Motion module Features
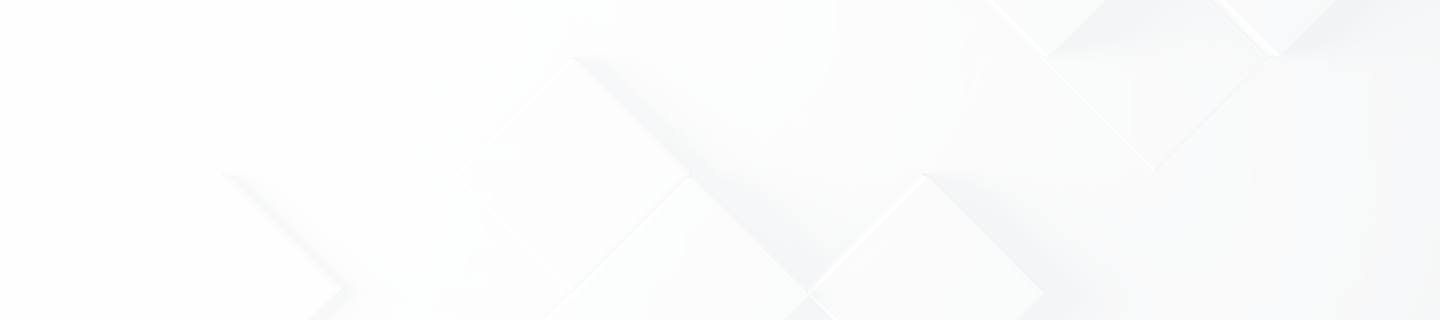
FX5-80SSC-G/FX5-40SSC-G
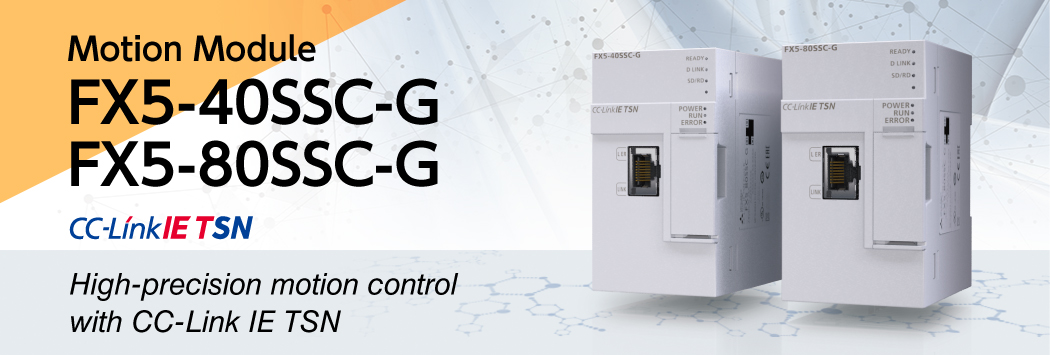
- Concept
- Features
- Positioning Control
- Advanced synchronous control
- Speed-Torque Control
- Auxiliary Features
- Engineering Environment
- CC-Link IE TSN
- Servo Amplifier MELSERVO-J5/MELSERVO-JET
- Functions List
- Related Link
Concept
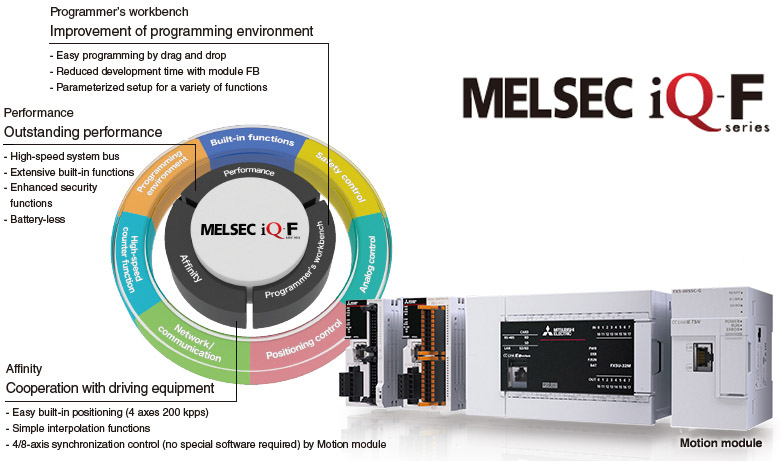
Features
Combined with a CC-Link IE TSN-compatible servo amplifier, the Motion module offers a high-performance servo system that improves machine capability.
- Performs advanced motion control, such as positioning, synchronous, cam, and speed-torque control.
- Connects remote I/O modules and FR-A800-GN inverters via CC-Link IE TSN. The data of these devices can be read/written by a CPU module.
- Connects TCP/IP devices, enabling a flexible system configuration.
- Possible to reuse the existing projects of the MELSEC iQ-F series Simple Motion modules (previous model).
The Motion module enables advanced motion control while offering cost-effectiveness.
The module has the capability and functions required for stand-alone/small-scale systems.
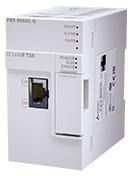

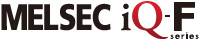
FX5-40SSC-G
FX5-80SSC-G
- Maximum number of control axes:
4 axes/module (FX5-40SSC-G), 8 axes/module (FX5-80SSC-G) - Minimum operation cycle*1: 500 [μs]
- Maximum number of connected modules*2: 4 modules/system
- Compatible servo amplifiers
MR-J5-G MR-J5D-G4 MR-JET-G
- *1.The operation cycle varies by the number of control axes and the models.
- *2.This refers to the total number of the Motion modules and one FX5-CCLGN-MS (master station).
Reuse of Existing Projects
The existing projects of a Simple Motion module can be reused. This enables reduction in program development time.
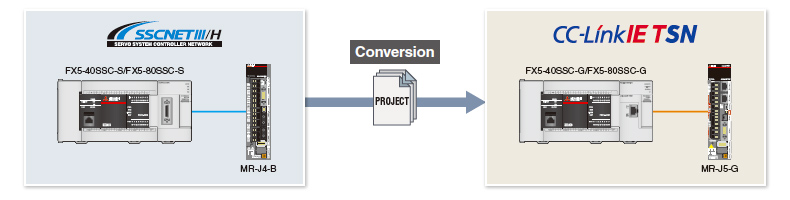
- *Parameter settings for the network and servo amplifiers are required.
Positioning Control
The Motion module executes various positioning control, such as trajectory control that combines linear and circular interpolation and speed-position switching.
Linear interpolation
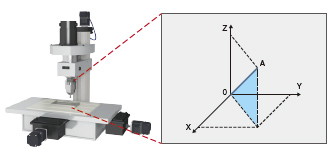
Circular interpolation
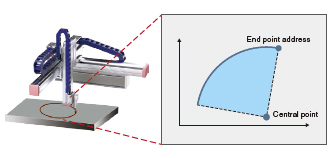
Trajectory control
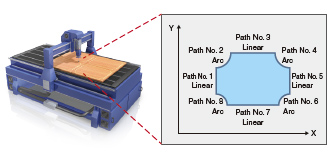
Speed-position switching
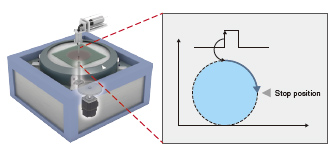
Programming
The Motion module easily executes positioning operation with the instruction in a sequence program that starts a positioning data of the motion profile table. To meet various application needs, the Motion module offers various types of control, such as linear/two-axis circular interpolation, fixed-pitch feed, and trajectory control.
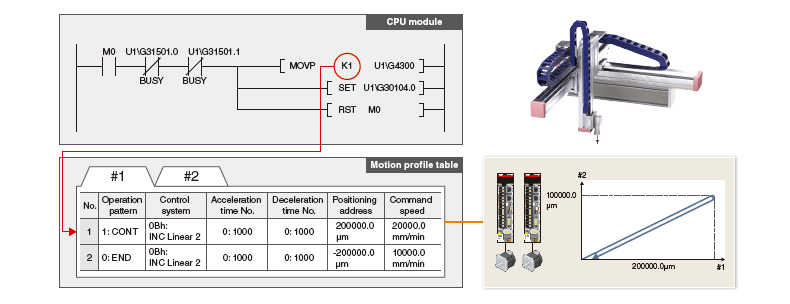
Advanced synchronous control
Synchronous control can be achieved using software instead of controlling mechanically with gear, shaft, clutch, speed change gear or cam, etc.
- Synchronous control can be flexibly started/ended for each axis, enabling the synchronous control axis and positioning control axis to be used within the same program.
- Command generation axis, servo input axis, or synchronous encoder*1 axis can be set as the input axis.
- The output axis is operated with a cam. The following three operations can be performed with the cam functions: linear operation, two-way operation, and feed operation.
- An incremental synchronous encoder*2 can be connected via MR-J5-G(-RJ)/MR-J5W2-G servo amplifier.
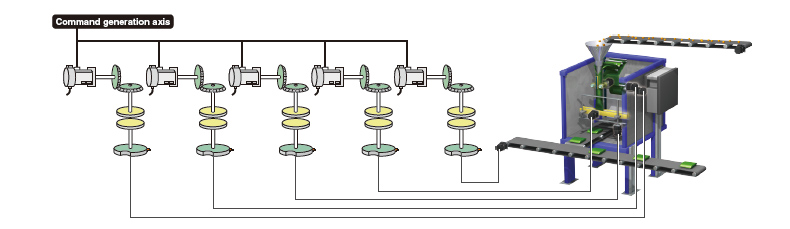
- *1.Supported by MELSERVO-J5 series.
- *2.When configuring an absolute position system, use an encoder of HK series servo motors.
- [Command generation axis]
- Command generation axis is the axis that performs only the command generation. It is controlled independently of other axes connected to servo amplifiers. (not counted as a control axis)
Parameter Settings
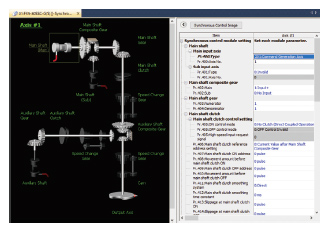
Synchronous control is executed by setting parameters of the input axis, output axis, gear, and clutch for synchronous control and turning on the synchronous control start signal.
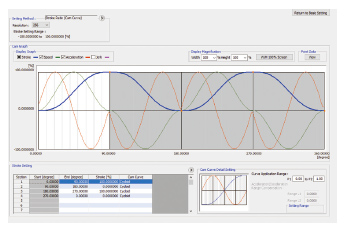
The cam graph can be flexibly and easily created through drag & drop. The waveform is changed according to the pointer’s movement.
Start/Stop
Synchronous control can be executed after synchronous parameters are set for each output axis. When synchronous control start signal is turned on, the synchronous control parameters are analyzed, and the status is changed to during synchronous control.
The output axis is operated by the commands transmitted from the input axis.
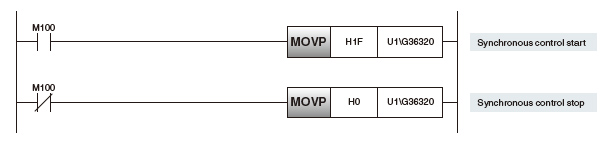
Speed-Torque Control
Speed Control/Torque Control
The axes in speed control are controlled to run at the constant speed following the speed command, and the axes in torque control are at the constant torque following the torque command.
The Motion module can be used for tension control application, such as unwinding or rewinding.
In addition, the current positions are always tracked even in speed and torque control, and therefore positioning is executed smoothly in accordance with the absolute position coordinate in position control after switched from the speed and torque control.
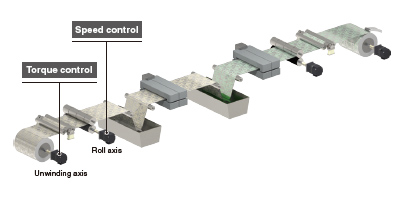
Continuous Operation to Torque Control
When using this control, you can switch from position control to torque control continuously without stopping the servo motor.
- The current positions are always tracked even in torque control, and therefore positioning is executed smoothly in position control after switched from the torque control.
- Position control is smoothly switched to torque control without stopping the servo motor.

Auxiliary Features
Virtual Servo Amplifier
The virtual servo amplifier function enables operations of a virtual servo amplifier as if an actual unit is connected.
When the virtual servo amplifier is set as a servo input axis of synchronous control, the Motion module executes synchronous control with virtually generated input commands.
In addition, this function is used to simulate an axis without an actual connection.
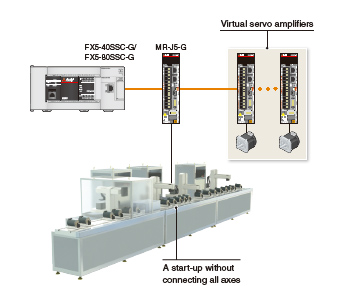
Automatic Return
When remote stations are back to normal status after disconnected due to a data link error, this function automatically returns the disconnected stations to the network and restarts data link.
When defective components need to be replaced in one of the machines in a production line or one of the units in a machine, only the machine or the unit can be partly turned off without powering off the whole system.
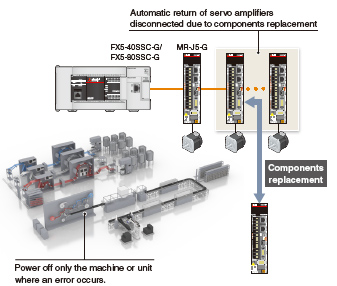
Batteryless Operation
The Motion module and the servo amplifier can be operated without a battery.*1
Maintenance costs are reduced as a result of eliminating the battery replacement and stock control.
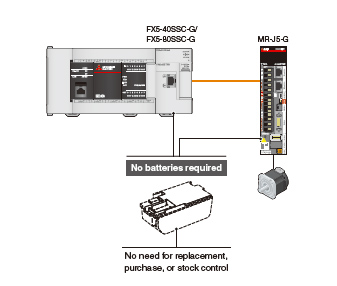
- *1.Direct drive motors may require a battery.
Mark Detection
This function latches data responding to a trigger signal input to a servo amplifier.
The compensation amount is calculated based on the latched data, and the error is compensated using a compensation axis.
A high-accuracy mark detection at 1 μs is available. Upgraded
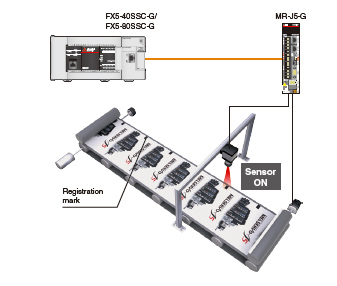
Engineering Environment
MELSOFT GX Works3
MELSOFT GX Works3 has a variety of features which help users create projects and conduct maintenance more flexibly and easily.
Our variety of engineering software (GX Works3, drive system sizing software, and FA Integrated Selection Tool, etc.) fully covers all stages of development processes from parameter settings to maintenance of Motion module, servo amplifier, and servo motors.
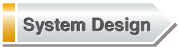
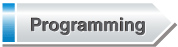
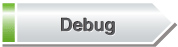
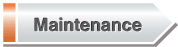
System Design
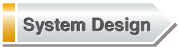
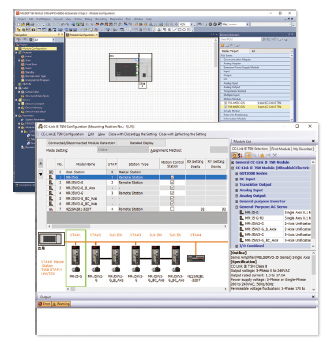
- Module configuration
- Network configuration
- Data settings for servo amplifiers
- Settings for remote I/O
Programming (Positioning)
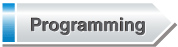
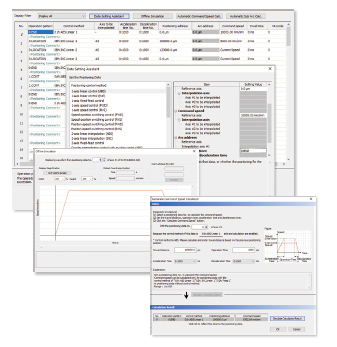
- Programming with Ladder, SFC, FBD/LD
- Positioning data settings
- Offline simulation, automatic calculation of command speed
Programming (Synchronous Control)
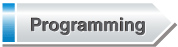
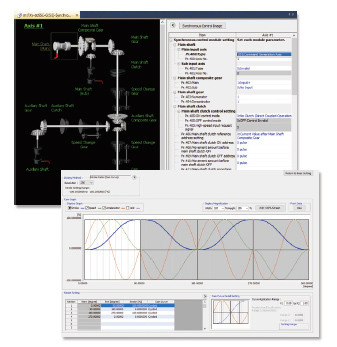
- Synchronous control parameter
- Cam data creation, cam data list
Debug/Maintenance
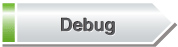
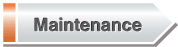

- Event history
- Current value history, start history, axis monitor
- Servo monitor
- Digital oscilloscope
Open integrated networking across the manufacturing enterprise
CC-Link IE TSN supports TCP/IP communications and applies it to industrial architectures through its support of TSN enabling real-time communications.
With its flexible system architecture and extensive setup and troubleshooting features make CC-Link IE TSN ideal for building an IIoT infrastructure across the manufacturing enterprise.
- * TSN: Time Sensitive Networking
- * IIoT: Industrial Internet of Things
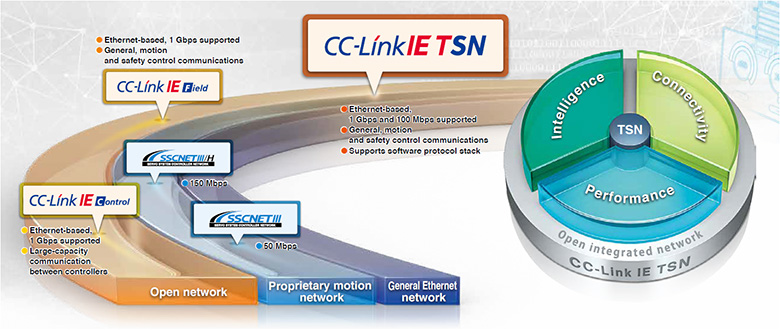
Servo Amplifier MELSERVO-J5/MELSERVO-JET
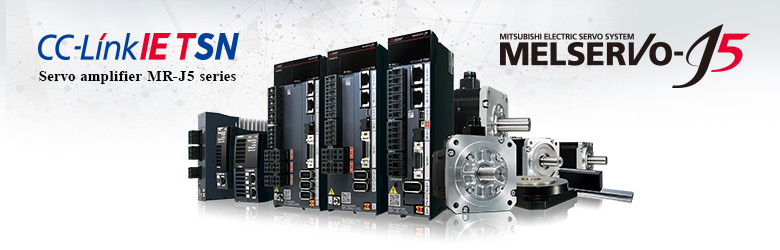
The MELSERVO-J5 series high-performance, industry-leading servo amplifiers feature a unique control engine that is more powerful than ever before.
These servo amplifiers can connect to CC-Link IE TSN to perform high-speed, high-precision control.
MR-J5W-G/MR-J5W-B multi-axis servo amplifiers and MR-J5D-G4 drive units simplify wiring and enable a compact machine.
- *1.MR-J5-G/MR-J5D1-G4 support 31.25 μs.
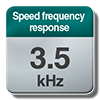
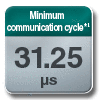

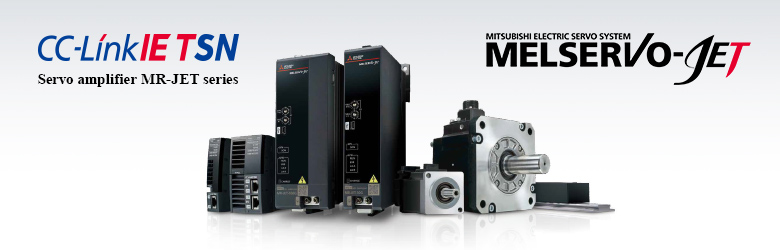
The MELSERVO-JET series high-performance servo amplifiers feature a unique control engine that is more powerful than ever before.
These servo amplifiers can connect to CC-Link IE TSN to perform high-speed, high-precision control.
The servo amplifiers support linear servo motors in addition to the rotary motors.
EtherCAT® is supported by MR-JET-G-N1.
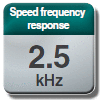
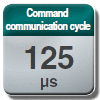
Functions List
Motion Module | |||
---|---|---|---|
FX5-40SSC-G | FX5-80SSC-G | ||
Maximum number of control axes | 4 axes | 8 axes | |
Operation cycle (operation cycle setting) [μs] |
500, 1000, 2000, 4000 | ||
Servo amplifier connection method | CC-Link IE TSN (communication speed: 1 Gbps/100 Mbps) | ||
Compatible servo amplifiers | MR-J5-G, MR-J5W-G, MR-J5D-G4 More details
MR-JET-G More details |
||
Interpolation function | Linear interpolation (up to 4 axes), 2-axis circular interpolation | ||
Control method | Positioning control, trajectory control (linear and arc), speed control, speed-torque control,
synchronous control, continuous operation to torque control |
||
Acceleration/deceleration processing |
Trapezoidal acceleration/deceleration, S-curve acceleration/deceleration | ||
Compensation function | Backlash compensation, electronic gear, near pass function | ||
Synchronous control | Synchronous encoder input, command generation axis, cam, phase compensation | ||
Cam control | Number of cam registrations *1 |
Up to 128 | |
Cam data | Stroke ratio data format, coordinate data format | ||
Cam auto- generation |
Cam auto-generation for rotary knife | ||
Positioning control method | Motion profile table | ||
Control unit | mm, inch, degree, pulse | ||
Number of positioning data | 600 data (positioning data No. 1 to 600)/axis (Can be set with MELSOFT GX Works3 or a sequence program.) |
||
Backup | Parameters, positioning data, and block start data can be saved on flash ROM (batteryless backup) | ||
Home position return | Driver home position return *2 | ||
Positioning control | Linear interpolation control (Up to 4 axes
*3 (vector speed, reference axis speed)),
fixed-pitch feed control (up to 4 axes), 2-axis circular interpolation (auxiliary point-specified, central point-specified), speed control (up to 4 axes), speed-position switching control (INC mode, ABS mode), position-speed switching control (INC mode), current value change (positioning data, start No. for a current value changing) NOP instruction, JUMP instruction, LOOP, LEND, block start, condition start, wait start, simultaneous start, repeated start |
||
Manual control | JOG operation, inching operation, manual pulse generator operation (up to 1 module (incremental), unit magnification (1 to 10000 times), via CPU (buffer memory)) |
||
Speed-torque control | Speed control not including position loop, torque control, continuous operation to torque control | ||
Absolute position system | Provided | ||
Synchronous encoder operation function | Up to 4 modules (via a servo amplifier or a CPU) | ||
Speed limit | Speed limit value, JOG speed limit value | ||
Torque limit function | Torque limit value same setting, torque limit value individual setting | ||
Forced stop | Via buffer memory, valid/invalid setting | ||
Software stroke limit function | Movable range check with feed current value or with machine feed value | ||
Hardware stroke limit function | Provided | ||
Speed change | Provided | ||
Override | 0 to 300 [%] | ||
Acceleration/deceleration process change | Acceleration/deceleration time | ||
Torque limit change | Provided | ||
Target position change | Speed to a target position address and a target position is changeable. | ||
M-code output function | Provided | ||
Other functions |
Step function | Deceleration unit step, data No. unit step | |
Skip function | Via CPU, via external command signal | ||
Parameter initialization function | Provided | ||
External input signal select function | Via CPU, via servo amplifier | ||
Mark detection function | Continuous detection mode, specified number of detections mode, ring buffer mode | ||
Mark detection signal | Up to the number of axes of the connected servo amplifiers | ||
Mark detection setting | 16 settings | ||
Optional data monitor function | Up to 4 points/axis | ||
Functional safety | DI/O connection of the servo amplifier *4 | ||
Automatic return | Provided | ||
Digital oscilloscope function | Bit data: 16 channels, word data: 16 channels *5 |
- *1.The number of cam registrations depends on the memory capacity, cam resolution, and number of coordinates.
- *2.The home position return method set in a driver (a servo amplifier) is used.
- *3.4-axis linear interpolation control is enabled only at the reference axis speed.
- *4.The safety extension module can be combined with a Motion module with version 1.001 or later.
- *5.Eight channels of each word data and bit data can be displayed in real time.