Improving quality and eliminating human errors
Mitsubishi Electric operates the e-F@ctory solution at its own production facilities, including the Nagoya Works. This has allowed the organization to confirm real-world improvements in productivity and operating rates, helping to continuously improve the e-F@ctory concept.
As part of this, Mitsubishi Electric is advocating the construction of optimal production systems, which leverage its factory automation products to process data and link with management systems. At the same time, the company is introducing joint solutions with manufacturing partners.
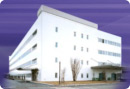
Key points of this case study
- 1. Eliminating human errors
- 2. Production efficiency improved by reducing operation time
- 3. Visualization of energy usage (power/unit consumption)
INDEX
Introduction to the Nagoya Works – FA control equipment production center
The Nagoya Works is the home of Mitsubishi Electric’s Factory Automation (FA) control equipment production center, where the company’s inverters and servo amplifiers are manufactured. Key components for various other FA products, including power modules, are also produced at this site.
Aims of introducing e-F@ctory
The e-F@ctory approach allows information to be managed and leveraged in real time, directly connecting the shop floor and IT systems to enable the visualization of the entire facility.
- Further improve quality
- Reduce lead times
- Achieve high productivity
- Visualize energy usage
Identifying issues
- Enhance coordination between each step in the process to prevent defective products from moving on to the next stage.
- Eliminate quality defects caused by human error.
- Improve production efficiency by automating the input of equipment operating parameters – a process previously done manually.
- Visualize power usage in real time, providing opportunities for energy savings.
Improvements
The system configuration, based on the MES interface, has successfully linked IT frameworks to control systems and equipment.
EcoWebServer II and EcoMonitorPro have been introduced, allowing the energy usage of each piece of equipment (power consumption/unit consumption) to be visualized.
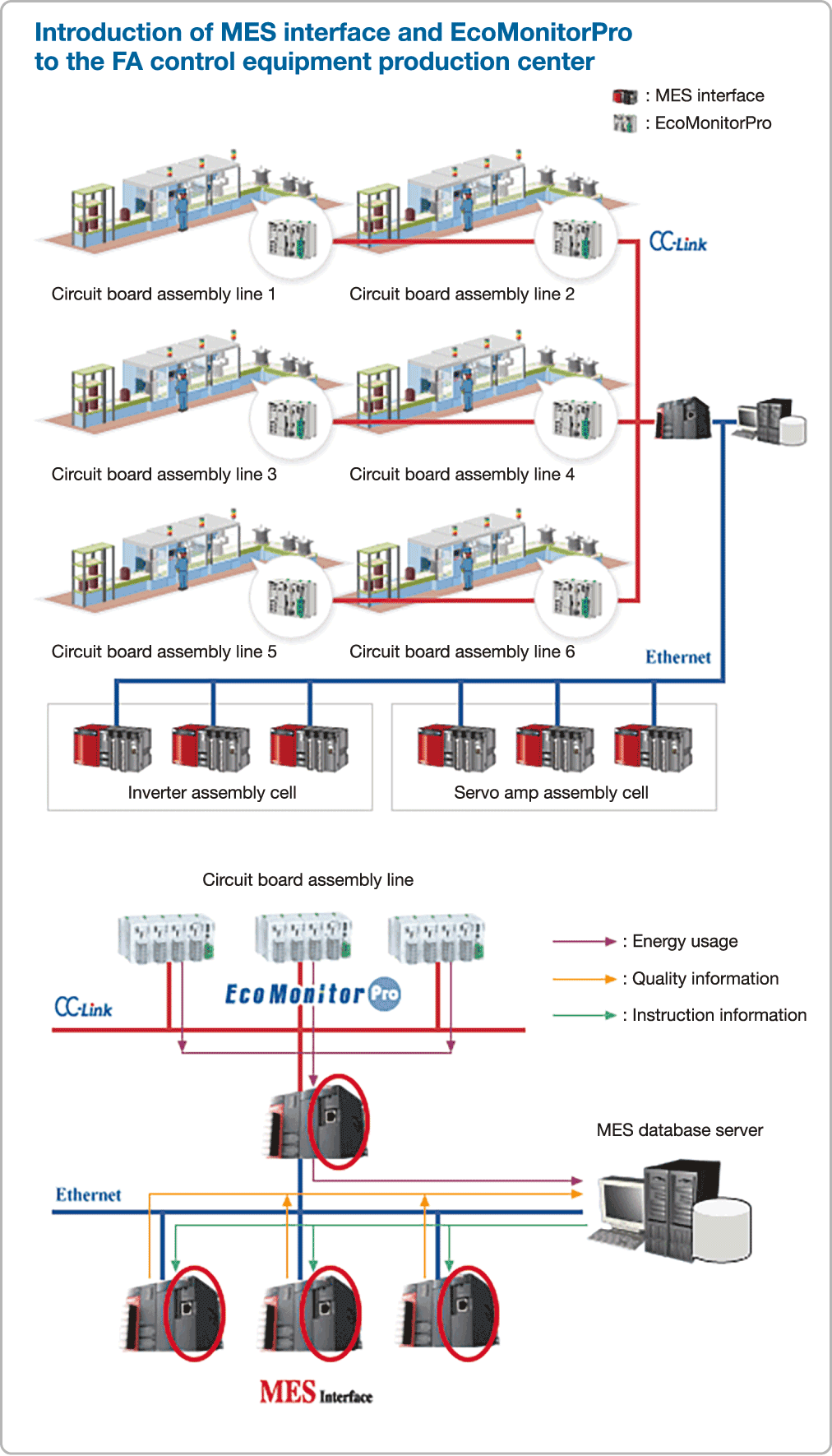
Benefits
- Human errors eliminated
- Production efficiency improved by reducing operation time
- Visualization of energy usage (power/unit consumption)
Human errors eliminated
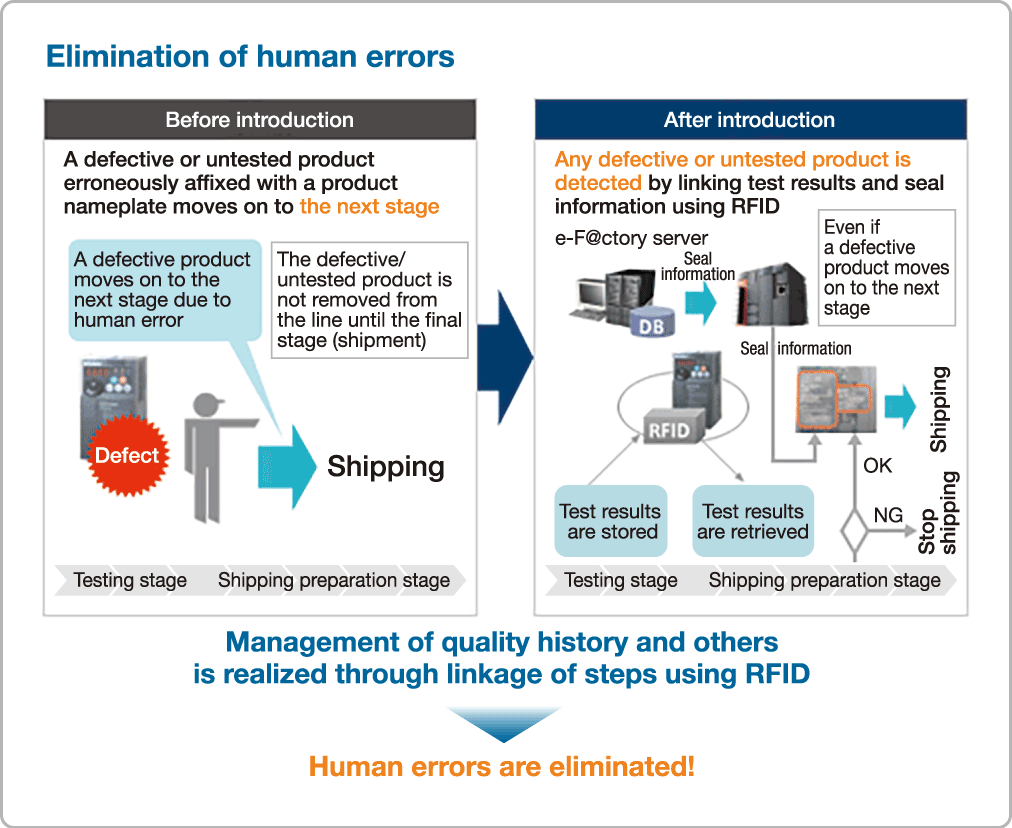
Production efficiency improved by reducing operation time
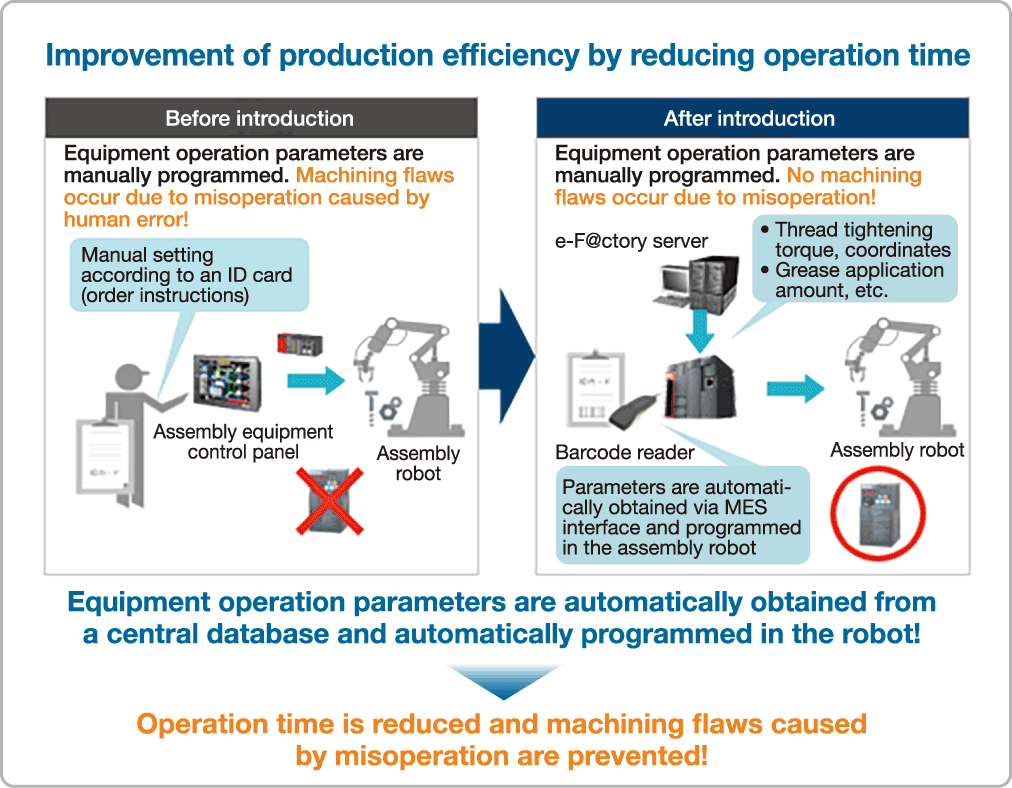
Visualisation of energy usage (power/unit consumption)
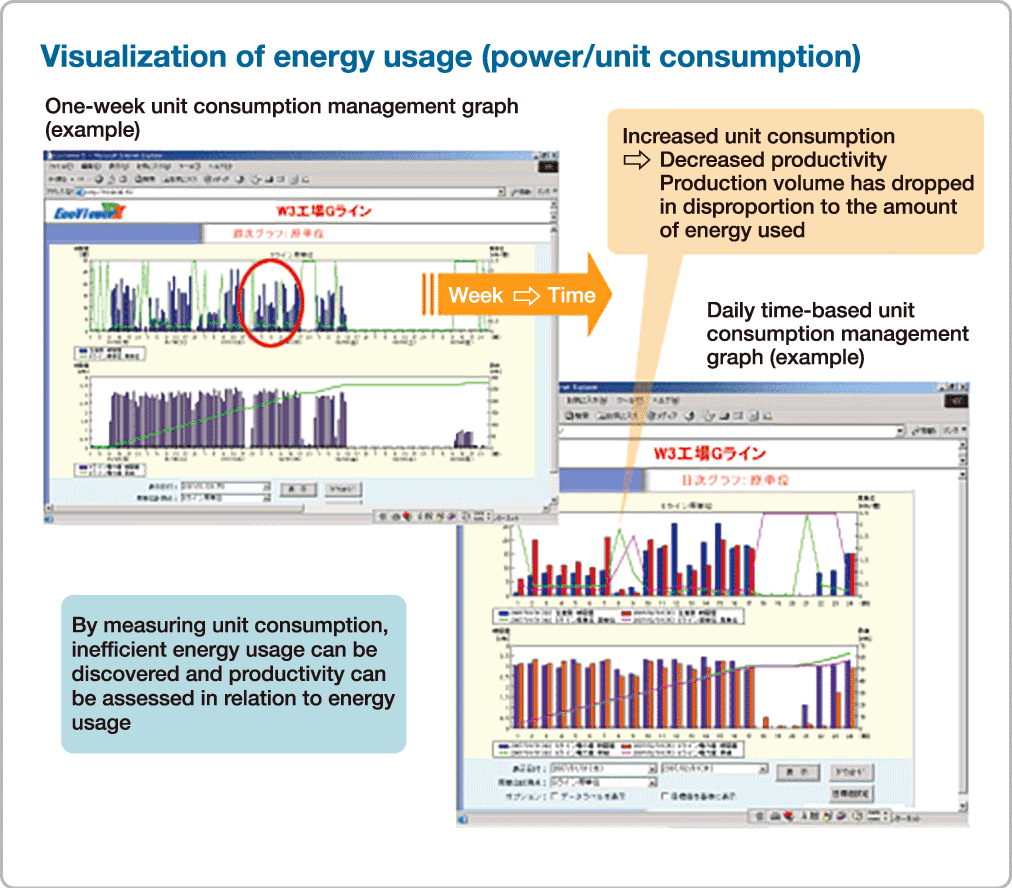