Controllers MELSEC-L Series
Product features -CPU-
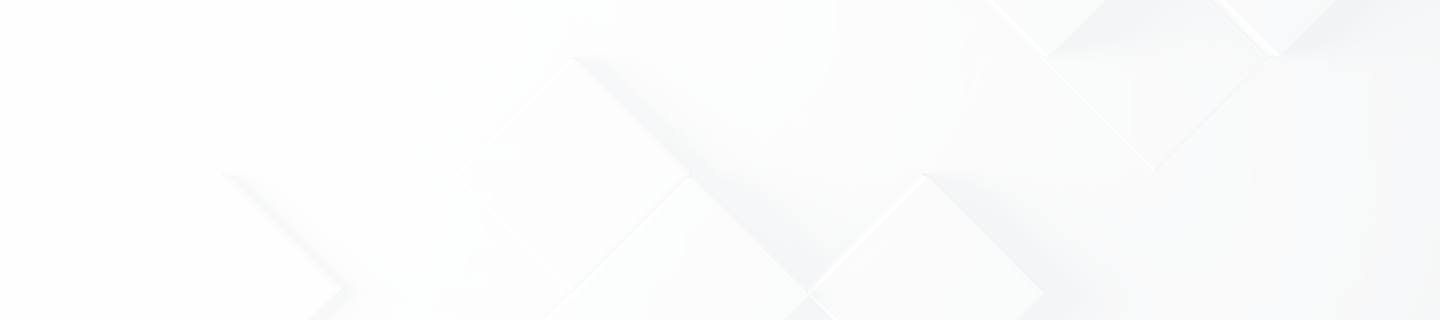
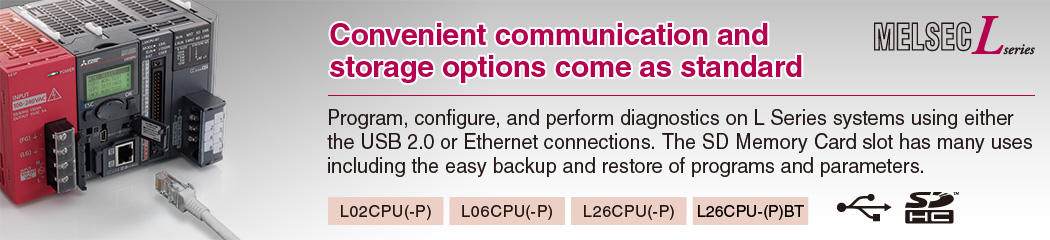
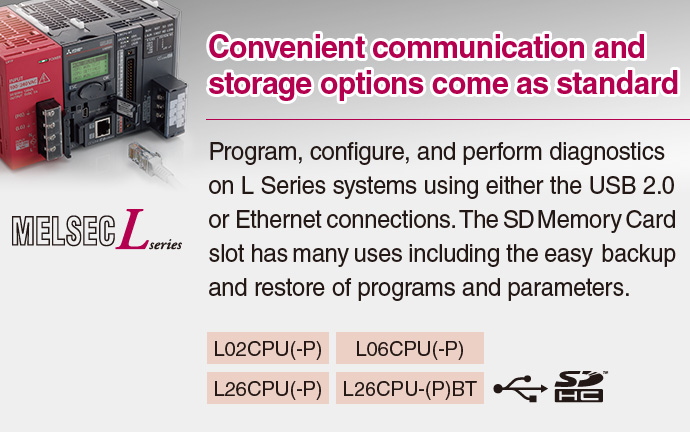
USB and Ethernet connections standard
Use the USB 2.0 interface or Ethernet to connect directly at the instillation site. The Ethernet interface supports direct connection with either a cross or straight LAN cable and does not require any configuration of the programmable controller or PC to operate.
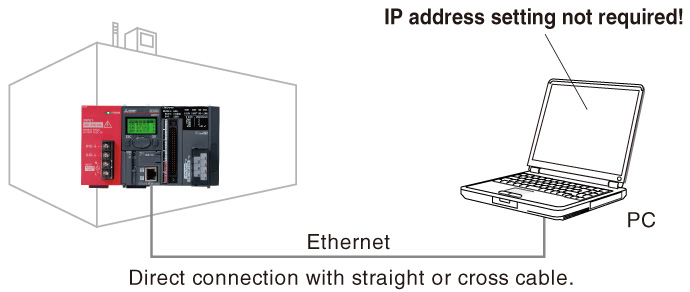
CC-Link IE Field Network Basic does not require network module<sup>Improved functionality!</sup>
Programmable controller CPUs with an embedded Ethernet port can be used as a master station*1, eliminating the need for an additional network module. The network can be configured with a minimum number of modules reducing space and hardware cost.
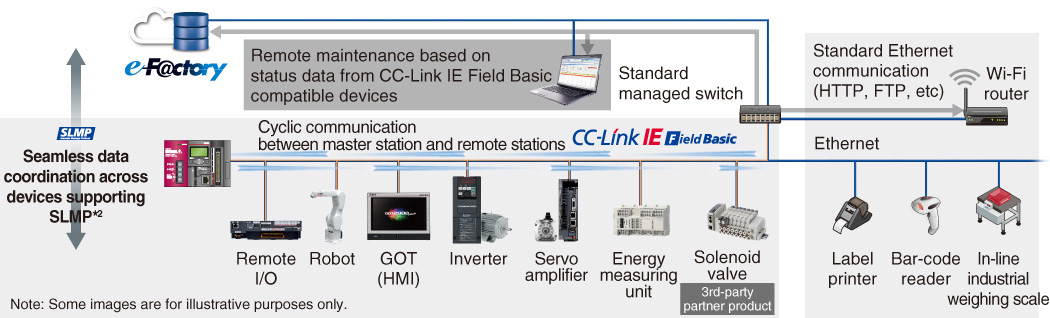
- *1.Only LnCPU(-P/-BT/-PBT) are compatible.
- *2.SLMP: Seamless Message Protocol
<span>Easily connect to BACnet<sup class="vis">®</sup> and MODBUS<sup class="vis">®</sup>/TCP<sup>Improved functionality!</sup></span>
Ethernet realizes a high-speed connection, such as communication with external devices.
By using the predefined protocol support function, various devices that require open network protocol support, such as BACnet® and MODBUS®/TCP are supported.
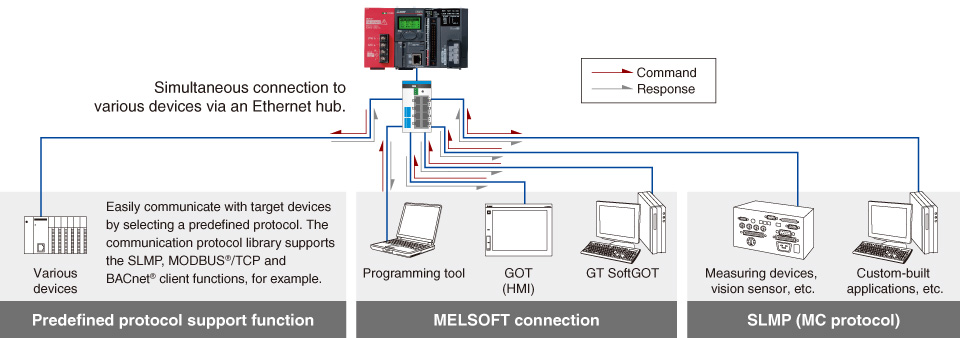
Network timestamp
Synchronize systems on an Ethernet network using an SNTP*3 server. Time synchronization can be achieved to enable simultaneous operations, quality control, or error tracking.
- *3.SNTP: Simple Network Time Protocol
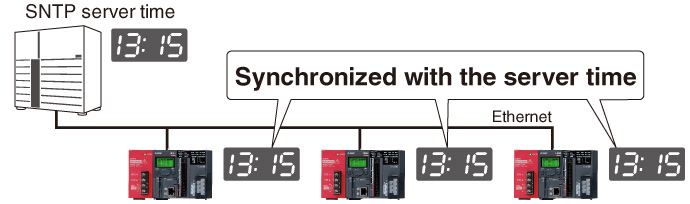
Program-less device data transfer
Simple PLC communication function*4
Using the programming tool, a simple parameter setting is all that is needed to transfer device data such as production information with no programming required.
This function makes it possible to easily establish communications not only with L Series, but also MELSEC iQ-R Series, iQ-F Series, Q Series and QnA/A Series controllers.
- *4.CPU module whose first five serial number digits are “13042” or later is required.
■Simple PLC Communication Setting
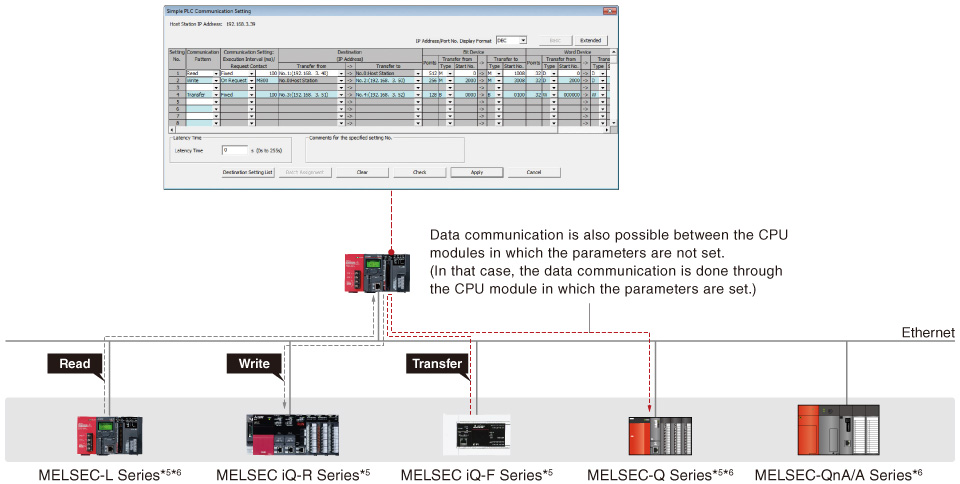
- *5.Built-in Ethernet port CPU is supported.
- *6.CPU module and Ethernet interface module are supported.
SD memory card special features
Use the SD/SDHC compatible memory card to quickly and easily back-up the CPU programs and parameters.
The backups can then be just as easily restored or used to program other CPUs. The memory card can also be used to hold data captured with the data logging function*7.
- *7.For details about the data logging function, please refer to “Historical trend and live feeds of production”.
Save/load programs directly into the Programmable Controller
Multiple project save/load function*8
Parameters, program files, etc., can be saved/read onto an SD memory card by simply using the onboard display unit, without having to connect to a separate PC. Once saved on the SD memory card, files can be sent via e-mail, for example, when requiring off-site editing of the files.
- *8.Supported by CPU module whose first five serial number digits are “14042” or later.
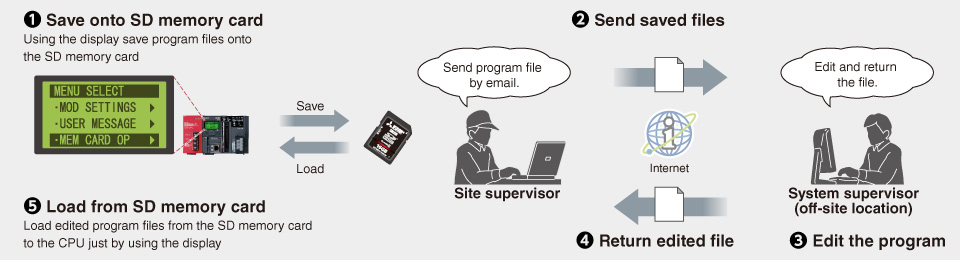