Controllers MELSEC iQ-R Series Product features -System Recorder-
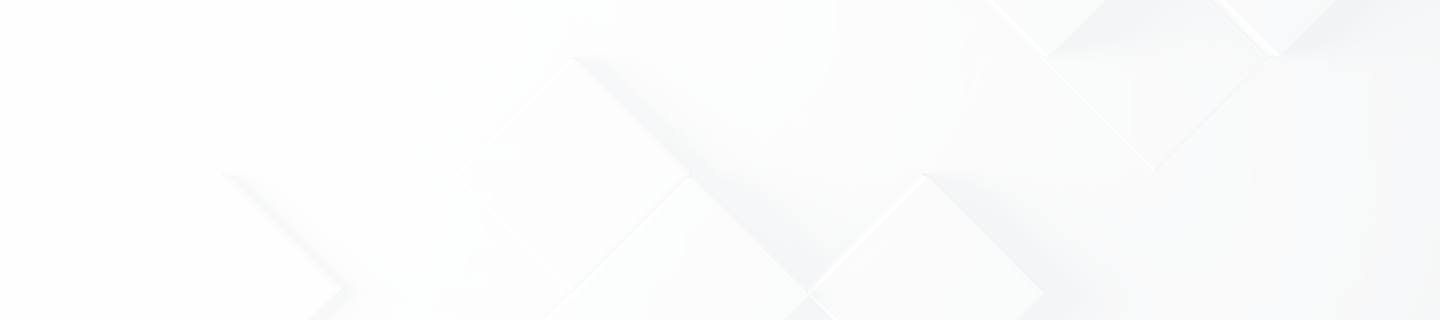
Simplified analysis
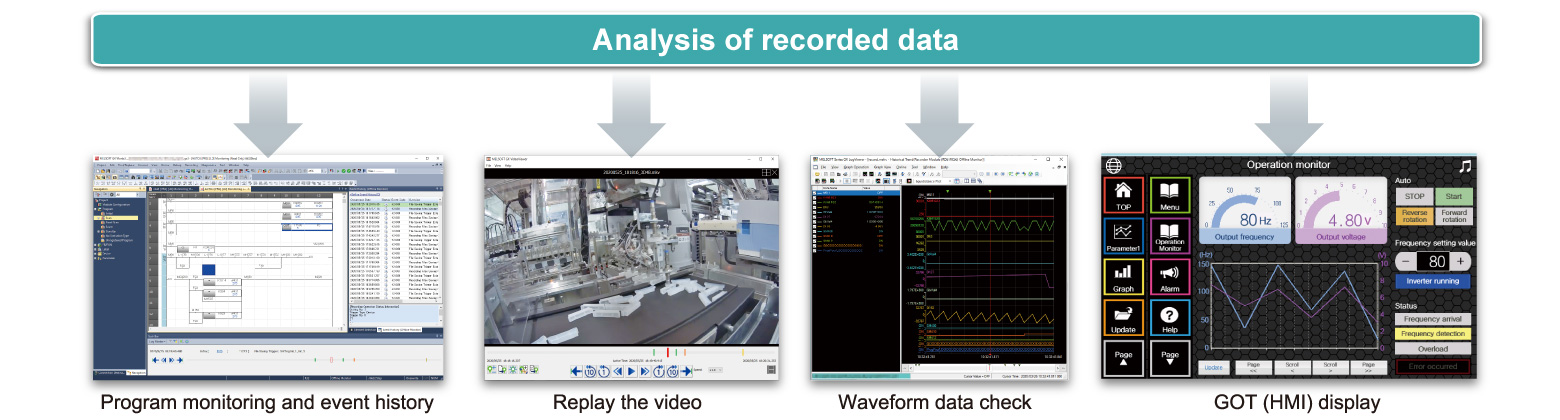
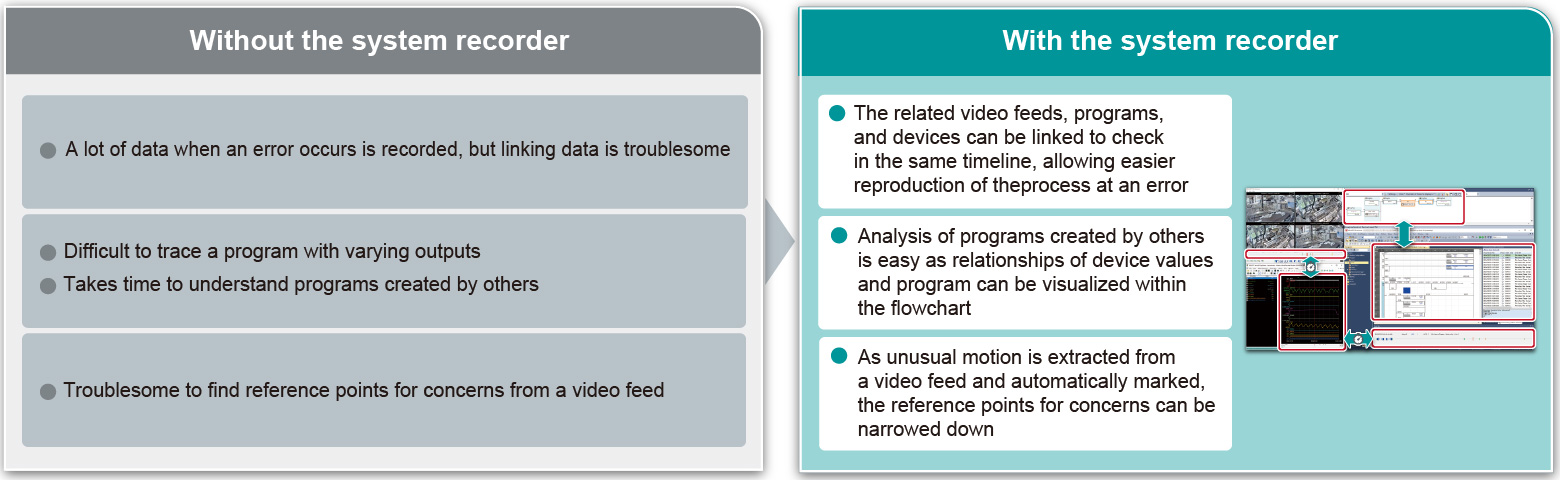
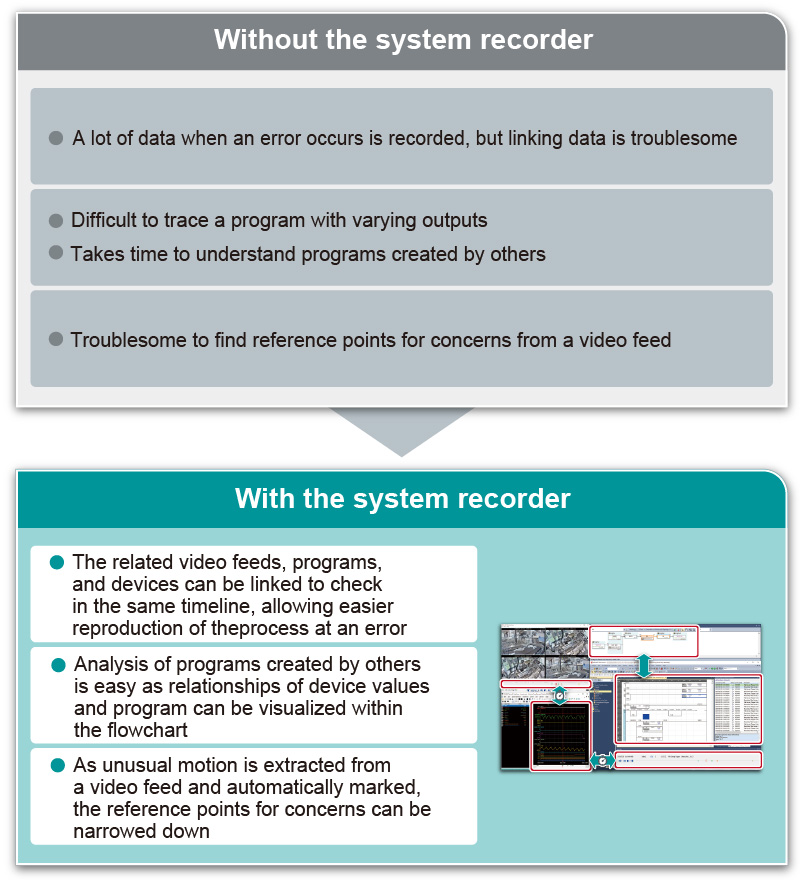
Log marker function GX VideoViewer ProGX VideoViewerGX LogViewerGX Works3
Faster cause analysis by synchronized video feed, program and waveform monitoring
- ❶Register milestone points on the timeline
Milestone points (log marker) can be added to the moment when an error occurs. These points can be saved for later use or for distributing amongst other support personnel enabling multiple people even in the remote location to analyze the problem area of the application.
- ❷Categorize registered milestone points
Log markers can be color-coded according to importance and event type with support of commenting, realizing efficient analysis.
- ❸Confirming video feed with collected data
After checking the video feed, outputs causing an error and related devices can be tracked as well as programs that change devices. The milestone points (log markers) are synchronized with each software and reproduced at different playback speeds offering a realistic view of the process together with the control data collected.
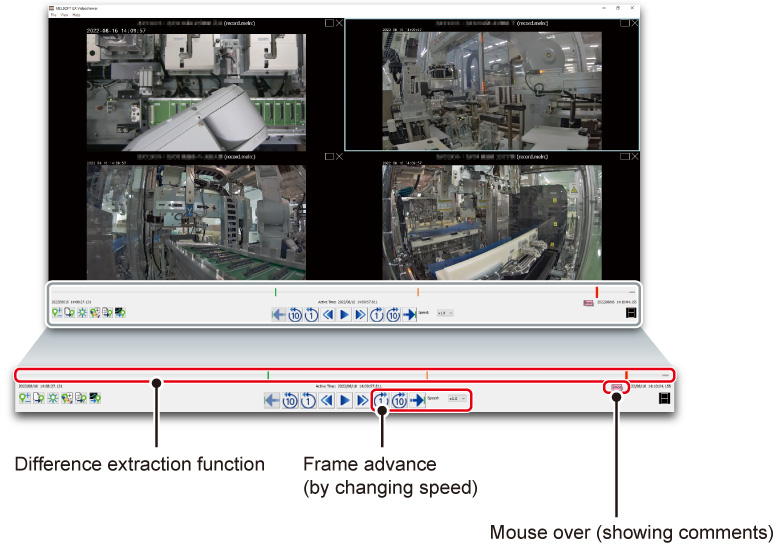
Difference extraction function GX VideoViewer Pro
Industry's
first*1
AI technology that extracts differences from the target video by comparing “appearance” and “operation” without deep learning
In addition to the GX VideoViewer functions, differences in a video feed are extracted and marked just with simple setting.
- *1.Based on Mitsubishi Electric research as of April 28, 2022
- ❶Automatically mark differences in the recorded video feed
- Extracts differences in the video feed that differ from normal patterns and adds a mark in the video feed and on the seek bar
- AI analyzes differences of appearance and operation with unique algorithm, enabling easier error analysis
- Significantly reduce the time to find errors and such occurring at a high-speed which cannot follow with the human eye
- ❷Easy 2-step setting
Automatic extraction by unique algorithms can be set up in 2 simple steps:
- STEP1Set camera images of normal operation. (generation of normal pattern)
- STEP2Execute difference extraction.
Differences are extracted according to changes in “appearance” and “operation”, then marked on the video feed automatically.
The log markers can be synchronized with other software.
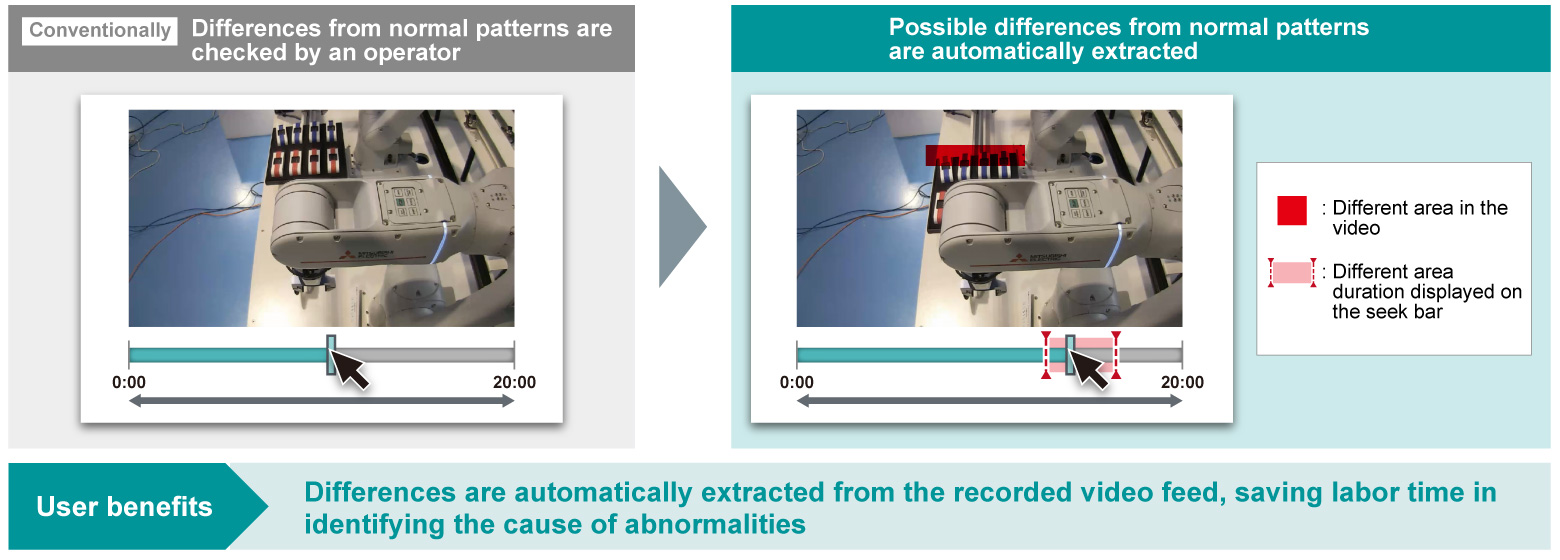

Maisart: Mitsubishi Electric's AI creates the State-of-the-ART in technology
Mitsubishi Electric's brand of AI technology aiming to make all devices smarter
Offline monitoring GX LogViewerGX Works3GT Designer3
Synchronized playback of program, waveform data, GOT (HMI)
(screens, operation logs, alarm history)
- Playback of data can be done very simply just by loading the recorded data into GX Works3, automatically executing all other necessary tools
- Using the “seek bar” enables to jump back and forth within the timeline synchronizing data between GX Works3 program monitoring (circuit monitor), GX LogViewer (waveform display), and GOT (HMI) (screens, operation logs, alarm history)
- Programming languages such as ladder, ST, FBD, and SFC are supported
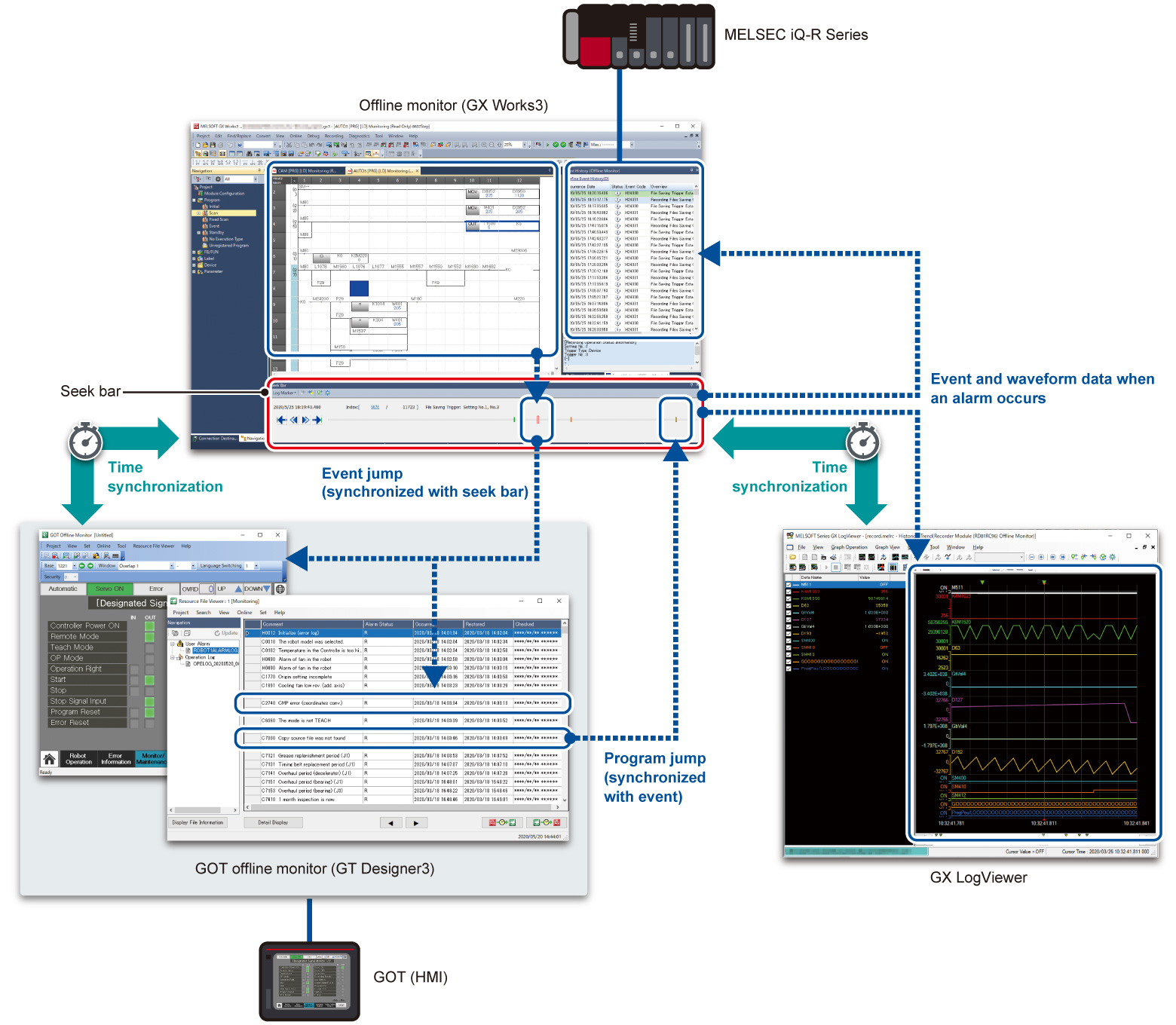
Data flow analysis function GX Works3
- ❶Visualize affected area of device/label
Device and labels together with the affected area can be visualized within the flowchart. The process flow from comments, instruction names, event history, and monitored values can be checked easily identifying the cause of an error.
- ❷Bookmark milestone points
Bookmark milestone points to check speedy.
- ❸Main program languages supported
Analysis can be done for ladder programs, function block diagram (FBD), SFC (within Zoom) and ST language programs.
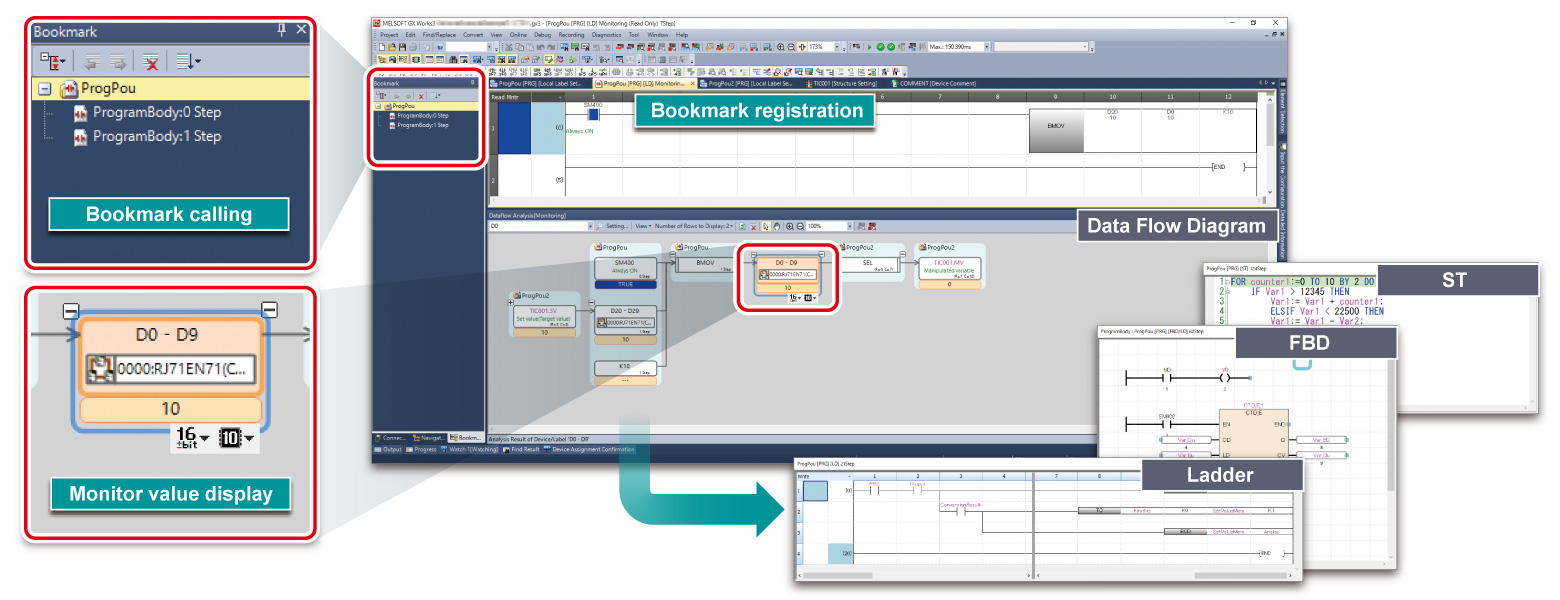
Simplified analysis of motion control GX LogViewer
By loading the motion module/motion CPU module data to GX LogViewer, the axis data shown as a waveform can be easily compared with the programmable controller device data for analysis.
Simplified analysis using panel computer GX Works3GX LogViewerGT Designer3GX VideoViewer
Multiple data can be reproduced on a panel computer such as the MELIPC MI3000 (embedded Windows® OS). Considering the panel computer is situated on the shop floor, various historical alarms and operation logs can be confirmed efficiently at the point where a problem occurs.
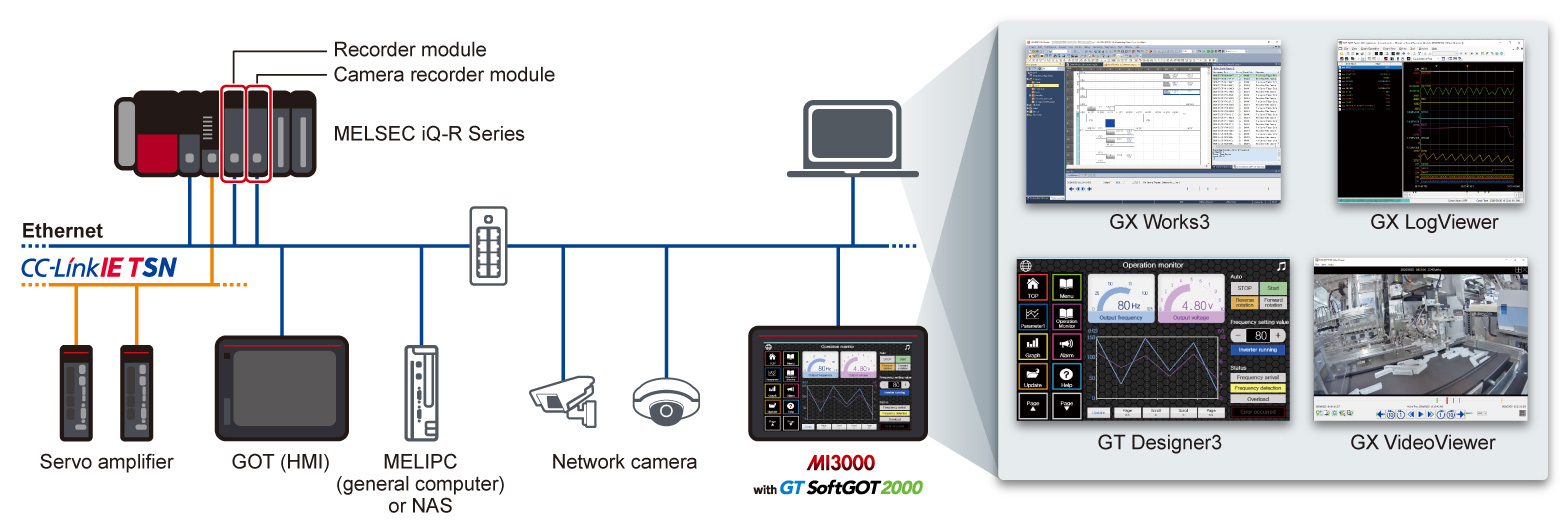