MELSERVO-J5 Series Servo Amplifier Safety Sub-Functions
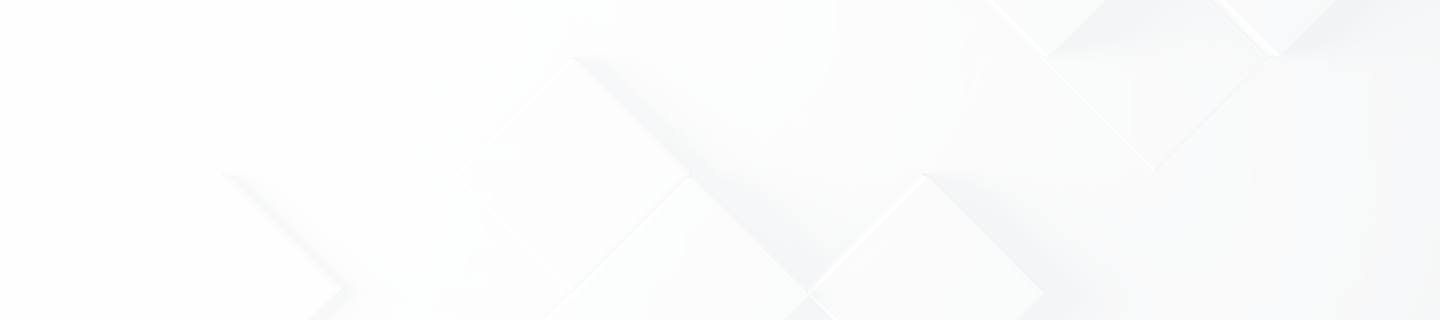
-
<
- 製品情報
Safety Sub-Functions
Specifications of servo amplifiers
Item | Specifications | ||
---|---|---|---|
MR-JET-G4-HS(N1) | |||
Safety performance |
Standards | EN ISO 13849-1:2015 Category 4 PL e, IEC 61508 SIL 3, EN IEC 62061:2021 maximum SIL 3, EN 61800-5-2 |
|
Mean time to dangerous failure (MTTFd) |
MTTFd ≥ 100 [years] (300a) | ||
Diagnostic coverage (DC) | DC = Medium, 96.5 % | ||
Probability of dangerous Failure per Hour (PFH) |
PFH = 7.7 × 10-9 [1/h] | ||
Mission time (TM) (Note 1) | TM = 20 [years] |
- Notes:
- 1. The performance of special proof tests within the mission time of the product is regarded as not necessary, however, the diagnostic interval is suggested as at least one test per three months for Category 3 PL e, SIL 3 on IEC 61800-5-2:2016.
Function specifications
Item | Specifications | ||
---|---|---|---|
MR-JET-G4-HS(N1) | |||
Safety sub-functions | STO | Shut-off response time (STO input off → energy shut off) |
8 ms or less (using input device) 60 ms or less (using CC-Link IE TSN/EtherCAT®) (Note 1, 4, 5) |
SS1 | Deceleration delay time | 0 ms to 60000 ms (functional safety parameter setting) | |
SBC | Shut-off response time | 8 ms or less (using input device) 60 ms or less (using CC-Link IE TSN/EtherCAT®) (Note 1, 4, 5) |
|
SLS1/2/3/4 | Observation speed | 0 r/min (mm/s) to 10000 r/min (mm/s) (functional safety parameter setting) (Note 6) | |
SSM | Observation speed | 0 r/min (mm/s) to 10000 r/min (mm/s) (functional safety parameter setting) | |
SDI | Direction monitor delay time | 0 ms to 60000 ms (functional safety parameter setting) | |
SLT | Observation torque | -1000.0 % to 1000.0 % (functional safety parameter setting) | |
Input/output function | Input device |
Number of inputs (double wiring) | 3 points |
Permissible time for mismatched double inputs | 0 ms to 60000 ms (functional safety parameter setting) (Note 8) | ||
Noise elimination filter | 1.000 ms to 32.000 ms (functional safety parameter setting) | ||
Test pulse off time (Note 7) | 1 ms or less | ||
Test pulse interval (Note 7) | 250 ms to 1000 ms | ||
Output device |
Number of outputs (double wiring) | 3 points | |
Test pulse off time | 0.500 ms to 2.000 ms (functional safety parameter setting) | ||
Test pulse interval | 1 s or less | ||
Safety communication function |
Response time | 250 ms (Note 2) | |
Transmission interval monitor time | 16.0 ms to 1000.0 ms (functional safety parameter setting) (using CC-Link IE TSN) (Note 1) | ||
FSoE Watchdog Time | 16.0 ms to 65534.0 ms (object setting) (using EtherCAT®) (Note 1) | ||
Safety communication delay time | 60 ms or less (using CC-Link IE TSN/EtherCAT®) (Note 1, 4) |
- Notes:
- 1. The listed value is applicable when the safety sub-functions through the network connection are executed.
- 2. This value is applicable when the transmission interval monitor time is 64.0 ms or less, or FSoE Watchdog Time is 60 ms or less.
- 3. The performance of special proof tests within the mission time of the product is regarded as not necessary, however, the diagnostic interval is suggested as at least one test per three months for Category 3 PL e, SIL 3 on IEC 61800-5-2:2016.
- 4. This value is applicable when the transmission interval monitor time is 32.0 ms or less, or FSoE Watchdog Time is 30 ms or less.
- 5. Set the communication cycle as follows:
-
- ●MR-JET-G4-HS: 125 μs or more
- ●MR-JET-G4-HSN1: 250 μs or more
- 6. The observation speed can be set separately.
- 7. The test pulse is a signal for the external circuit to perform self-diagnosis by turning off the signals to the servo amplifier instantaneously at regular intervals.
- 8. If it is set to 0 ms, no alarm occurs.
List of supported safety sub-functions
Servo amplifier model |
Connection method (connector) |
Servo motor type | Safety sub-function (IEC/EN 61800-5-2) | |||||||
---|---|---|---|---|---|---|---|---|---|---|
STO | SS1 | SBC | SLS (Note 3) |
SSM (Note 3) |
SDI (Note 3) |
SLT | ||||
SS1-t | SS1-r (Note 3) |
|||||||||
MR-JET-G4-HS(N1) | DI/O connection (Note 2) (CN3) |
Rotary servo motor | Cat. 4 PL e, SIL 3 |
Cat. 4 PL e, SIL 3 |
Cat. 3 PL d, SIL 2 |
Cat. 4 PL e, SIL 3 |
Cat. 3 PL d, SIL 2 |
Cat. 3 PL d, SIL 2 |
Cat. 3 PL d, SIL 2 |
Cat. 3 PL d, SIL 2 |
Network connection (Note 1, 4, 5) (CN1A/CN1B) |
- Notes:
- 1. Combine the servo amplifier with an R_SFCPU safety CPU with firmware version 20 or later.
- 2. The listed safety levels are applicable when the following executes safety sub-function control with a diagnosis using test pulses.
- ● Safety CPU or safety controller that meets Category 4 PL e, SIL 3
- When a forced stop switch, a safety switch, or an enable switch is directly connected to the servo amplifier and a diagnosis using test pulses is not executed, the safety level is Category 3 PL d, SIL 2.
- 3. A fully closed loop system does not support SS1-r, SLS, SSM, and SDI.
- 4. The safety sub-functions through the network connection are not available when the servo amplifiers use CC-Link IE Field Network Basic.
- 5. Set the communication cycle as follows:
- ● MR-JET-G4-HS: 125 μs or more
- ● MR-JET-G4-HSN1: 250 μs or more