Simple Motion module Features
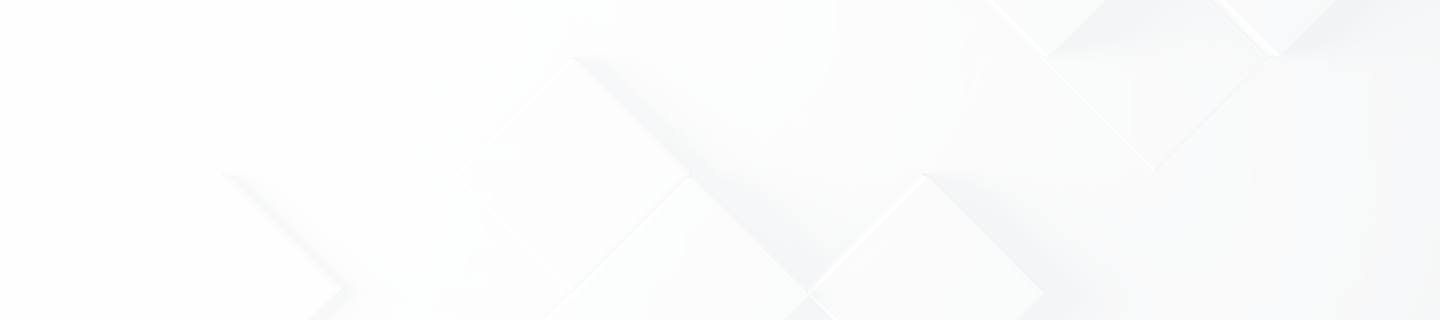
FX5-80SSC-S/FX5-40SSC-S
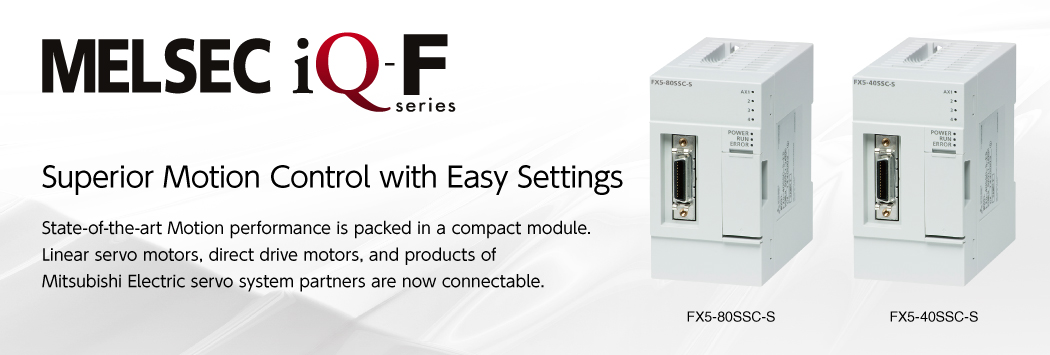
- Features
- SSCNETIII/H
- Positioning Control
- Synchronous/Cam controls
- Mark Detection Function
- Engineering Environment
- Functions List
- Related Link
Features
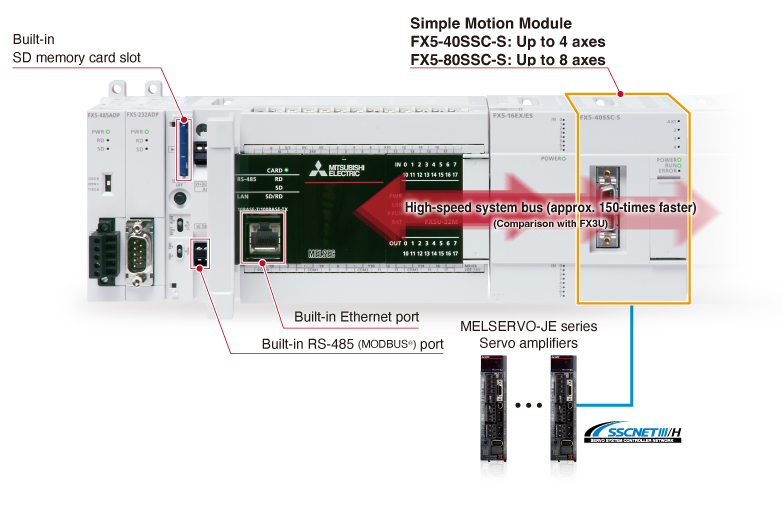
Synchronous/Cam Controls Contribute to Higher Performance of Small-sized Equipment
The Simple Motion module is provided with synchronous and cam controls required for food processing machines and packaging machines. Combined with the Mitsubishi Electric's high-performance servo amplifier, the Simple Motion module enables downsizing of machinery while achieving outstanding performance. In addition, our extensive engineering environment allows you to create desired systems with ease.
Central Control via SSCNETIII/H Boosts Efficiency in Startup
The Simple Motion module can consolidate multiple servo amplifier parameters, shortening the startup time further. Also, operation information, such as power consumption and total power consumption of the servo amplifiers, can be monitored in real time, which enables further reduction in maintenance time.
Connection with various drive products
Not only rotary servo motors but also linear servo motors, direct drive motors, FR-A800 series inverters, and products of Mitsubishi Electric servo system partners are connectable.
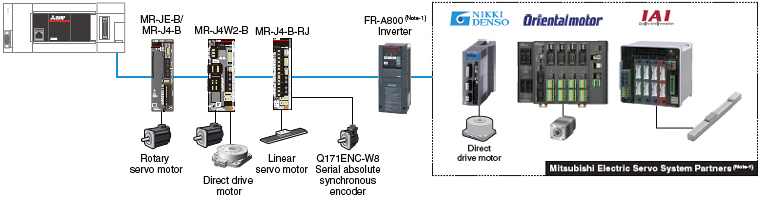
- (Note-1):
- When using a partner product or the inverter FR-A800, use one whose version supports the Simple Motion module.
The Simple Motion Module Opens up Many Possibilities for Higher Performance
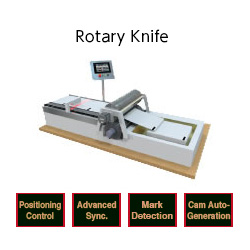
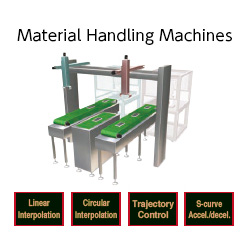
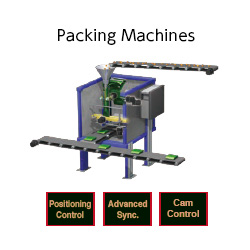
High-speed Synchronous Network SSCNETIII/H
- Communications speed is increased to 150 Mbps full duplex (equivalent to 300 Mbps half duplex), three times faster than the conventional speed.
System response is dramatically improved. - Smooth control of a machine is possible using high-speed serial communications with a cycle time of 0.222 ms.
- Synchronous communications are achieved with SSCNETIII/H, offering technical advantages for machines that require deterministic control.
- Long distance wiring is possible up to 3200 m (10498.69 ft.) per system (maximum of 100 m (328.08 ft.) between stations x control axes up to 32 axes), suitable for large-scale systems.
- SSCNETIII/H compatible and SSCNETIII compatible servo amplifiers can be used together.
(The communications speed when SSCNETIII compatible products are used together in the same system: 150 Mbps full duplex)- (Note):SSCNET (Servo System Controller Network)
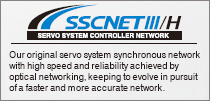
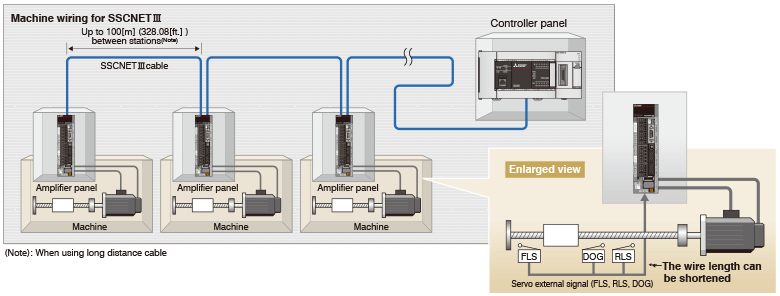
Positioning Control
Positioning control is easily performed with a sequence program starting positioning data of a point table. To respond to extensive applications, various positioning controls are available: Linear interpolation, 2-axis circular interpolation, fixed-pitch feed, and continuous trajectory controls, etc.
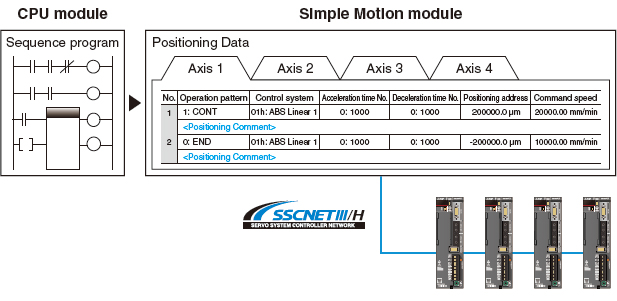
Synchronous/Cam controls
Advanced synchronous control
The advanced synchronous control is software-based synchronous control as an alternative to mechanical control, such as gear, shaft, clutch, speed change gear and cam. In addition, cam control becomes even easier with cam auto-generation function.
The synchronous control can be flexibly started/ended for each axis, allowing the synchronous control axis and positioning control axis to be used within the same program.

- [Command generation axis]
- Command generation axis is the axis that performs only the command generation.
It is controlled independently of other axes connected to servo amplifiers. (not counted as a control axis)
Cam auto-generation
Cams for rotary knife can be generated automatically.
An ideal cam data can be created just by registering sheet length, synchronous width, and cam resolution to the specified device memory on GOT screen.

Mark Detection Function
The actual position of the servo motor can be obtained based on the inputs from the sensor that detects the registration marks printed on the highspeed moving film. By compensating the cutter axis position errors based on those inputs from the sensor, the film can be cut at the set position.
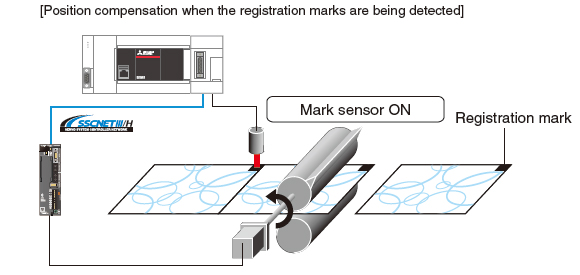
Engineering Environment
Easy point-and-click programming architecture MELSOFT GX Works3
This software supports the whole product development cycle - creation, startup, debugging and maintenance of sequence programs, parameters, positioning/cam data.
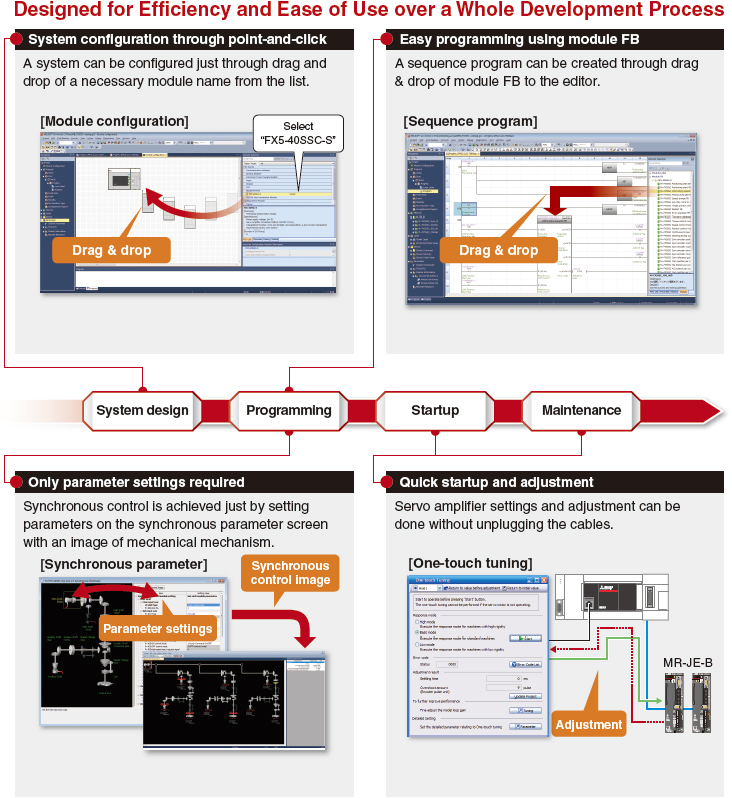
Functions List
Simple Motion Module | |||
---|---|---|---|
FX5-80SSC-S | FX5-40SSC-S | ||
Number of control axes | Up to 8 axes | Up to 4 axes | |
Servo amplifier connection method | SSCNETIII/H (150Mbps) | ||
Maximum distance between stations [m(ft.)] | 100 (328.08) | ||
Connectable servo amplifier | MR-J4-B(-RJ), MR-J4W-B More details MR-JE-BMore details |
||
Operation cycle[ms] | 0.888, 1.777ms | ||
Engineering Environment | MELSOFT GX Works3 (Simple Motion module setting function) | ||
Control modes | Positioning control, Position control, Speed control, Torque control, Speed-torque control, Cam control, Advanced synchronous control, Linear interpolation (up to 4 axes), Circular interpolation (2 axes), Trajectory control, Speed-position switching control (ABS/INC), Position-speed switching control (INC) | ||
Control unit | mm, inch, degree, pulse | ||
Number of positioning data | 600 data (positioning data No. 1 to 600)/axis | ||
Acceleration/deceleration process | Trapezoidal acceleration/deceleration, S-curve acceleration/deceleration |
||
Manual control | JOG operation, Manual pulse generator operation, Inching operation | ||
Functions that change control details | Current value change, Target position change function, Torque change function, Speed change function, Override function, Acceleration/deceleration time change function |
||
Home position return method | Proximity dog method, Count method 1, Count method 2, Data set method, Scale home position signal detection method, Driver home position return (Note-1) |
||
Auxiliary functions | Forced stop function, Hardware stroke limit function, Software stroke limit function, Absolute position system, Amplifier-less operation function, Unlimited length feed, Optional data monitor function, Mark detection function, Flash ROM backup, M-code output function, Digital oscilloscope function, Cam auto-generation function |
||
Number of I/O occupying points | 8 points | ||
24VDC external current consumption [A] | 0.25 | ||
Mass [kg] | 0.30 |
- (Note-1):
- The home position return method set in a driver (a servo amplifier) is used.