We reinforced our competitiveness.
First released March, 2022
“Mitsubishi Electric wire-cut EDMs are high speed machines, and only they can die-cut automotive materials that are thick and hard.”
Toru Watanabe, CEO, Watanabe
WATANABE CO., LTD.- Metal working, Japan -
As industrial products become more sophisticated, the precision of dies and molds has increased by orders of microns, and electrical discharge machining (EDM) technology continues to evolve to achieve this. Here, we will focus on SMEs that remain competitive by implementing EDMs to meet the changing needs of molds for automotive parts.
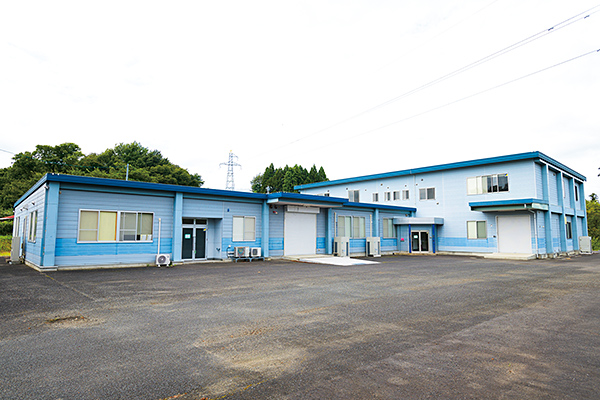
Aggressive investment in wire-cut EDMs generates improved productivity from today’s die and mold needs
Watanabe (head office: Yokohama City, Kanagawa Prefecture) has actively introduced Mitsubishi Electric wire-cut electrical discharge machines (EDMs) in its wire cutting business. It says Mitsubishi Electric wire-cut EDMs are particularly indispensable to processing automotive dies and molds and are instrumental in supporting the company’s distinct advantages of short delivery schedules and high processing precision.
Key Points:
- 1.Exhibits outstanding strengths in processing automotive dies and molds
- 2.Provides an advantage in responding to high-precision needs such as for semiconductors and 5G networks
- 3.Satisfies even the highest precision orders with the MP2400
Watanabe conducts its wire cutting business through its four plants; the Fukushima Wire Cutting Center in Nihonmatsu, Fukushima, which comprises two plants: the Kanagawa Wire Cutting Center in Zama, Kanagawa and the Chubu Wire Cutting Center in Toyokawa, Aichi. Traditionally, the company’s business focused on the automotive sector, yet from 2019, Watanabe saw an increased production in electric vehicle motors, semiconductors, 5G components, robots and pharmaceutical lines. In response to this trend, the company has augmented its fleet of wire EDMs every year, such that it now has 95 EDMs across all of its plants.
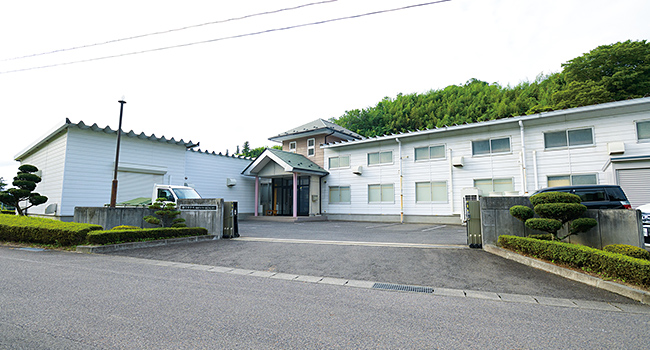
Fukushima Daiichi Plant. Eighteen employees, including many local people, work here.
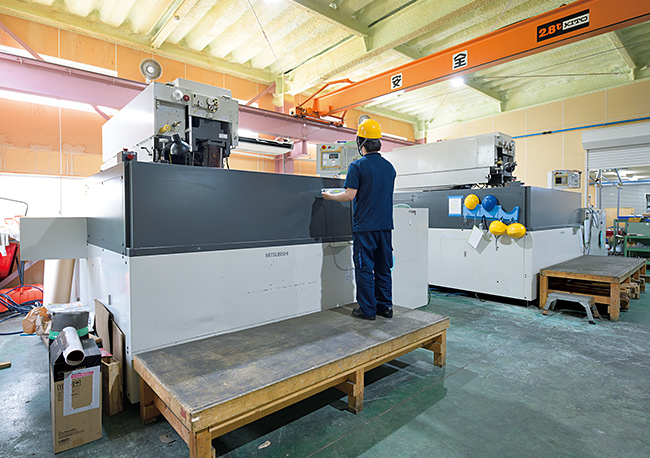
Fukushima Wire Cutting Center Daiichi Plant is outfitted with three Mitsubishi Electric large wire EDMs, including the FA40 shown in the photo above.

Toru Watanabe, CEO, Watanabe
Mitsubishi Electric’s wire EDMs account for a large proportion of the additional machines used. Toru Watanabe, CEO of Watanabe, says, “Particularly over the past five years, we have introduced Mitsubishi Electric wire EDMs in preference to other makes, to reinforce our competitiveness. Mitsubishi Electric machines are high speed, and only they can die-cut automotive materials that are thick as well as hard.”
He also notes, “Recently, we have introduced the MP2400, which is seldom seen in other companies, and has allowed us to place greater emphasis on quality.”
MP2400 at the Core of Operational Expansion
The Fukushima Wire Cutting Center Daini Plant at Nihonmatsu, Fukushima is seeking to expand the scale of its operations. As of September 2021, it has two MP2400s, eight MV2400Rs, and four MV1200R Mitsubishi Electric wire EDMs. Watanabe plans to install three additional MP2400s by spring 2022, which will bring the company-wide total of MP2400 Mitsubishi Electric wire EDMs to nine, including the MP2400s at the Kanagawa and Chubu plants, and two that are planned to be installed in the Chubu plant. “We are actively introducing the MP2400s to acquire a distinct advantage in responding to high-precision needs such as for semiconductors and 5G,” says Watanabe.
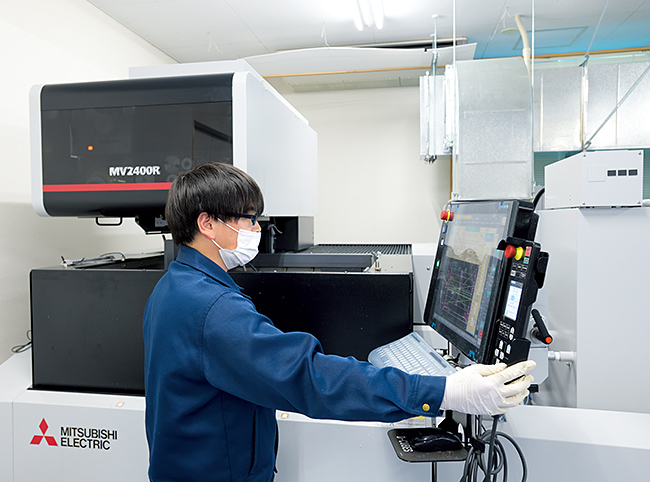
Ten employees currently work at Fukushima Wire Cutting Center Daini Plant. Most employees are completely new to operating an EDM when they first join the plant.
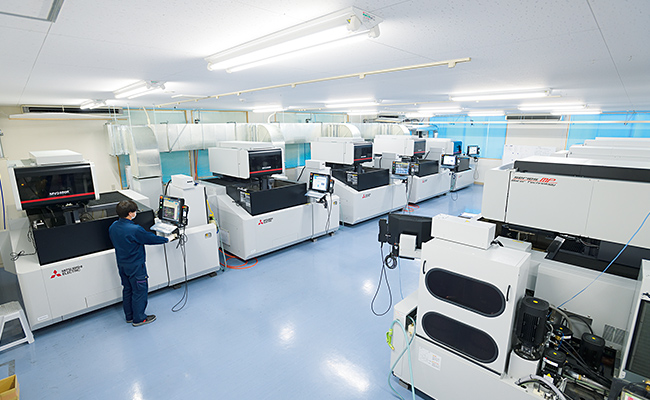
Mitsubishi Electric wire EDMs line the floor at the Fukushima Daini Plant. Room temperature is kept constant to ensure high-precision, stable operations.
Shingo Kikuchi, General Manager of the Fukushima Wire Cutting Center and Head of the Daini Plant, says the work handled by the Daiichi and Daini plants is mainly divided by processing precision. The Daiichi Plant, equipped with large cutting machines including one each of Mitsubishi Electric’s FA50, FA40 and FA30, primarily completes the cutting and trial production of component parts. The Daini Plant is dedicated to processing work that requires high precision, such as for semiconductor-related parts and dies and molds.
“When the Daini Plant commenced full-fledged operations in 2019, our production scale was still small, but we increased our number of machines in one phase over the past two years. By introducing the high-performance MP2400, we are now able to respond to high-precision processing needs, and so customer requests are also increasing,” says Kikuchi.
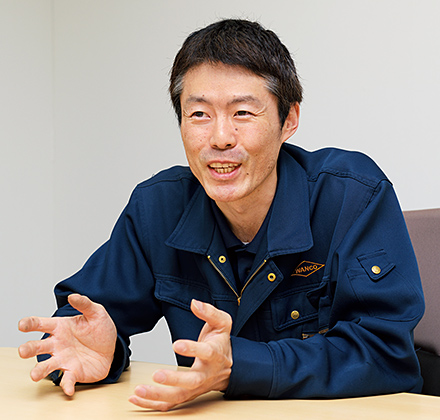
Shingo Kikuchi, Director and General Manager of the Fukushima Wire Cutting Center
As the secret behind the company’s policy of providing the shortest delivery schedules in Japan, Kikuchi says, “We manage our orders comprehensively by working out a plan from the moment we receive an order, and by taking advantage of our large number of cutting machines by allotting work to those that are idle.” In other words, although Fukushima mainly caters to orders in regions north of northern Kanto, it also allocates its work with an eye on the machine situations in Kanagawa and Chubu and flexibly takes action to achieve the shortest delivery schedules.
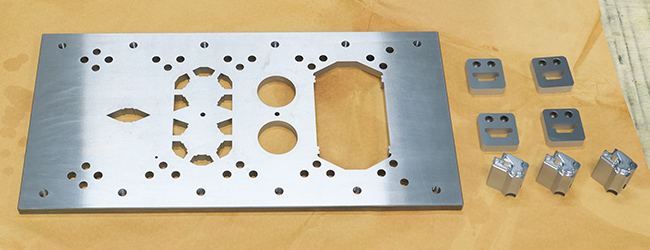
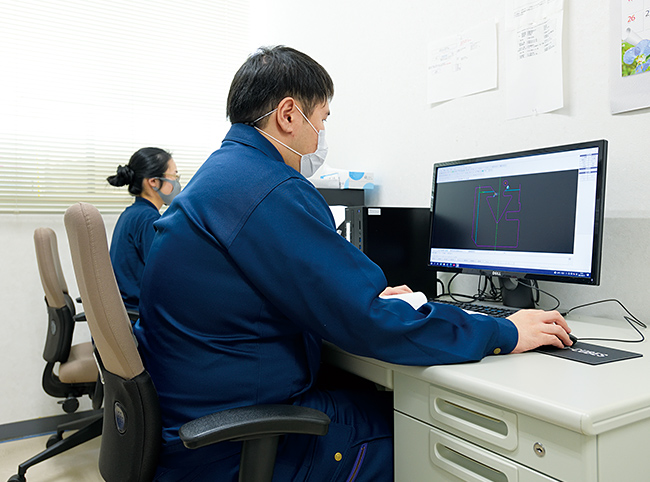
The CAD room at the Fukushima Daini Plant. There are two CAD operators in the Daiichi Plant and three in the Daini Plant.
Shohei Muto, a production supervisor, says of Mitsubishi Electric wire EDMs, “Their usability is extremely satisfying, and I also give a big score to the high precision results that are easily achieved with them and their rapid processing speed that is faster than machines by other makers.” The Daini Plant receives orders for various parts besides die components and can respond to plate thicknesses ranging from 5mm to around 200mm. “A request for 2 microns has been our greatest challenge, but we were able to overcome the challenge with the MP2400,” says Muto. He also notes that he pays particular attention to temperature management and the setting of processing materials, to ensure high-precision processing in a stable manner.
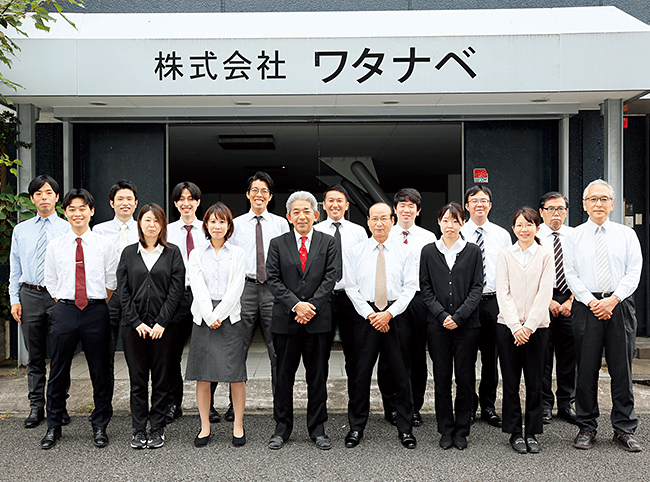
Photo: Yuji Tatsukoshi, Junko Kuroyanagi
Products and Solutions
WATANABE CO., LTD.
- •Established in 1965
•deals in wire cutting business, and sale of die products - URL : http://www.watanabe-wire.com/