Reducing maintenance costs and improving safety
First released February, 2021
“…with devices and wiring that have been in use for over 40 years....it's not realistic to replace them all for new……we had to handle the problem by raising the daily monitoring levels…”
Shinya Ueki, Senior Technician of Nitto Denko Production Technology
NITTO DENKO CORPORATION- Manufacturing, Japan -
Dr. Energy
Who would have thought that the management of energy could lead to more efficient maintenance processes and the increase of plant safety? That was exactly the result of this e-F@ctory application created by Nitto Denko Corporation at their Kameyama Plant.
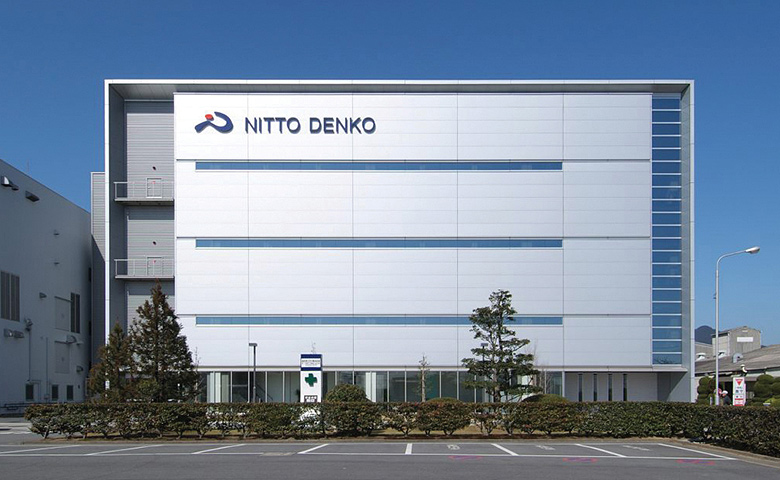
Summary:
As flammable liquids are used at the plant any electrical fault could lead to fire, but by using Mitsubishi Electric’s MELSEC-Q Series insulation monitoring module QE82LG, to monitor electrical devices and wiring for insulation deterioration, countermeasures have been strengthened without reworking major equipment.
Key Points:
- 1.Rapid identification of leakage points has led to an efficient renovation process
- 2.Making use of existing facilities yet still enabling the rapid execution of electrical fire countermeasures
- 3.Continued safety improvement in parallel with cost reductions
Having developed specialist knowledge in technologies such as adhesives and coatings, Nitto continues to apply this understanding and provide unique products to diverse business areas like; electronics, automobiles, and residential building materials. Among other things, their Kameyama Plant is responsible for the production of CISFLEX®, a thin-film metal-based board used for precision circuits in hard disk drives as well as transparent resin for LED sealing and polarizing film for liquid crystal displays.
Operation began at the Kameyama Plant in 1969. Plant 2 has been in operation ever since, with products including the varnish which protects coils in ecological car motors and moisture-proof coatings for electronic substrates. Both use flammable liquids in their manufacture necessitating the establishment of strict fire control standards; even so, concerns arose about leaks from old wiring and electrical machines used at Plant 2.
“Plant 2 has no shortage of devices and wiring that have been in use for over 40 years, since it began operation. But it’s not realistic to replace them all for new. We had to handle the problem by raising the everyday monitoring level.” said Mr. Shinya Ueki, Senior Technician at the Production Technology Section of Nitto ICT Sector Manufacturing Supervision Department.
As a general rule, the two major causes of plant electrical fires are overheating at loosened connection or contact areas of circuits, and electrical leakage. Nitto handles the former with yearly maintenance checks using thermography but the problem was in the latter case.
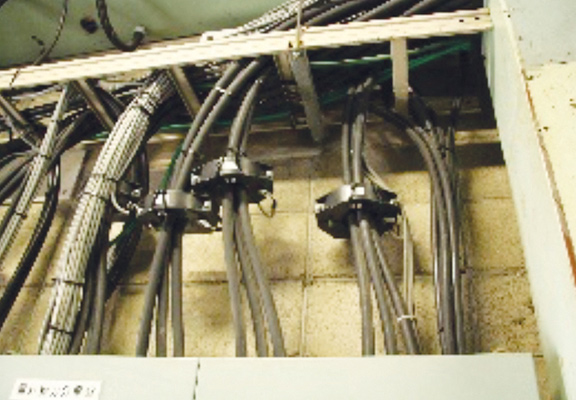
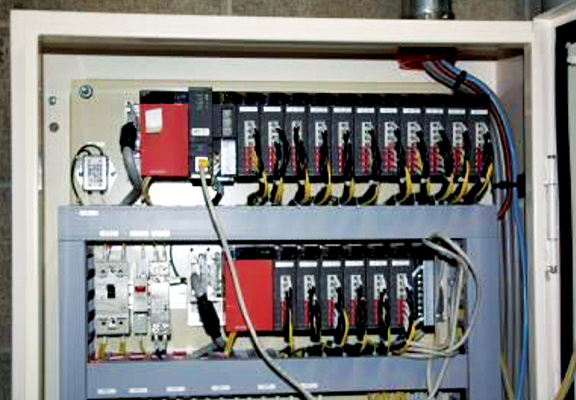
The ZCT (left) mounted on the cables at the base of the panel board sends leakage current information
To the insulation monitoring module “QE82LG” (right) within the panel board for processing.
“We used to check the insulation monitoring equipment set up for each transformer but with multiple loads connected in parallel, it was difficult to pinpoint problem locations. And then, leaks through surface moisture would naturally dry and disappear while we were investigating, and we’d never find the cause.” commented Ueki.
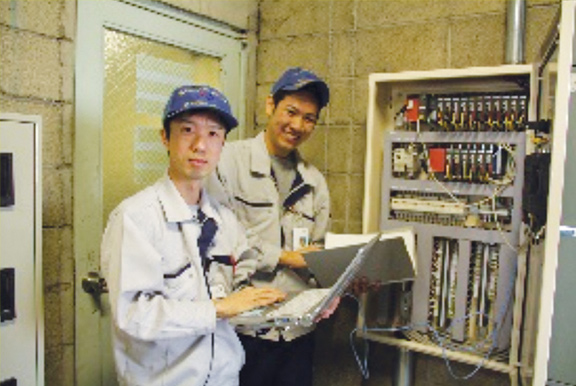
Senior Technicians Mr. Ken’ichiro Nishiwaki and Mr. Yoshiaki Sugimoto were also involved in the introduction process. “It’s easier now to identify leakage points.”
In order to eliminate this kind of problem, what was needed was a system that could monitor leaks individually, close to the load and inform the supervisor immediately. Nitto turned to Mitsubishi Electric’s insulation monitoring module QE82LG.
Rapid identification of leakage of unknown origin is now a real possibility
As part of Mitsubishi Electric’s general purpose PLC MELSEC-Q Series, the QE82LG module can measure leakage current for individual circuits. Notably, it can accurately monitor insulation deterioration through measuring the amount of resistance leakage current occurring due to wiring or device deterioration.
Nitto placed 30 QE82LGs in the transformer room and 22 in the cubicles of its Plant 2. The Zero-phase Current Transformer (ZCT) mounted on the cables at the base of the panel board is used to send leakage current information to the QE82LG which processes it.
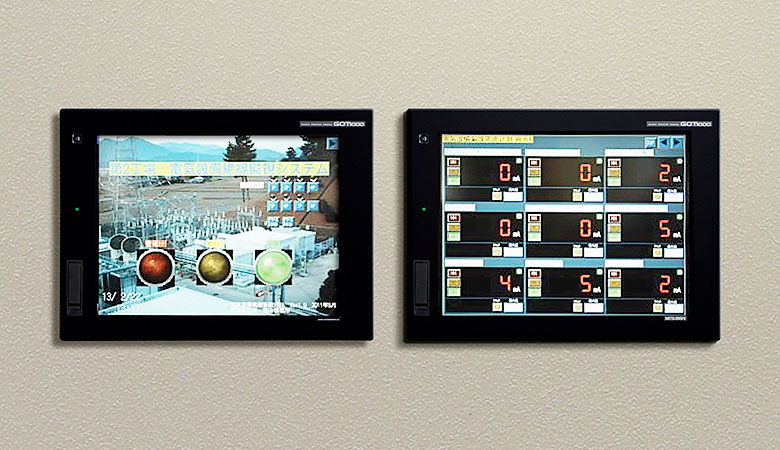
Main display screen (left) and individual monitoring results display screen (right) on the GOT. Values exceeding the set threshold values light up in yellow or red.
Measurement results are displayed on the GOT (Graphic Operation Terminal) display. The QE82LG allows two types of alarm threshold value to be set; in this case Nitto set an electric-shock level of 30mA and a potentially fire causing leakage-level of 200mA. If any of the total 52 monitoring devices should exceed these levels, even once, the GOT displays the leakage point in yellow or red and emits a warning.
By changing leakage monitoring from per-transformer to per-panel board, leakage causes which could not be determined in the past have now become increasingly clear. “For instance, once we had a case where the company doing wiring installation got the connection wrong, so that load current flowed onto the ground side. At the time we couldn’t find the cause, but after introducing leakage monitoring, we’ve been able to identify causes immediately in similar cases,” explained Ueki.
Furthermore, in cases involving phenomena like moisture-caused leakage (where the cause naturally evaporates) identification is now easily done at panel board level, meaning that it is now possible to renovate leakage points much earlier and prevent fire-related accidents. In addition, being able to see leakage current by circuit numerically is a saving grace for the maintenance staff. Ueki further explained “The usual practice is alarm-point management but being able to see the numbers all the time lets us grasp the status trends and respond more quickly.”
The implementation costs fitted well within Nitto’s budget. One major reason was that they were able to create the GOT display screens and monitoring programs themselves. “By using the components provided by Mitsubishi Electric, the screen programming was completed in two weeks, and implementation took just a month, even with the rest of the design. If it had been something complex that we couldn’t design ourselves, the costs would probably have soared,” noted Ueki.
Better organization of maintenance activities
Nor is fire prevention through insulation monitoring the only effect of the introduction of the insulation monitoring module. Another major advantage is its promise of future maintenance cost reduction.
Plants operating with more than 7,000V are required to name a chief electrical engineer and to present maintenance and safety regulations. Nitto’s Kameyama Plant, also subject to these rules, is bound to observe strictly the regulations as presented and to prevent electrical accidents and failures. However, as the targeted facilities age, their risk of failure also increases, meaning that it is necessary to implement additional maintenance procedures along with more frequent conventional maintenance. As a result, the maintenance costs tend to increase year by year, and the process itself cannot be avoided.
However, “I have the feeling that we can replace a lot of our current maintenance process through new maintenance methods. Looking at the case of this insulation monitoring system we’ve introduced, maintenance activities measuring insulation resistance and so on of the panel board, were meant to confirm the state of the insulation of the devices and wiring, i.e. whether there’s any leakage. I think [the new system] probably gives us good enough reasons to simplify it, reducing measurement frequency et cetera.
“That is, by organizing the maintenance activity, we can both improve maintenance quality and reduce maintenance costs.” suggested Ueki. The fact is that when, as in the case of Plant 2, devices and wiring on site are used beyond the manufacturer’s recommended replacement values, things can go wrong at any time.
A fixed cycle of maintenance may well not be enough to prevent accidents completely. What is essential is to have regular system monitoring which detects trouble more quickly and Nitto judged that insulation monitoring using the QE82LG would be effective in this vein.
Having confirmed the effects at Plant 2, Nitto now plans to consider introduction to other factories such as Plant 5. “Plant 5 started operation in 1985 and is about to hit 30 years old. Because it makes sealing resin for LEDs, it’s full of powder1, and has a higher chance of leakage than other plants. We plan to move on with introduction while analyzing the insulation deterioration risks at other factories,” concluded Ueki.
Looking ahead, they are envisioning future plans such as a system which would inform maintenance staff of alarms wirelessly from the PLC when a leakage occurs. The effects of the introduction of QE82LG’s insulation monitoring for safety and security seem to be even greater than they had imagined
Products and Solutions
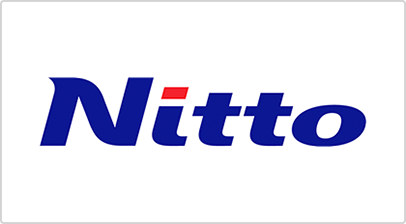
Nitto Denko Corporation
- Nitto has been inspiring customers through the creation and development of innovative ideas since its foundation in 1918.Nitto is winning the leading position by leveraging proprietary technologies in niche markets such as Polarizing films for displays, Thermal release sheets, and Thin-film metal circuit board for HDD head.
- URL : https://www.nitto.com/jp/en/