Industrial robot MELFA FR PLUS
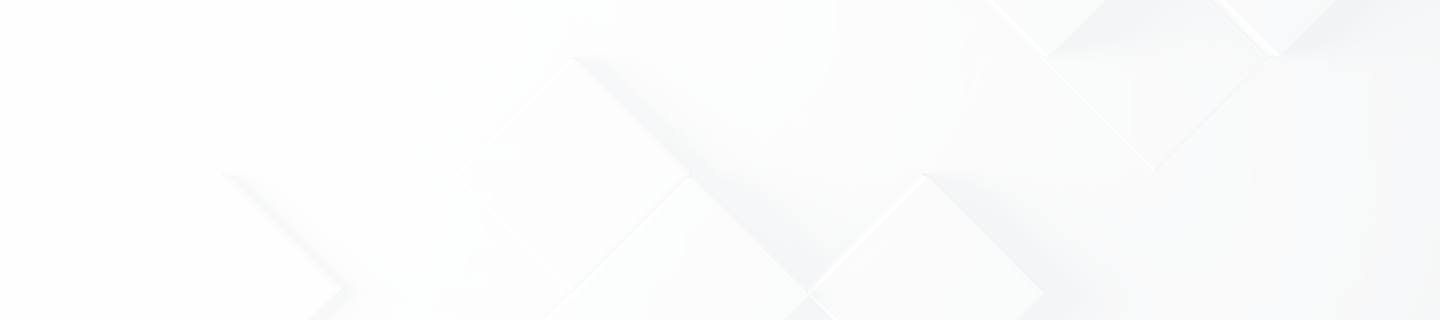
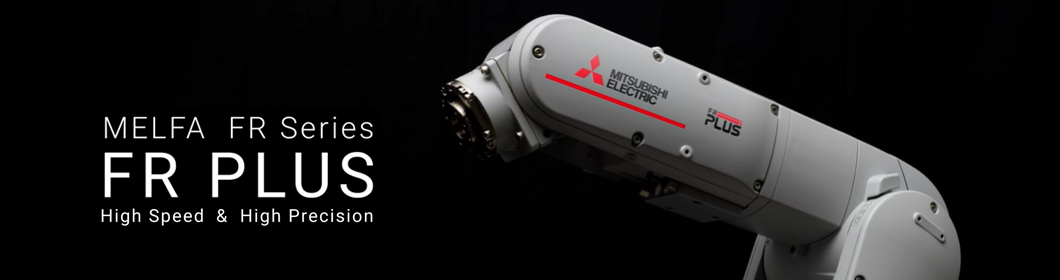
MELFA FR PLUS introduction
Advanced features maximizing FR series performance, further improving accuracy, efficiency, and quality
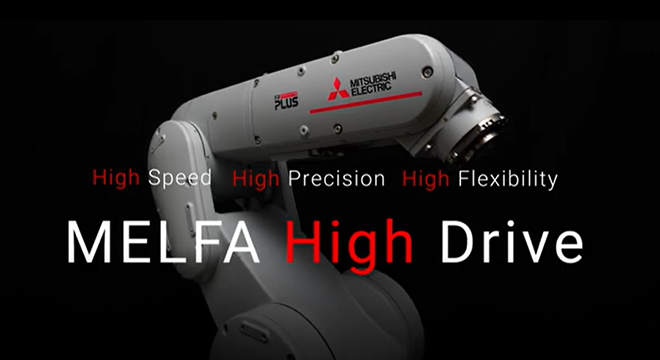
MELFA FR series FR PLUS offers reduced positioning time and improved trajectory accuracy with the "MELFA High Drive function" and supports a wider range of applications with "expanded force sensor lineup".
These features flexibly meets the need of each customer's manufacturing processes and contributes to high productivity and quality.
*Please refer to the catalog for details.
Lineup
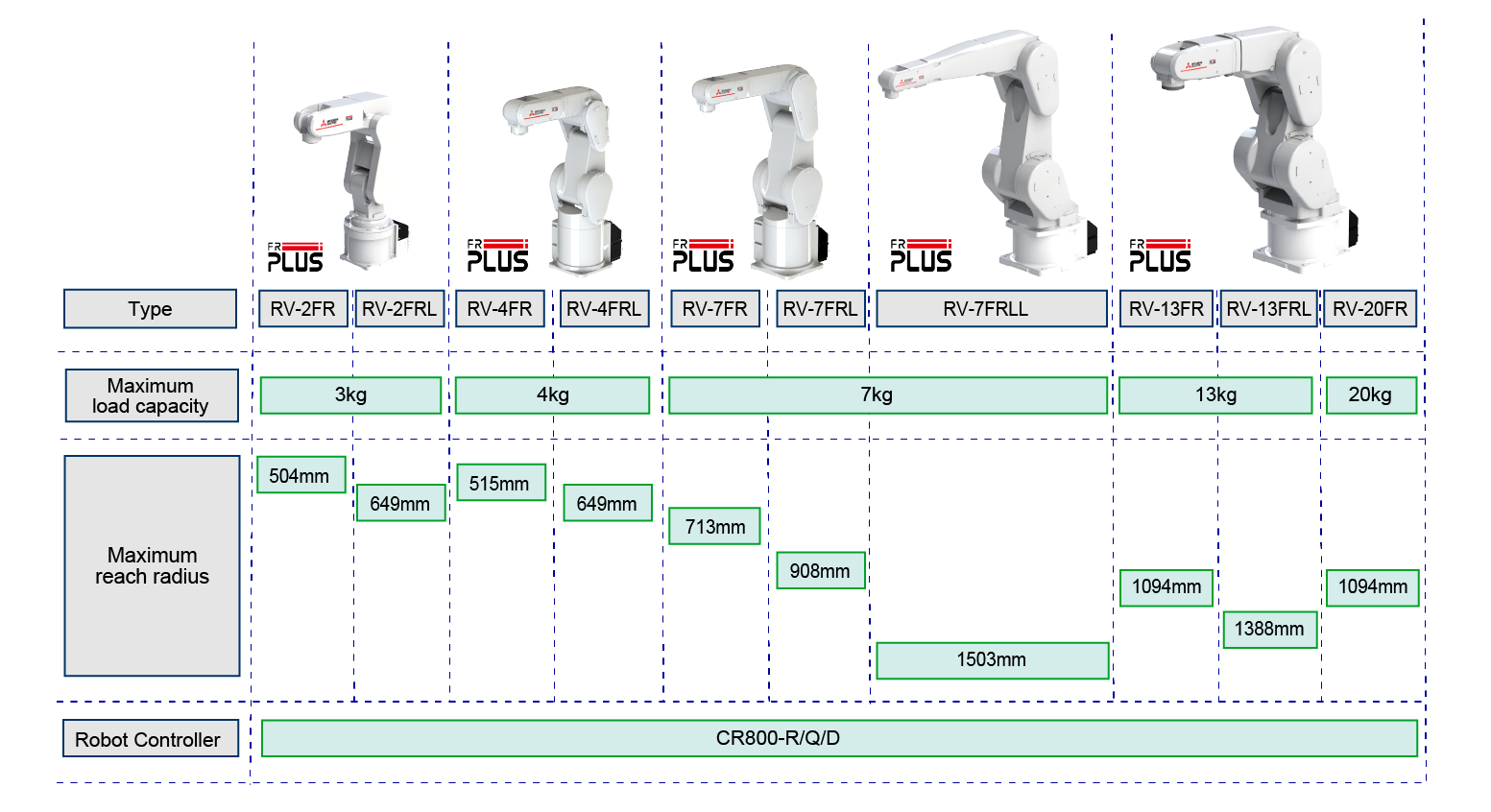
*1:Supported models are planned to be expanded as needed.
MELFA High Drive Function
Reduced positioning time
The vibrations that occur during positioning can be suppressed by using Mitsubishi Electric's unique vibration control algorithm. This enables a 30% reduction of the positioning settling time (*2), improving the cycle time.
The improved cycle time leads to improved productivity.
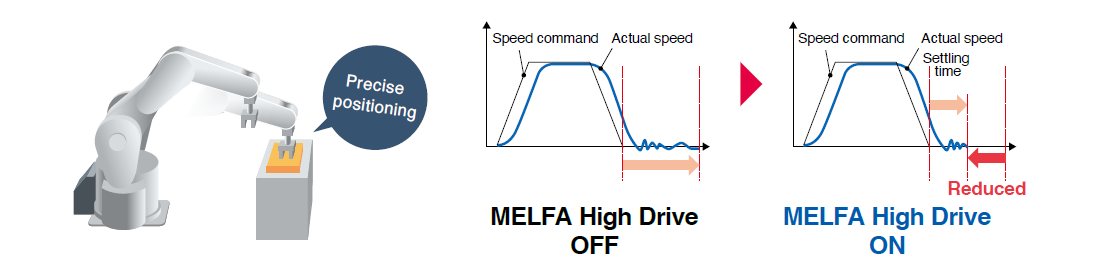
Check the video that introduces the Mitsubishi Electric "vibration suppression" that realizes the MELFA High Drive function.
High-accuracy trajectory control
The trajectory accuracy is improved with trajectory compensation control. Setup adjustment has become easier since the trajectory fluctuation due to the speed and position less occurs.
Furthermore, this function improves work quality, such as sealing process.
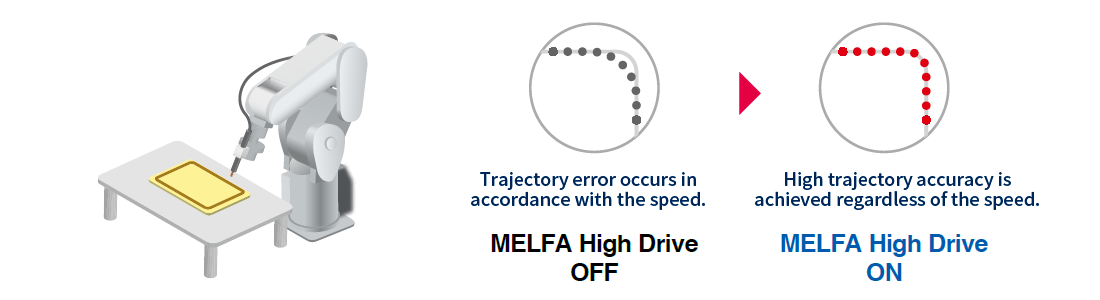
Comparison of trajectory accuracy when MELFA High Drive function is turned ON/OFF
The trajectory accuracy is improved up to 64% when the MELFA High Drive function is ON compared to when it is OFF. (*2)
It is now possible to maintain machining accuracy while shortening machining time.
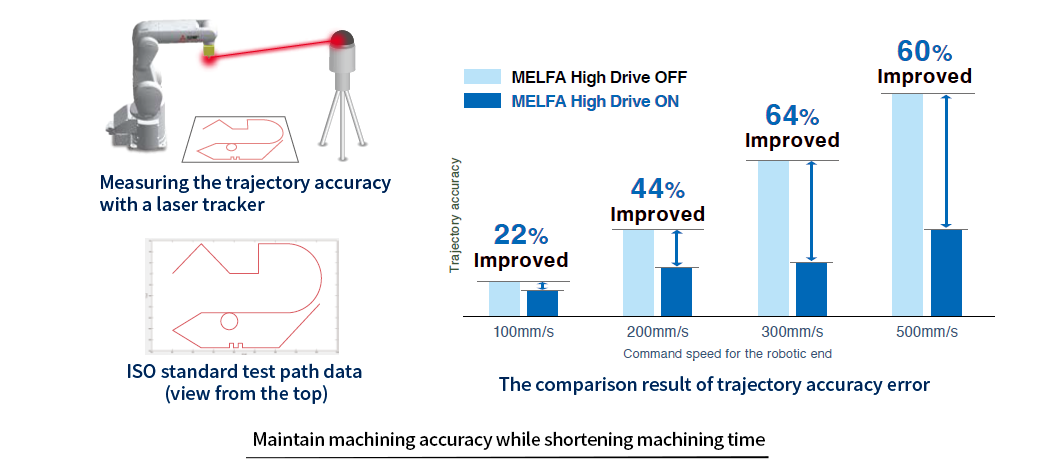
An enlarged diagram when the test path is a circle
The trajectory accuracy has been improved by the MELFA High Drive function. (*2)
It makes fine tuning and teaching easier.
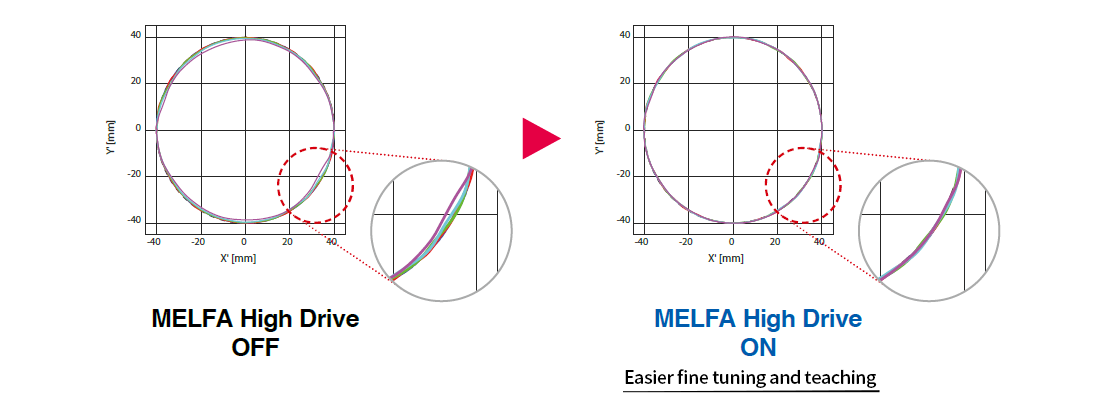
*2: This value indicates the measurement result in our environment. The improvement rate varies depending on the environment of each customer.
Expanded force sensor lineup
With the collaboration of our robot software technology and the partner companies, a wider range of applications is supported to meet the need of each customer's manufacturing processes.
Canon U.S.A., Inc.
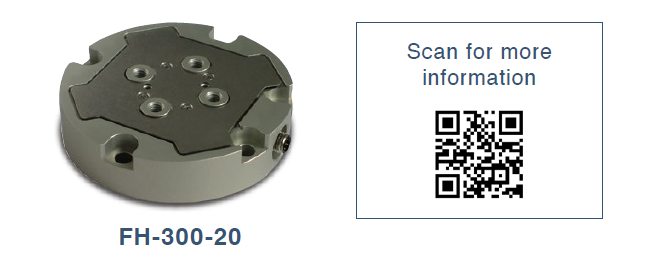
FH-300-20
Equipped with an optical encoder, FH-300-20 achieves precise force control with a thin, lightweight design and low noise.
- For details of the specifications and installation method, refer to the standard specifications of the force sensor.
- If you would like more information about Canon force sensors, please contact your local Canon or distributor.