We’ve achieved quicker delivery times and expanding orders
First released March, 2022
“The total running cost, including electricity, have also come down.”
Hidefumi Ikawa, CEO, Sagami Yodan
SAGAMI YODAN CO., LTD.- Metal working, Japan -
There is fierce competition in every industry. Forty years after its founding, the CEO's decision to ensure survival was automation. The effect of the decision will be clarified with the evaluation of the factory manager and engineers.
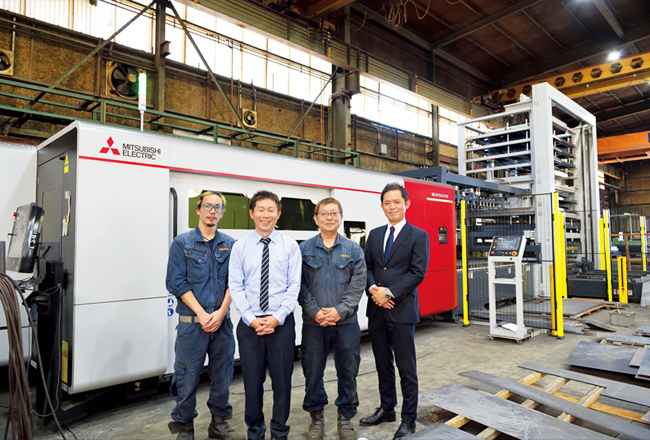
Fiber Laser Processing Machine with Automatic Sheet Changer Brings Industry Competitiveness
Sagami Yodan Co., Ltd. (located in Sagamihara City, Kanagawa Prefecture), a company whose main business is the primary processing of steel sheets, has started to use Mitsubishi Electric’s two-dimensional fiber laser processing machine to increase its already impressive delivery times. Machining thick plates and small holes has always been difficult, but now the company can not only complete these tasks at high-speed, but it has also further improved performance with a new automated sheet change system.
Key Points:
- 1.Broader capabilities for machine processing including thick plate and small hole processing
- 2.Cutting errors prevented with function to change settings automatically
- 3.Enhanced automation with new sheet change system
Since its founding in 1981, Sagami Yodan Co., Ltd. has been using oxy-fuels to cut and weld metal plates. The company introduced a CO2 laser processing machine in 2006 to ramp up its strength in quick delivery. However, local competition increasingly used laser processing machines reducing Sagami Yodan’s advantage. The company decided then to bring in the ML3015GX-F60 fiber laser processing machine (the GX-F60) in January 2021 to replace its CO2 laser machine.
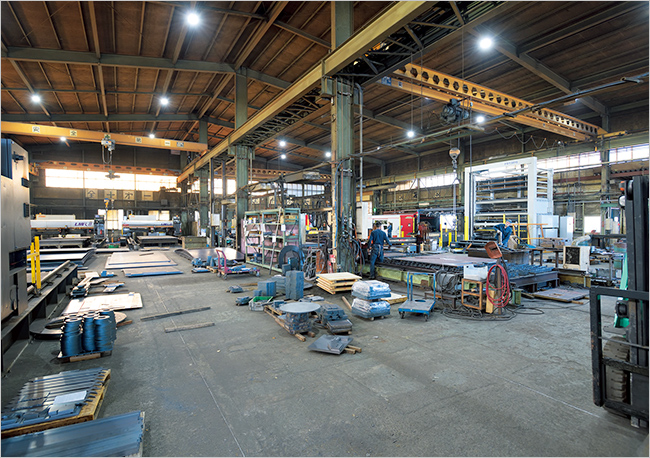
The factory in full-view. The ML3015GX-F60 and FOT3015 can be seen at the back right. As well as the oxy-fuel cutting machine, the company has four other different make laser processing machines brought in by the previous president in 2006.
One of the things that is now possible with the introduction of the GX-F60 is precise cutting of plates over 6 mm thick, as well as high-quality small hole machining, something which was also extremely difficult. Not only can the company now process metal sheets from as thin as 0.1 mm up to 22 mm thick, a size which couldn’t be cut in the past, but it can also do this at high speed. For example, in the case of steel plates with a thickness of 6 mm or less, what used to take five to six hours, can be achieved in under an hour. Additionally, small holes with a diameter of 9 mm or less can be drilled into thick plates with a high degree of precision.
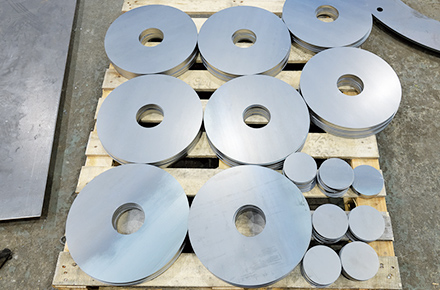
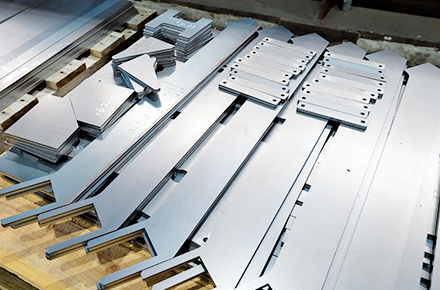
Finished cut and drilled products. With the ML3015GX-F60, small holes with a diameter of about 4 to 5 mm can be machined into thick plates of 16, 19 or 22 mm to a high standard of quality, earning favorable ratings from customers.
“Previously we couldn’t take orders for any size less than 9 mm in diameter because of the risk, but now we can machine small holes well below 9 mm so our customers are very happy with us,” says CEO of Sagami Yodan, Hidefumi Ikawa. In the past contractors would have had to ask a specialist machining company to make small holes when required. This of course took time and increased costs. Now that Sagami Yodan can machine small holes, the company has become more valuable to its customers, earning itself a good reputation.
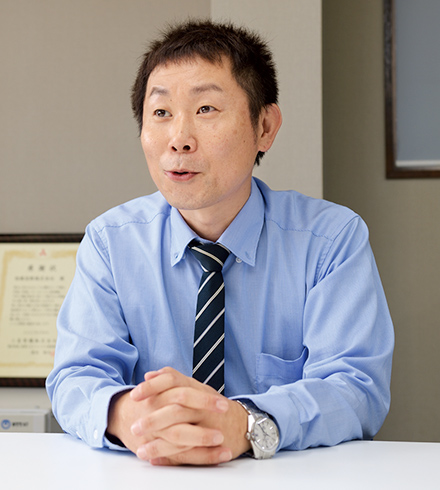
Hidefumi Ikawa, CEO, Sagami Yodan
The GX-F60 has an AI (Artificial Intelligence) assist function that automatically changes the control settings so that machining can carry on securely, reducing errors to a minimum during the cutting process. With the previous processing machine, burning would often occur during drilling, which increased wastage. But with the AI assist function, they no longer have this problem.
“If we are to thrive, we must automate everything”
In addition to the GX-F60, Sagami Yodan has also introduced the FOT3015 automatic sheet change system. “If we are to thrive, we must automate everything that can be automated. It’s certainly not cheap, but of course we’ve introduced automation to our factory in the knowledge that the results will outweigh the costs,” explains Ikawa.
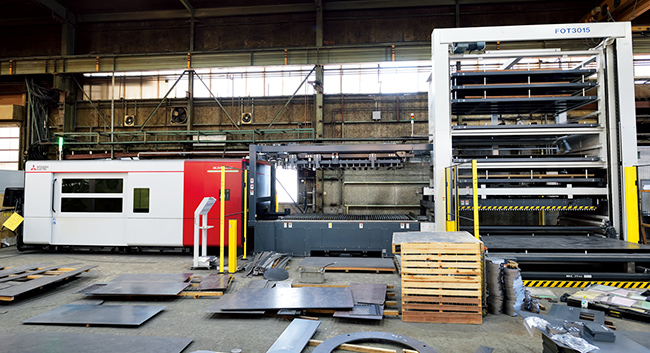
The ML3015GX-F60 (left), a 2D fiber laser machine with an output of 6kW, has not only enabled high-speed cutting of thick plates but has also eliminated instances of burning which had happened in the past during processing, eradicating errors in the cutting process with its AI assist function. The FOT3015 automatic sheet change system (right) has 8 levels, 4 for the raw materials and 4 for the finished product.
With the introduction of the FOT3015, materials and machined pieces can be automatically fed in and out, helping to significantly automate and streamline the process. For example, if an order for 500 pieces is received in the evening, it is now possible to turn it around and get it done by the afternoon of the next day. This wouldn’t have been possible before, significantly improving delivery times. Depending on the quantity and level of precision, it is not uncommon for orders received in the morning to be delivered that afternoon.
“Since the cutting speed has improved significantly compared with our previous machines, we can finish big orders much more quickly. The total running cost, including electricity, has also come down. And with the automatic sheet changer, the loading of new materials after cutting can be done without the need for a factory worker, meaning the machine can run every day and during the night without stopping,” says factory manager, Shuji Furuhashi on how the machine has helped streamline operations.
The GX-F60 also benefits from iQ Care Remote4U, a service that allows users to remotely check how the processing machine is operating. “It’s very useful. I use it on my smartphone to see operating data and I can check to see what the problem is if the machine stops running at night for whatever reason.” says Furuhashi.
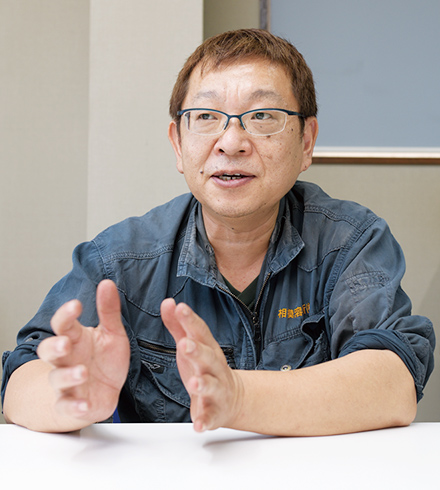
Shuji Furuhashi, factory manager
Ryosuke Hashida, who is in charge of computer-aided design and is also involved in the operation of on-site processing machines, says, “The number of materials we can now load onto the machine has increased hugely. This increase means that we can also cut a greater amount, so as well as quicker delivery times, we’ve been able to take on more orders. I hope we can continue to do more and more in the future.”
With limited factory space, it was difficult to store enough stock to respond quickly to sudden orders or supply issues. With the introduction of the FOT3015 however, Sagami Yodan has been able to make better use of its factory policy of increased stock levels. In this way, the introduction of the GX-F60 and the FOT3015 is also changing the way Sagami Yodan runs its business.
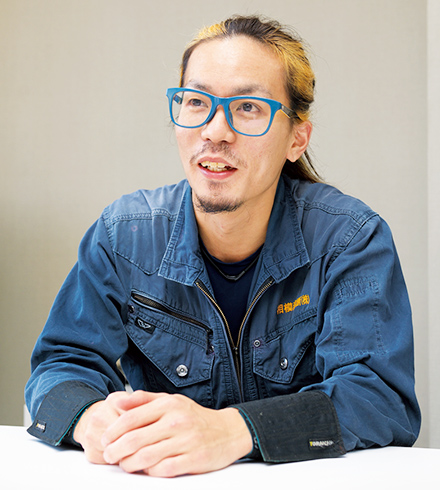
Ryosuke Hashida, involved in running the processing machines on-site
“Demand has not grown that much, because of the pandemic, but since we can cleanly cut more materials, we want to focus on processing a wider range of materials in the future such as stainless steel and aluminum,” reveals Ikawa.
Products and Solutions
SAGAMI YODAN CO., LTD.
- •Established in 1981.
•Metal plate processing with laser processing machines, and oxy-fuel welding and cutting