Robot Engneering software (MELFA)MELSOFT RT ToolBox3
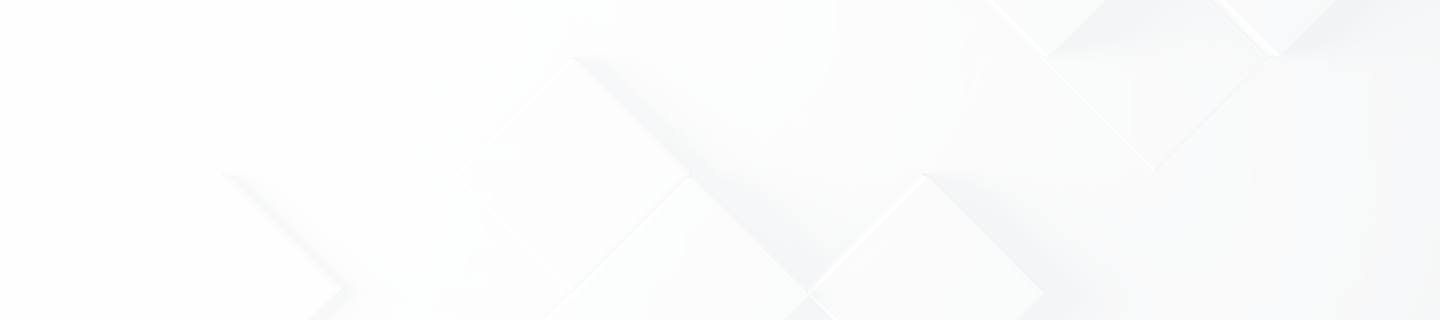
Program editing and debugging functions
- Programs can be edited using MELFA-BASIC IV, V, and VI.(varies depending on the model).
- Improvement of work operations by a multi-window format and the various editing functions.
- This is helpful for use in checking operations such as the execution of program steps, setting of breakpoint settings, and other tasks.
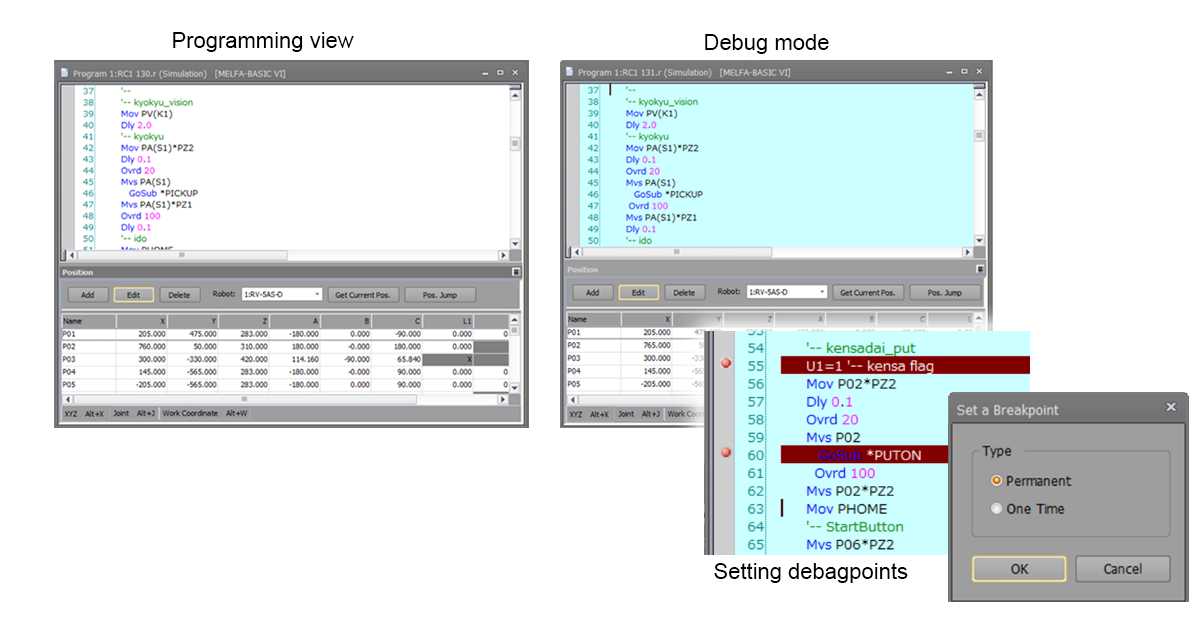
MELFA-BASIC VI
- As well as providing a more complete set of commands, this uses structured programming to give high levels of reusability and readability.
- Allows structured programs, enabling programming with high levels of reusability and readability.
- Keeping a library of program processing allows knowledge to be accumulated and provides improved reusability.
The libraries can also be hidden to prevent knowledge from being disclosed.
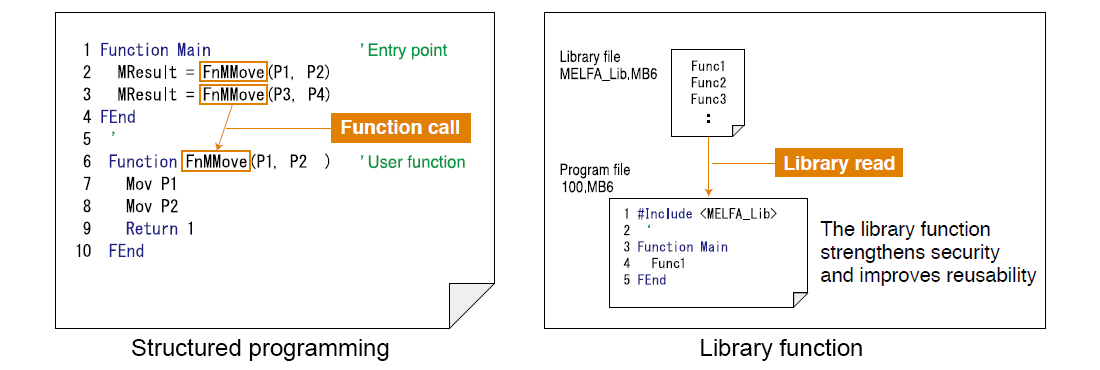
3D viewer
- The 3D viewer allows easy verification of robot poses and movements, verification of the limit values of user-defined parameters, and virtual placements of peripheral devices by basic objects.
- It can also be used to check for interferences between the robot and peripheral devices.
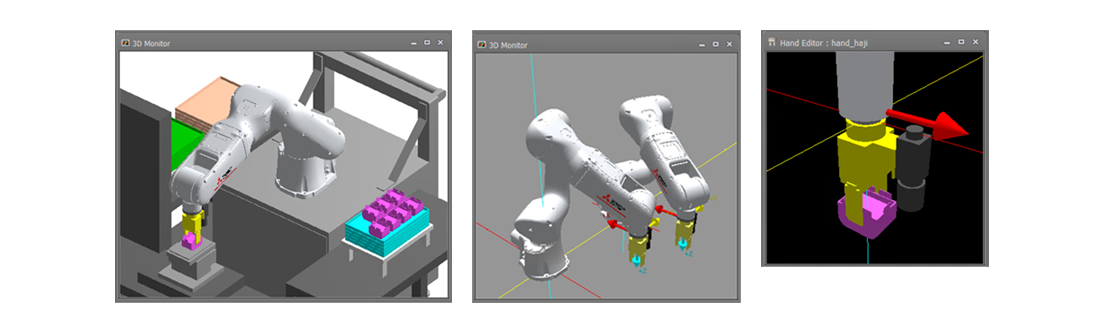
Simulation functions
Robot programs, including I/O signals, can be simulated in the PC, movements can be verified, and the cycle time of robot operations can also be measured.
That is, the operations of the actual system can be reproduced as they are. Such simulation functions are also effective for preliminary system examinations.
- A maximum of 8 robots can be operated, and coordinated movements among robots can be verified.
- Servo simulations can also be performed, for preliminary examination of loads.
- Signals can be coordinated with GX works2 and GX works3 for easy creation of line simulators.
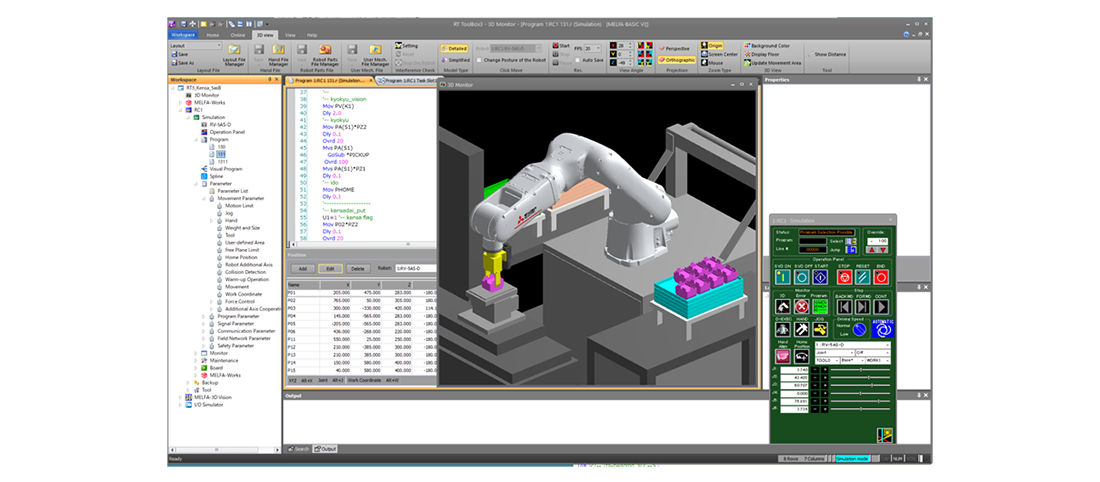
MELFA-Works function
The MELFA Works function can be used in RT ToolBox3 Pro.
MELFA Works, an add-in tool of SolidWorks®, can simulate robot production systems on SolidWorks® and output the data of processing paths on workpieces.*1)
*1) SolidWorks® is a registered trademark of SolidWorks Corp, (USA). An add-in tool is a software program that adds certain functions to application software packages.
Main functions
- Simulation of robot operations
Robot programs, including I/O signals, can be simulated on SolidWorks®. That is, the operations of the actual system can be reproduced as they are. - Cycle time
The cycle time of robot operations can be measured. - Interference checks
Interferences between the robot and peripheral devices can be checked. - CAD links
Work data for performing sealing operations and other such tasks that require many teaching steps can be easily created by selecting the processing area on the 3D CAD data. Since work data is created from 3D CAD data, even complex 3D curves can be generated. - Calibration
The point sequence data of CAD coordinates created using CAD links is corrected into robot coordinate data, and the operation program and point sequence data are sent to the robot.
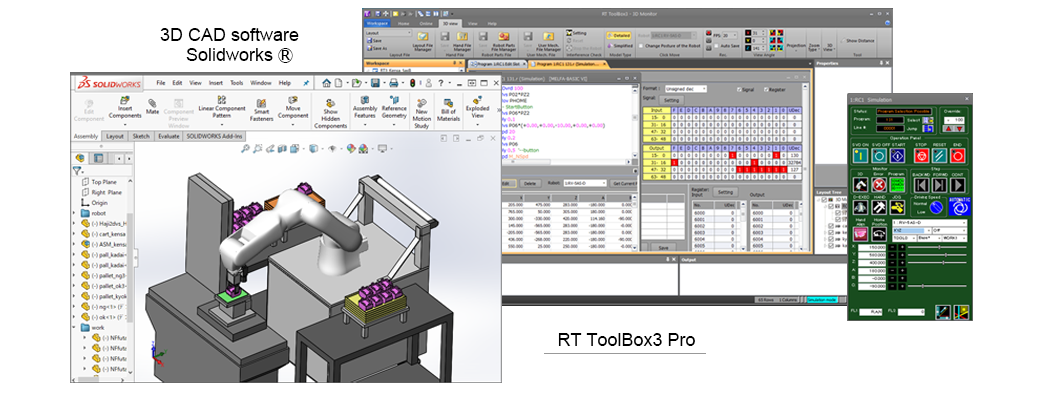
Visual programming
RT ToolBox3 includes the visual programming function of RT VisualBox, which enables intuitive operations. It is easy to start up robots even without knowledge of robotics.
It also supports simulation, allowing you to perform motion confirmation and interference checks of programs created with visual programming on a 3D layout.
- It is easy to start up robots even without knowledge of robotics.
- It also supports simulation, allowing you to perform motion confirmation and interference checks of programs created with visual programming on a 3D layout.
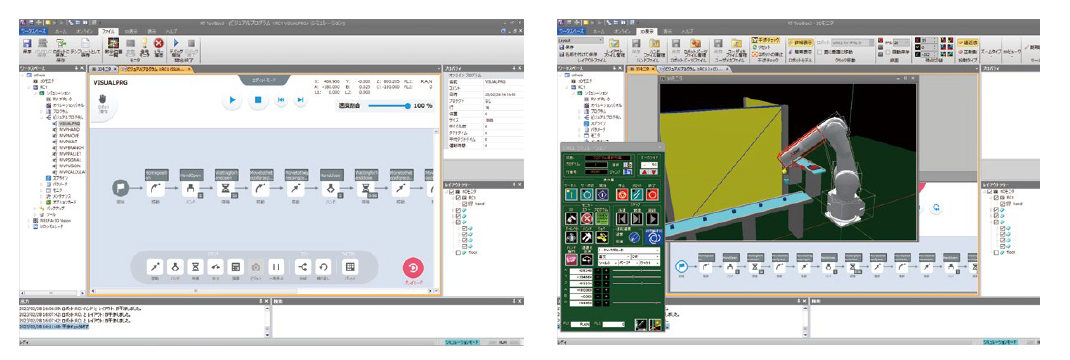