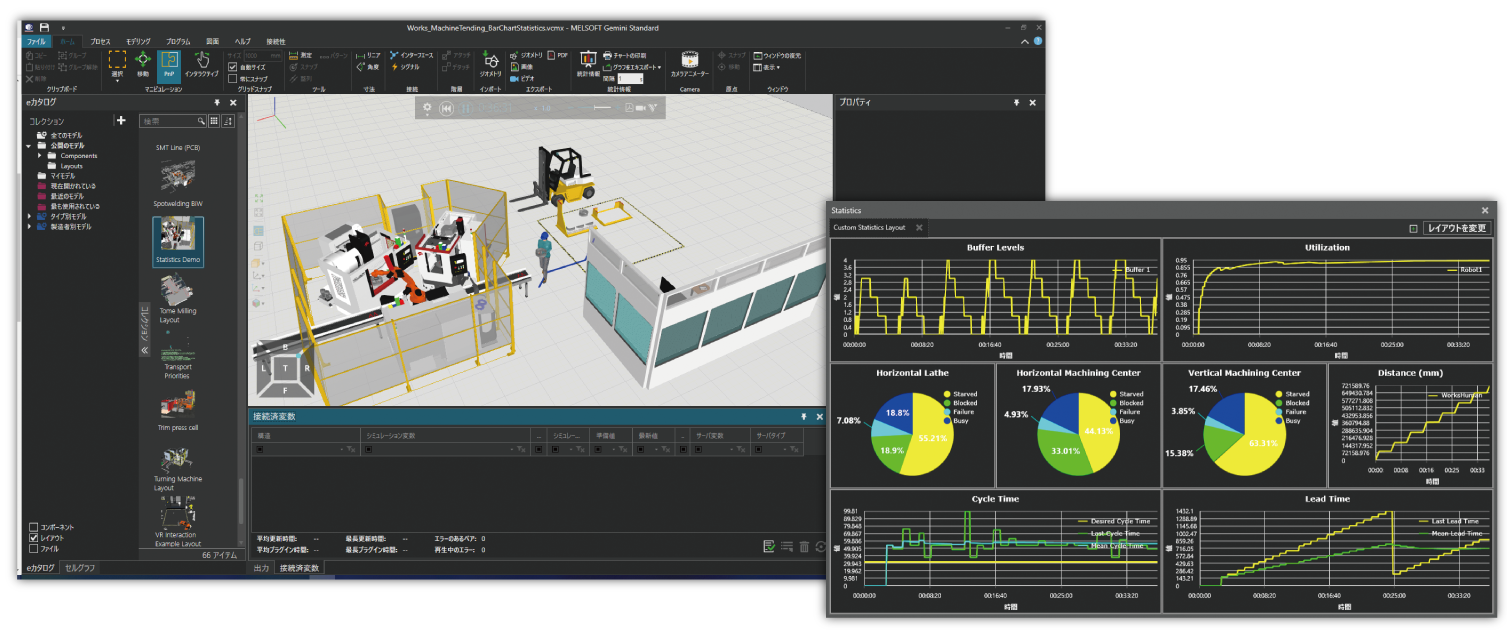
30%
reduction
Approximately 30% reduction
The system enables the construction of a line by placing 3D models from an extensive library of approximately 3,000 types of conveyors, robots, AGVs, personnel, etc., to perform optimal layout verification prior to actual line construction or modification.
In addition,the system can visualize the operating ratio for each process and piece of equipment in graph form, making it easy to identify areas for improvement during line modification and to compare the effects of each improvement measure.
Utilizing the line simulation function to easily perform pre-verification
Planning
Formulate improvement plans related to equipment, operator movement, etc.
Preparation
Reproduce current line based on line/work specifications
Verification
Verify effects of reproduced improvement proposal
Operation
Apply to actual factory lines for operation
Issue
The current production line could not keep up with the increase in demand, so there was an urgent need to increase production capacity.
The customer urgently needed to increase its production capacity therefore considered adding a manual work station however wants to verify the line change in advance and build a system to increase production without any need for rework.
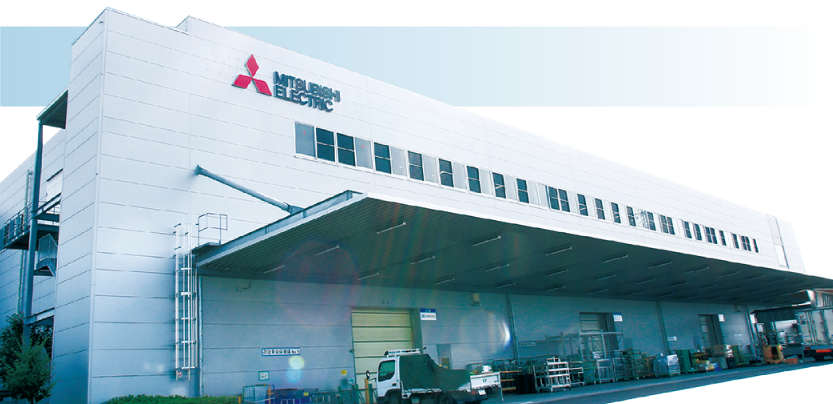
Example: Assembly line of Nagoya Works, Mitsubishi Electric
■Work station/5 locations (5 operators) ■Overhead crane/3 units ■Welding robot/2 units
Current | Unit production: 69 units/months | Cycle time: 128 min/unit |
Target | Unit production: 80 units/months | Cycle time: 103 min/unit |
Utilization flow
Planning
We wanted to increase the number of work stations from the current five to six and achieve a cycle time of 103 minutes/unit.
However, it was difficult to conduct preliminary verification, including detailed loss analysis, and using conventional Excel®-based calculations.
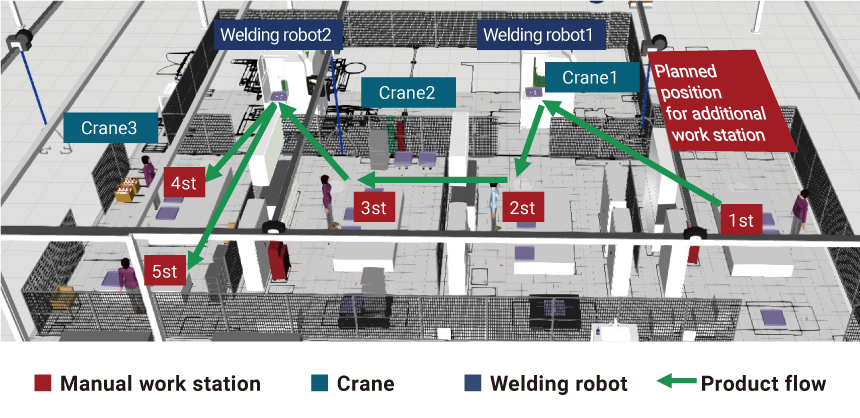
Preparation
MELSOFT Gemini was used to reproduce the current line based on line specifications (station layout, individual work time, etc.)
Current model construction was completed in around two days due to the abundance of 3D models already set up in the eCatalog.
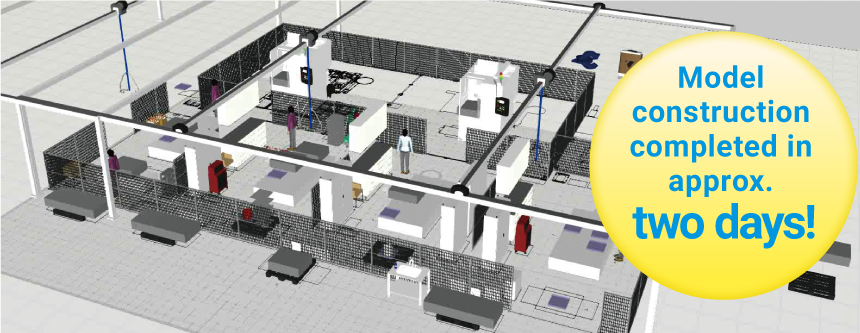
Verification
Cycle time was reduced to 99 min/unit with one additional work station and one additional operator.
A graph function detected idling losses that were previously unnoticeable, and the installation of an intermediate work station eliminated these losses.
In actual operation, cycle time was reduced to 92 min/unit, thus increasing production capacity.
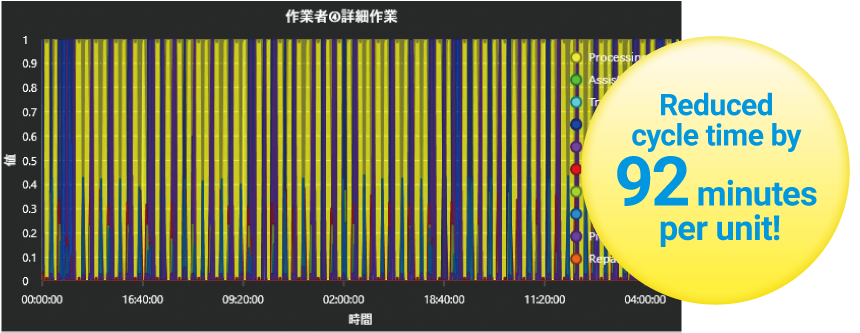
Operation
Based on the simulation results of MELSOFT Gemini, the target production volume of 80 unites/month was achieved.
In addition, idling loss was eliminated by installing an intermediate work-in-process stand which saved approx. JPY600,000 annually.
Due to the high accuracy of the preliminary verification, rework was reduced by redesign and additional work.
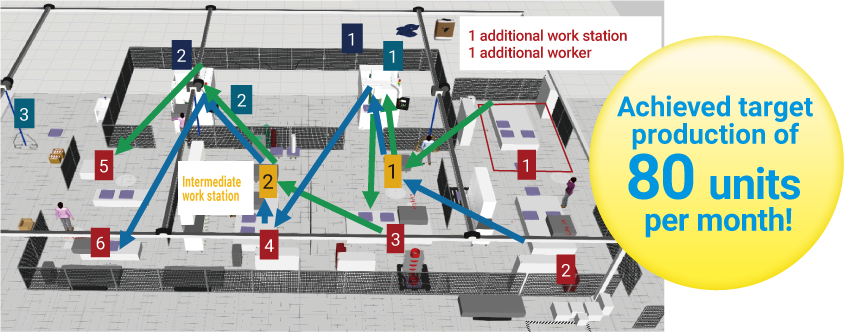
Benefits of introduction
Able to verify improvement using multiple patterns
Simulations can easily be adjusted, therefore multiple improvement patterns can be swiftly verified.
Easy to review due to visualization of improvements
Observe process waste in 3D, utilize screen recording, operating ratio chart, etc. during simulations.
Prevent time loss due to rework
If the production line is actually modified based on Excel® trial calculation values, there is a possibility that a study into the improvement method will need to be repeated.
Higher productivity
Lower cost
Less labor time
Verifies worker flow lines and line layouts of the assembly line in advance.
As a result, we were able to establish a system to increase production without rework!
Introduction example02
Equipment Simulation EditionRealizing front-loading in a digital space to reduce overall construction time from 40 to 34 weeks!
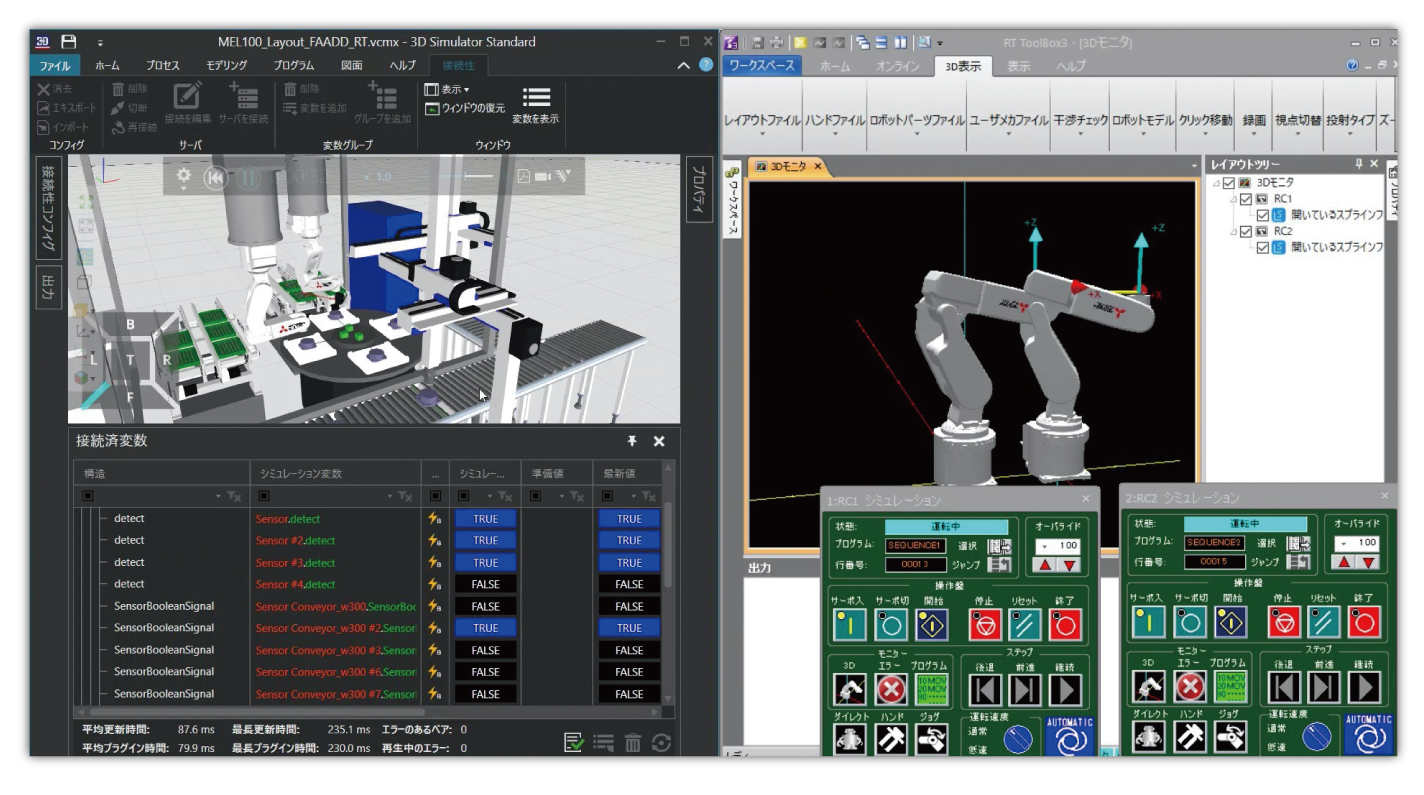
6 weeks
Reduction of 6 weeks
Control logic can be verified in 3D operation by connecting to engineering tools such as programmable controllers and robots, as well as Mitsubishi Electric FA equipment.
By identifying problems in advance, such as mechanical collision and robot motion during control execution, the system greatly reduces on-site engineering labor time.
Direct connection to FA equipment and various tools for smooth collaboration
Verification items
Control program debugging
Verification items
Teaching
+
collision check
Verification items
Program verification for cycle time reduction
Issue
Delays in upstream mechanical design put pressure on the overall process schedule and did not allow enough time for debugging using actual equipment for downstream control design, which required a lot of on-site adjustment time.
We want to perform equipment simulation in advance to achieve front loading!
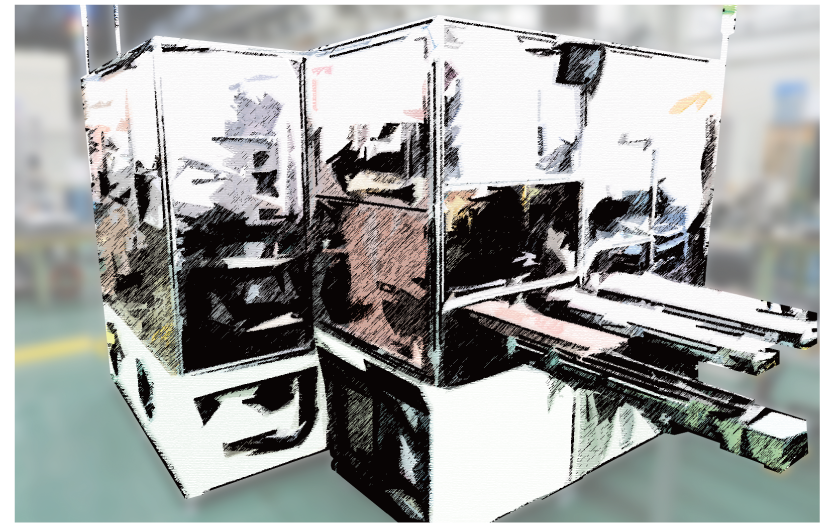
Utilization flow
Control program debugging
Operations of the control program can be visually confirmed with a 3D model, and defects that were difficult to notice only in the program can be identified.
Debugging of control programs without the use of actual equipment is now possible.
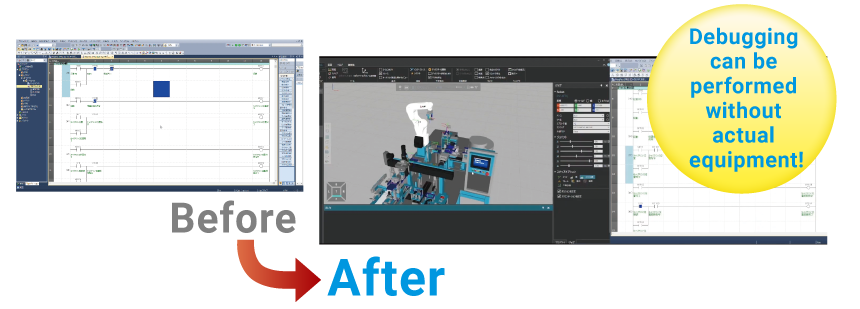
Teaching + collision check
MELSOFT Gemini is used to perform teaching work and faithfully simulate actual robot operations such as paths and range of motion.
This means that teaching and collision check can be completed in advance without actual machine.
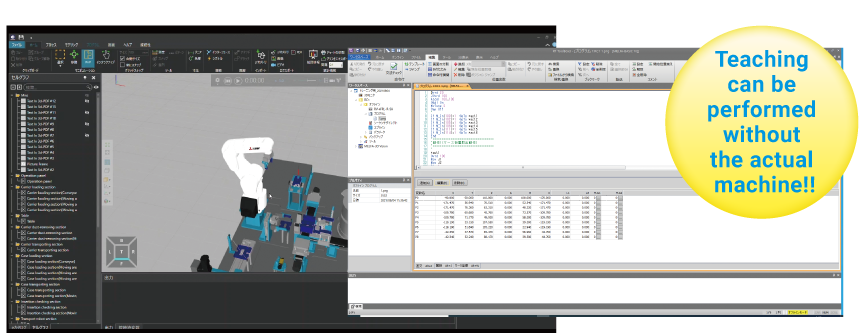
Program verification for cycle time reduction
Carrier transfer is performed in parallel with robot operation, preventing operation loss.
Because wasteful movements were identified and improved at the design stage, the cycle time was reduced by 30 seconds, from 1 minute and 20 seconds to 50 seconds.
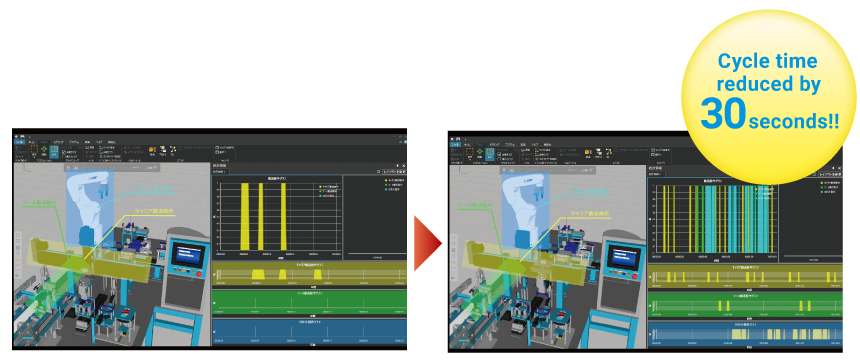
Benefits of introduction
Reduced on-site engineering labor time
Because verification is possible with a 3D model, less time is required for debugging and on-site engineering.
Enables accurate and rapid collision check
Linkage with RT ToolBox3 prevents equipment damage due to collision and reduces on-site adjustment and start-up time.
Reduces cycle time before going to the production shop floor
Because wasteful movements were identified and improved at the design stage, cycle time was reduced before going to the production shop floor.
■Cost-effectiveness(e.g.)
-
Introduction cost
MELSOFT Gemini
- License cost
- Training cost
- Labor cost for development upon utilization
-
Build period
Reduced by approx.
6 weeks
*If the daily SI cost is 80,000 yen, the cost reduction is 2.4 million yen for a 6-week x 5-day operation. -
Introduction benefit
6-weeks’ worth of production profit by reducing start-up time
*If daily production profit is 1.6 million yen, profit increase is 48 million yen for 6 weeks x 5 working days. -
Payback period
Approx. 5 days
*Assuming an introduction cost of approximately 10 million yen, a cost reduction of 2.4 million yen due to a reduced build period, and an introduction benefit of 1.6 million yen per day.
Validate machine operation in virtual space and improve the validity of control logic before setting up in the field.
Achieve shorter set-up time by frontloading development