Realizing small-lot, multi-cycle production using robot assembly cells
First released March 2014
Achieving high-mix low-volume production is a common challenge for every sector of the manufacturing industry. Even certain mass-produced products have a wide variance of models as well.
As an example, the Kani Factory at Mitsubishi Electric’s Nagoya Works manufactures electromagnetic switches. To coincide with the launch of its MS-T series, the factory introduced an innovative production method in which it combined flexible cellular manufacturing with industrial robots. By balancing the benefits of both, this solution has achieved the small-lot, multi-cycle manufacturing required for electromagnetic switches.
Key points of this case study
- 1. Cellular manufacturing allows flexible setup changes for variable type and volume production
- 2. Improved quality and increased operating rate by using robots
- 3. Optimized manufacturing with complete Mitsubishi Electric Factory Automation (FA) solution
Introduction to the Kani Factory – Electromagnetic switch manufacturing base
Mitsubishi Electric’s Kani Factory is part of the company’s Nagoya Works and is located in the city of Kani, Gifu Prefecture, Japan. It is a specialized factory producing electromagnetic switches used in start/stop motors and overload (burnout) protection applications. Electromagnetic switches need to be mass produced, and the factory is equipped with fully automated manufacturing lines to achieve this. A benefit of this setup is increased output when continuously producing identical products. However, tooling changeovers take time, so efficiency decreases in cases when a multitude of models need to be produced. There are various types of electromagnetic switches featuring different types of coils and more - so the factory needs a flexible production system that can switch between product types depending on the required lead time.
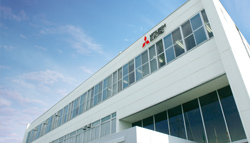
One way to achieve high-mix production with minimal setup changes would be a manual cellular manufacturing method. However, order volumes tend to be high for electromagnetic switches, particularly for low-voltage products, so there were concerns that this approach, which relies on manual work, would not ensure sufficient output. For the manufacture of electromagnetic switches, the ideal system needs to maintain a similar capacity to a fully automated line, even with repeated setup changes.
“Robot assembly cellular manufacturing system” for the MS-T series
For the new MS-T series, the factory introduced a “robot assembly cellular manufacturing system”, which combined cellular production with robots.
A key aspect of cellular manufacturing using robots is that the system combines the capabilities of both people and equipment, with robots automating processes such as the transfer and assembly of components. The production process for electromagnetic switches consists of six main stages: insertion of movable contacts, installation of fixed contacts, rear case assembly, terminal screw tightening, fitting of the terminal cover, and testing. Robots and FA equipment are used in each stage of the process.
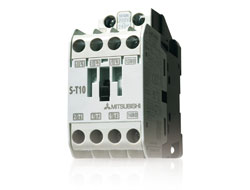
MS-T Series electromagnetic switches
Industrial robots: MELFA F Series
The system utilized the MELFA F series, the latest model of Mitsubishi Electric’s MELFA industrial robots at the time. These robots deliver enhanced performance including high speed, an expanded operating range, internal cables, plus improved intelligent technology such as compatibility with force and vision sensors.
In the robot cell, as well as performing assembly work automatically at high speed, the robots are equipped with sensors to improve accuracy. For example, in the movable contact insertion process, vision sensors are used to detect misalignment. During rear case assembly, a force sensor on the robot hand measures the load to detect any abnormal fitting. When tightening terminal screws, a torque sensor is used. Fasteners are unscrewed and retightened if any sign of abnormality is found. Previously, when components were supplied by the parts feeder, there were frequent stoppages due to jamming at the outlet. In the new system, a vision sensor detects the position and angle of each component so the robot can pick it up correctly.
Robots were already in use at the Kani Factory, but as Yukihiro Kimura of the Machine Technology Section explains: “The F series features internal cables all the way to the robot arm, which prevents cable twisting, lowers the risk of disconnection, and reduces maintenance work.” Another advantage of the internal cabling is that it minimizes interference with nearby equipment.
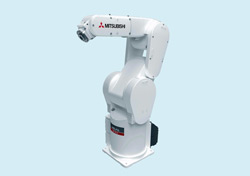
MELFA F Series industrial robots used in the assembly cell
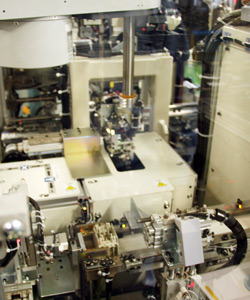
Movable contact insertion process. Insertion failures are detected by a sensor at the end of the robot arm
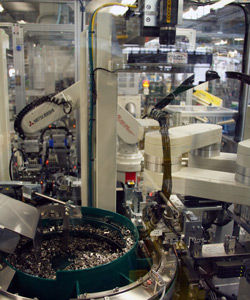
In the fixed contact insertion process, a vision sensor detects the position and angle of the component and adjusts the position of the robot
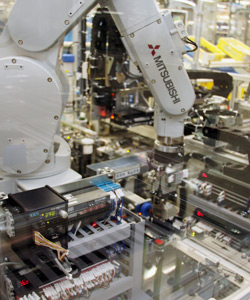
During rear case assembly, abnormal fitting is detected by the load applied to the force sensor at the end of the robot arm
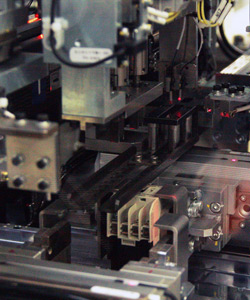
When tightening terminal screws, the servo system detects the load on the screw with a torque sensor. If any abnormality is detected, the fastener is unscrewed and retightened
Productivity improvement for any lot size
One of the main benefits of combining robots with cellular manufacturing has been an improvement in on-time delivery rates. “It now takes hardly any time or work to change the tooling setup, which has made small lot production easier, allowing flexible manufacturing with optimized lead times,” says Masahiro Ichihara, Head of Manufacturing at the Kani Factory. When it comes to electromagnetic switches, customers demand short lead times. On a fully automated line, setup changes involve a lot of work, so products are usually manufactured in units of a certain quantity. The cellular system has significantly reduced this workload, meaning that small-lot production is now possible. The automated robotic assembly process ensures production efficiency - often a weak point of cellular manufacturing.
Another major benefit is the response to minor equipment stoppages. Previously, with the fully automatic line, maintenance engineers would have to go on-site during stoppages to check the robots using a teaching box and to carry out recovery procedures. Now, with the robot assembly cell, this can be done using on-site GOT HMIs. Consequently, it takes less time and work to restart production, leading to further improvements in manufacturing efficiency.
It also has the effect of reducing the floorspace required. On a fully automated line, which are usually long, component stockers take up a lot of room. The robot assembly cell consolidates all equipment into a smaller area, taking up only 1/3 of the space, improving production efficiency per area.
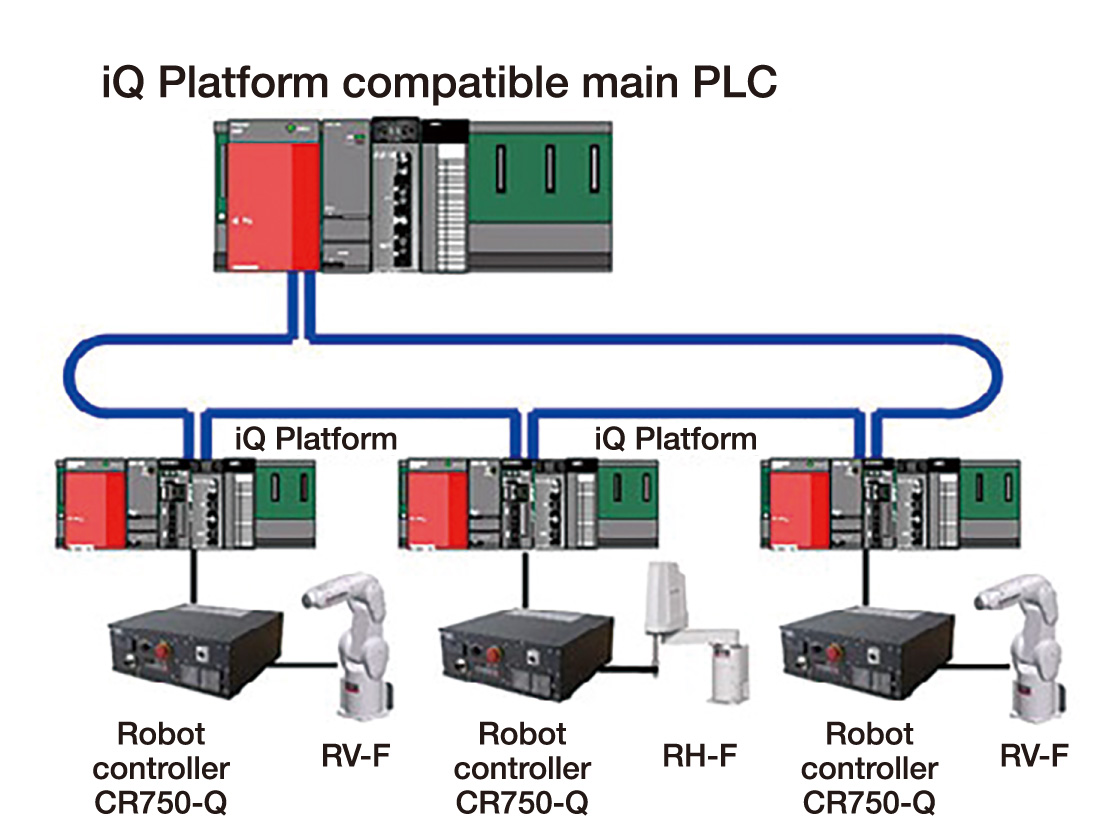
System outline
iQ Platform and e-F@ctory make system architecture easy
The robot assembly cell at the Kani Factory has introduced an e-F@ctory solution, so when a worker scans the 2D barcode printed on the production instructions, information is sent to the PLC that controls the respective process. Tooling changes to prepare for the next product type are carried out instantaneously. The MES interface means that manufacturing and quality information are communicated to the management server in real time via the integrated controller. This ensures that in the unlikely event of a problem being found in a robot or equipment, any potentially affected products can be easily identified.
The whole production facility, including robots, runs on the Mitsubishi Electric iQ Platform. “In addition to robots, the assembly cell uses a large number of devices including PLCs, servos, GOT HMIs, vision sensors and force sensors. These all operate on the iQ Platform which allows for easy batch setting and management of data. This also made the system architecture easy,” says Kimura.
By introducing these solutions, the new production system for electromagnetic switches has succeeded in achieving small-lot, multi-cycle production. As a provider of FA solutions, Mitsubishi Electric is constantly working to develop and enhance its automation technologies by putting the systems and equipment into practice at its own facilities.
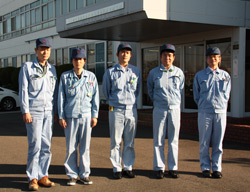
The team responsible for introducing the robot assembly cell