Quality
Basic Policy and Management
Basic Policy
Based on its Purpose, “We, the Mitsubishi Electric Group, will contribute to the realization of a vibrant and sustainable society through continuous technological innovation and ceaseless creativity,” the Mitsubishi Electric Group constantly strives to increase customer satisfaction in all aspects of its business, from the production of high quality, easy-to-use products to after-purchase support, response to major issues, and product disposal.
Basic Philosophy on Quality
The Mitsubishi Electric Group established the Four Basic Quality Assurance Principles that reflect the spirit of quality as the top priority identified in the Memorandum of Quality issued by the president in 1958. However, in 2021, many improper quality control practices were made public. Therefore, the Basic Quality Assurance Principles were revised as below in November 2023 incorporating feedback from employees.
Under the Basic Philosophy on Quality, the Group will realize a system and a workplace that eliminates incentives for improper quality control practices.
Basic Philosophy on Quality
- We offer the quality that ensures customer satisfaction.
- We provide products and services with quality as our top priority.
- We each plays self-leading role for creating better quality.
Management
The Corporate Quality Assurance Reengineering Group has been implementing company-wide measures to promote quality assurance reform and strengthen activities for improving quality. The Corporate Quality Assurance Reengineering Group has a Quality Assurance & Management Department at each manufacturing base, which assumes the function for checking, including shipping authority, as well as a contact point for consultation on issues in the field.
The Three Key Reforms Division* directs the Corporate Quality Assurance Reengineering Group based on reports and consultations from the Group. In addition, the Quality Governance Subcommittee has been monitoring and checking the effectiveness of various initiatives carried out under the quality assurance reform on a regular basis with the advice of outside experts.
Three Key Reforms Monitoring Committee, established under the Board of Directors, monitors and oversees the status of each measure.
- The Three Key Reforms Division is composed of the relevant executive officers, including the CSO/CRO, and steadily promotes reforms in the three key areas of quality assurance reforms, organizational culture reforms, and governance reforms. It also responds to the monitoring and supervision of the progress of the Three Key Reforms by the Board of Directors and is responsible for appropriate disclosure of information to stakeholders.
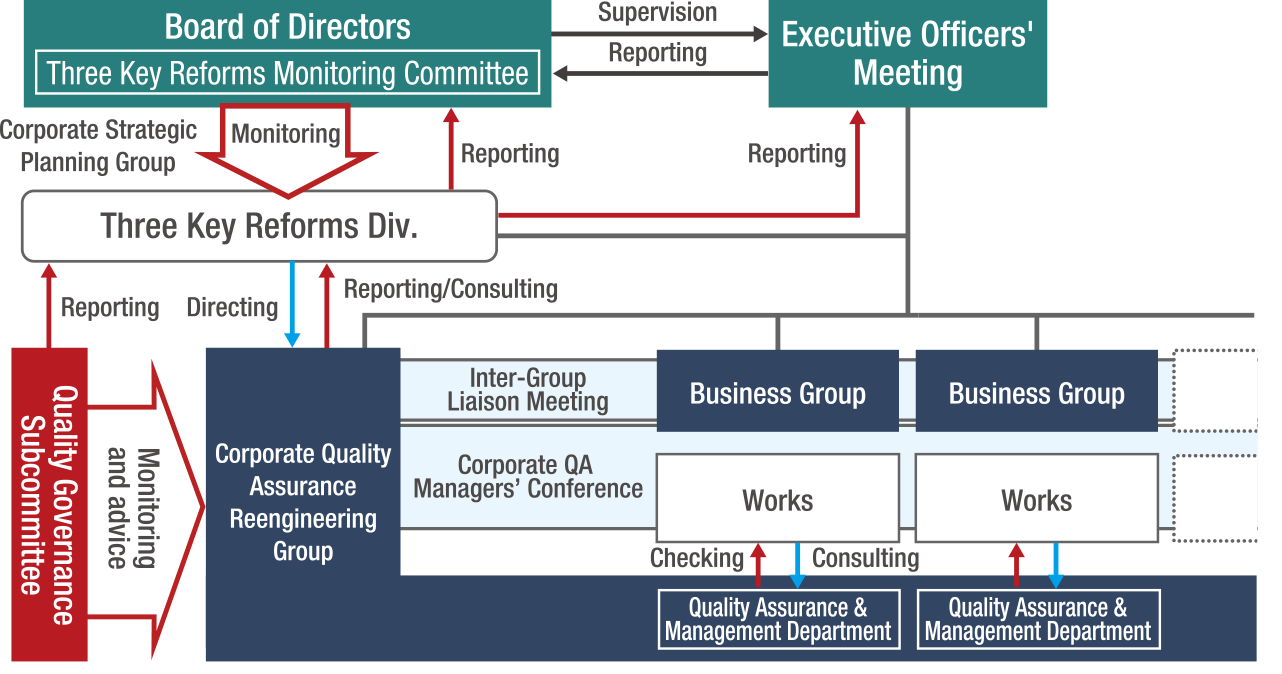
* Quality Assurance
Quality Improvement Activities
The Mitsubishi Electric Group promotes quality improvement activities in all business processes related to products and services to improve quality, safety and reliability while promoting human capital development.
With regard to development and design in particular, we strive to develop human capital who are capable of assessing each country’s laws and standards, customer requests, and basic product functions as well as executing and driving designs and evaluation that ensure and guarantee safety, reliability, and stability of functions. These human capital improve our development and design quality by ensuring, alongside other efforts, all parties involved are familiar with the elemental technology guidelines necessary for ensuring quality.
As a part of the quality assurance reform, we also completed capital investment in the area of strengthening quality through use of IT and digitalization exceeding the initial plan (30.0 billion yen) in fiscal 2024.
As for procured products, we have been working to improve quality in collaboration with our suppliers, who are important partners of the Mitsubishi Electric Group, by asking them to understand our policy that gives top priority to quality.
With regard to product defects, we have also built a database of failure cases that have occurred in the Mitsubishi Electric Group. We use this database to build quality into products to prevent defect recurrence.
Providing Easy-to-Use Products
Basic Policy
The Mitsubishi Electric Group engages in universal design under the principle of “creating user-friendly products and comfortable living environments that benefit as many people as possible.” To achieve user-friendliness and comfortable living in the true sense of the words, we are committed to providing products and living environments that offer a high level of satisfaction to as many people as possible.
Mitsubishi Electric Group’s Efforts in Universal Design
We have applied the concept of universal design (UD) to home appliances such as air conditioners and refrigerators, as well as to public equipment such as elevators, by considering the needs of all users. This approach is continuing to evolve.
Universal Design Guidelines for Widespread Usability
The Universal Design Guidelines are a comprehensive set of standards that apply to a wide range of product development to ensure usability of our products by all users, including children, senior citizens, and people with physical disabilities. These guidelines address the changes in human characteristics that occur with age and consider various disabilities. They are organized around four key perspectives: recognition, identification, physical use, and safety/usability.
UD-Checker, the Universal Design Evaluation System
UD-Checker is Mitsubishi Electric’s proprietary tool that can be used by both industrial designers and engineers to evaluate universal design qualities.
This tool shows four quantitative measures of universal design, namely recognition, identification, physical use, and safety/usability, indicating specific design aspects for development and improving the efficiency of product development. The UD-Checker is used on a wide variety of Mitsubishi Electric Group products from home appliances and public equipment to industrial equipment.
The UD-Checker’s Four Evaluation Criteria
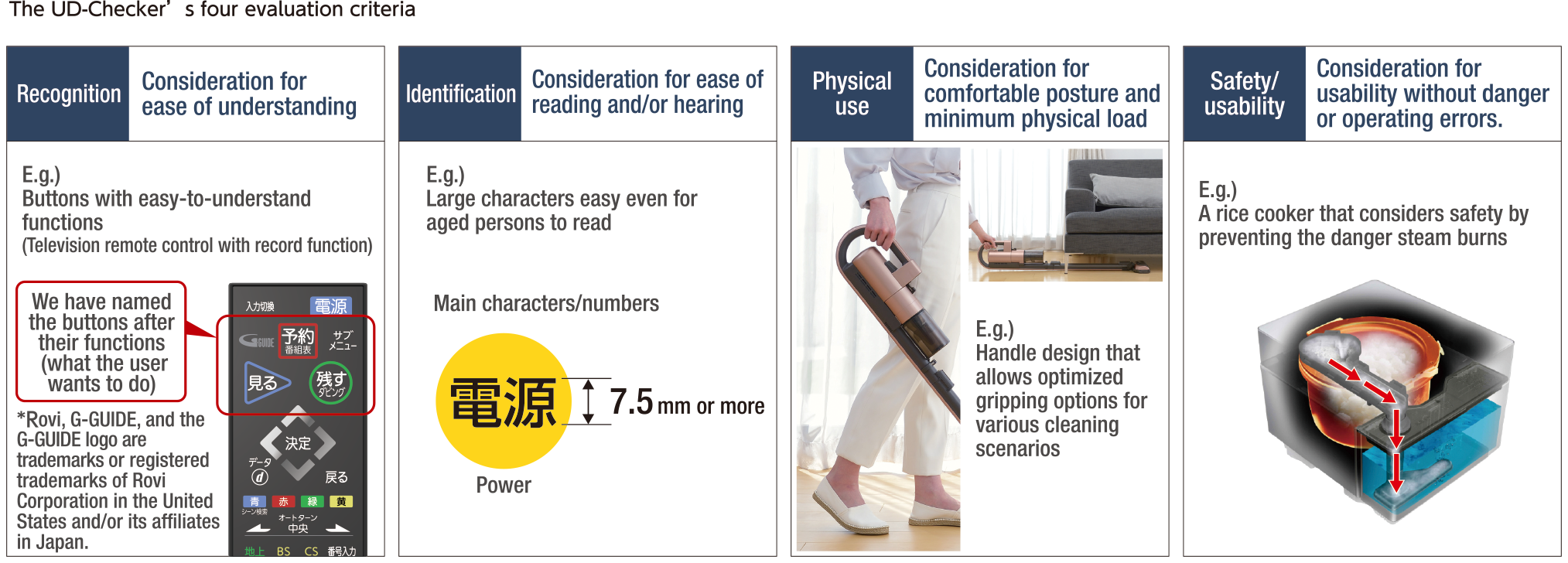
Universal Design Examples to Date
Application to Home Appliances
Mitsubishi Electric has been ahead of the game in applying the concepts of universal design to home appliances. For instance, we have applied the Universal Design Guidelines to the IH cooking heater.
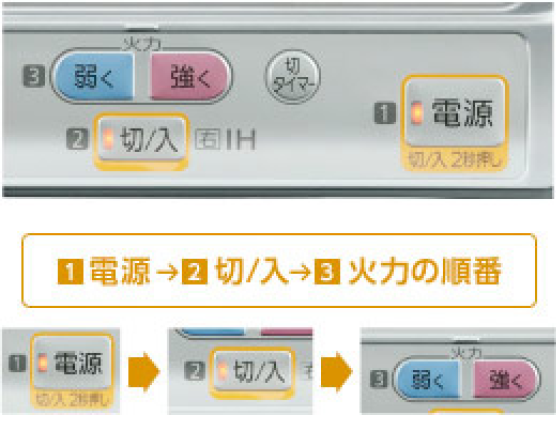
Large character & numerical indication of steps for use
“RakuRaku-IH” Cooking Heater CS-G221AKS
Large characters & numerical indicators of steps for use
Features
Characters are approximately 1.8 times the size of our conventional system. (Compared with Mitsubishi Electric's conventional model G38MS)
Can be operated simply by pressing buttons in order of numbers displayed.
Application to the Industrial Sector
Even in the industrial sector, where there is a high level of specialization and a relative lack of diversity in terms of operators who handle equipment, the labor environment is changing. Examples of this transformation include the aging of workers, and more foreign and inexperienced workers—changes that have increased the need for universal design. At the Mitsubishi Electric Group, we are applying the concept of universal design to our industrial products, such as factory automation equipment and electric power devices, as well as to the installation and maintenance of equipment on factory floors.
Creating Easy-to-Understand Instruction Manuals
Under a campaign to provide first-rate instruction manuals, the Mitsubishi Electric Group is directing its efforts to create easy-to-read and easy-to-understand instruction manuals to ensure the safe and comfortable use of our products. Forming the basis of this effort is Mitsubishi Electric’s original “Guidelines for the Creation of Instruction Manuals for Home Appliances—Instructions.” To raise the quality level of instruction manuals, this handbook is distributed to all associated companies in Japan that handle home appliances.
Award Received
In fiscal 2024, we won the following awards at the IAUD International Design Awards organized by the International Association for Universal Design (IAUD). All of the winning products below received awards due to the exploration of the needs of consumers and users and the design of styling and functions to realize usability that meets those needs.
- Multi-Use Delivery Service Robot System for Hospitals: A collaborative robot with a friendly design that is also supportive of medical professionals (Silver Award)
- Wall-Mounted Circulating Fan: A simple, easy-to-use fan (Bronze Award)
- Large-Capacity Home Freezer U22: A large-capacity, easy-to-use refrigerator (Bronze Award)
Mitsubishi Electric will continue creating products and services that leverage the extensive range of its technologies to solve the problems of users.

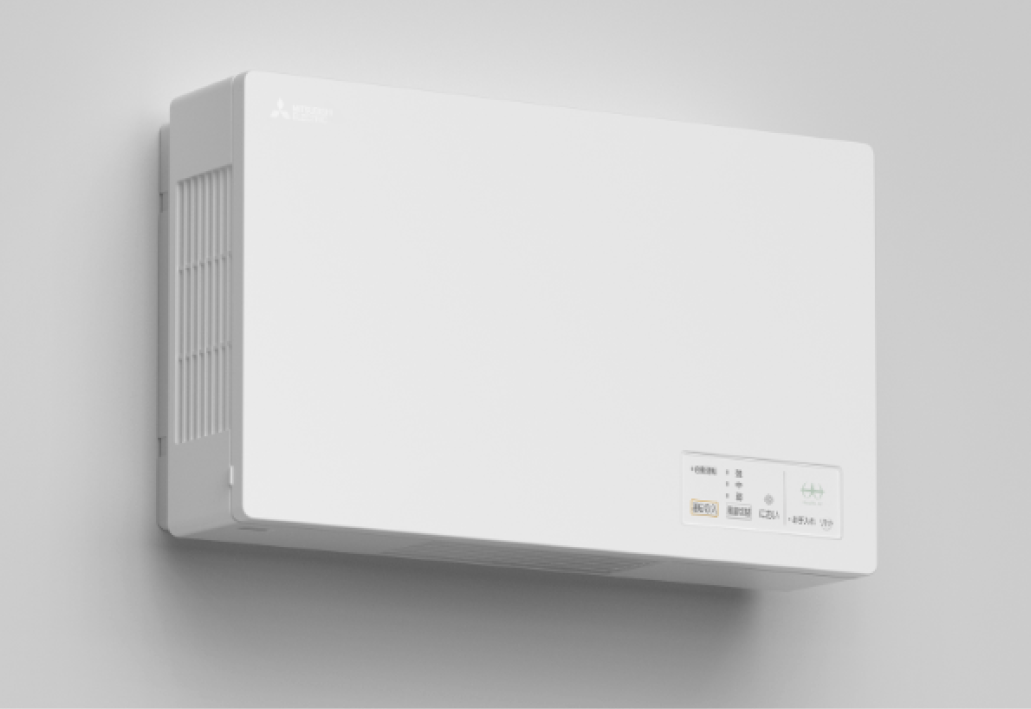
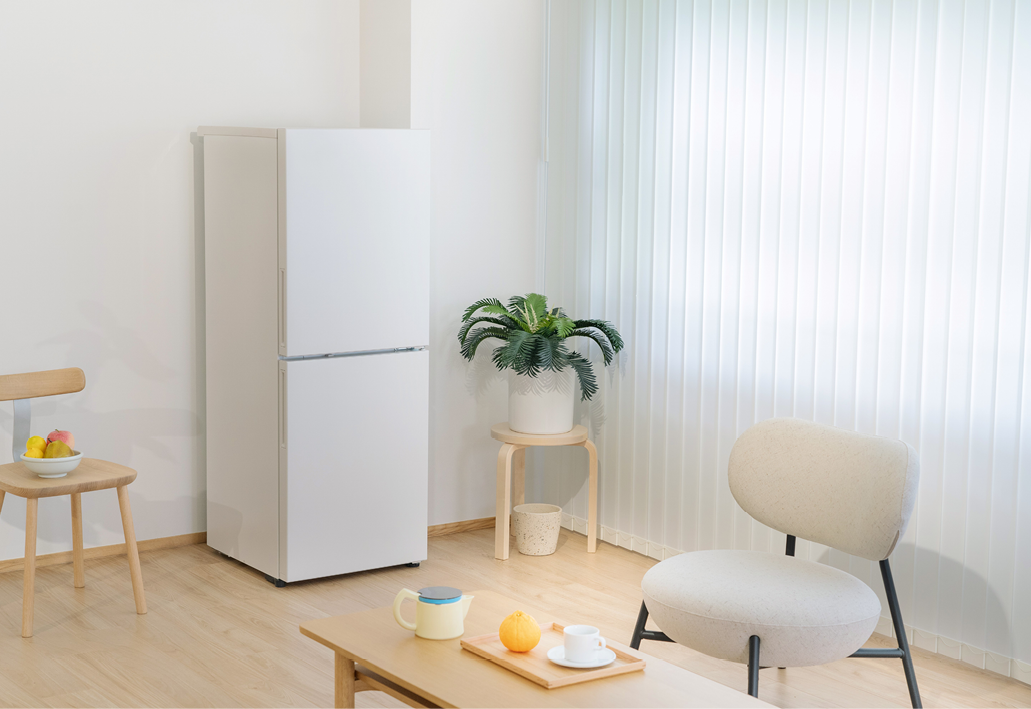
Improving Customer Satisfaction
Basic Policy
The Mitsubishi Electric Group has been committed to customer satisfaction since its founding. Inheriting this spirit, we collect feedback from our customers through customer satisfaction surveys as appropriate to the characteristics of each business operation and incorporate customer opinions into product development, marketing strategies, and services.
We also strive to maintain customer satisfaction by strengthening our repair/service systems, providing effective staff training, and expanding access to information via our websites.
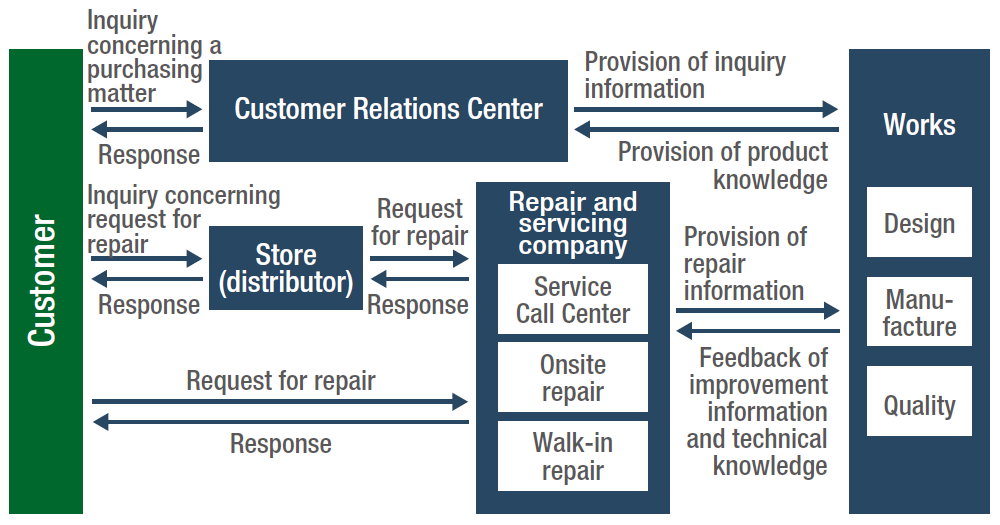
CS Activities by the Home Appliances Group (in Japan)
The Living Environment & Digital Media Equipment Group handles matters related to home appliances and carries out customer satisfaction (CS) improvement activities. These activities are aimed at ensuring that Mitsubishi Electric products are available to as many people as possible and that customers across the country can use the product they purchase with confidence. We value contact with customers and retailers, offering guidance on purchasing decisions, product usage, and after-sales service. We continuously strive to incorporate feedback from these interactions into future product development, sales, and service improvements.
Taking Calls 24 Hours a Day, 365 Days a Year
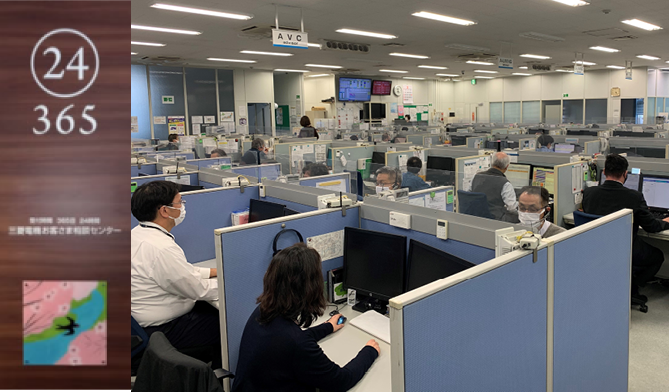
Customer Relations Center
To satisfy customer expectations, it is necessary to carefully observe behavior and preference of customers throughout the sales, service, development, and manufacturing stages, and to quickly detect and respond dynamically to signs of market changes. Mitsubishi Electric’s Customer Relations Center and Service Call Center responds to product inquiries 24 hours a day, 365 days a year, ensuring prompt resolution of customer inquiries and concerns.
The Technical Support Call Center, which responds to technical inquiries from distributors, and the Repair Service Station, the stronghold of repair services operated by Mitsubishi Electric System & Service Co., Ltd., also respond to inquiries 365 days a year (excluding some regions).
As the Customer Relations Center receives a wide array of inquiries every year due to the diversification of product functionality, we are constantly reinforcing staff members, and are making consistent efforts to provide proper training.
System of Reviewing Customers’ Comments
The content and results of consultations and repair requests from customers and the details of technical inquiries are sent as feedback to the manufacturing works. They are used to improve both products under production and in development, and to provide repair information to distributors.
The Customer Relations Center compiles a database of customer feedback and periodically sends the results of trend analysis to works, sales companies, and research institutes. Works and sales companies strive to improve current products and simplify instruction manuals, while research institutes use the information to improve products under development. At the same time, regular liaison meetings are held between works and Customer Relations Center to address issues and improve information collection.
Shizuoka Works has created opportunities for engineers to hear feedback from customers directly in order to improve the quality of room air conditioners "Kirigamine." When quality problems arise, engineers visit the customer to check on the usage environment and provide feedback for product development. Such feedback is used to improve product design and control specifications. We have also reflected feedback from customers in our efforts to improve product quality with respect to perceived temperature control and the noise of outdoor units. We will continue to improve our products by using valuable customer feedback.
CS Activities by the Building Systems Group (in Japan)
The Building Systems Group handles elevators and escalators that provide vertical transportation within buildings and building management systems. By ensuring their safety and security and continuously delivering comfortable means of transportation and living spaces as indispensable social infrastructures on a global scale, we contribute to making society even more vibrant and sustainable.
24-Hour, 365-Day Safety Hotline
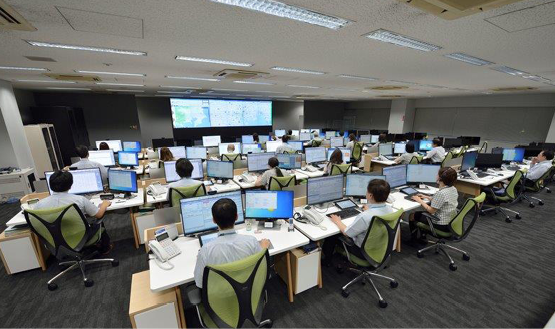
Information center
Information Centers situated in eight locations throughout Japan provide a safety hotline for responding to and dispatching engineers in cases such as failure signal issues or customer calls regarding building facilities.
Information Centers constantly monitor remotely the status of contracted customers’ building facilities. When an error signal is received, the system provides information on the current locations, works in progress, and even the technical levels of approximately 6,000 engineers. This ensures that the most suitable engineer who can arrive the earliest and respond most effectively is dispatched.
The system also supports the quick recovery of building functions by taking actions such as sending repair history information and other details related to the building to the engineer or processing urgent orders for parts.
Moreover, by monitoring changes in data on the operational status of elevators and air-conditioning facilities, information centers strive to detect and address abnormalities before they develop into malfunctions and prevent problems from occurring.
Mitsubishi Elevator and Escalator Safety Campaign
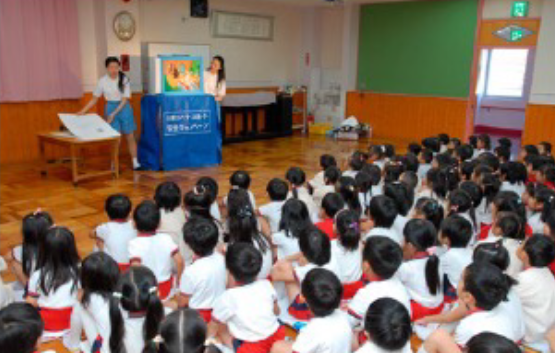
Mitsubishi Elevator and Escalator Safety Campaign
Elevators and escalators are used to transport a large number of persons, so a high level of safety is imperative, and they are thus equipped with various safety devices and functions.
At the same time, regular maintenance and inspection and correct use are necessary to ensure safe operation.
The Mitsubishi Electric Group conducts the Mitsubishi Elevator and Escalator Safety Campaign, which includes user briefings to promote awareness of proper and safe elevator and escalator usage. Additional briefings are held for apartment and building owners and managers, focusing on daily management practices and emergency response procedures. These sessions have been attended by more than 300,000 people to date and will continue to be held as an important safety activity of the Mitsubishi Electric Group.
Product Safety-related Principles
Basic Policy
Based on the Purpose and Our Values, the Mitsubishi Electric Group promotes product safety initiatives under its Product Safety-related Principles.
With regard to consumer products particularly, Mitsubishi Electric is committed to preventing serious hazards that could result in death, injury, fire, or other damage, by subjecting all products to a quantitative risk assessment at the development stage, while also designing and developing products in consideration of their end-of-life management (to ensure safety even at the stage where products are prone to break or be discarded).
At the same time, our Service Call Center and Customer Relations Center in Japan operates 24 hours a day, 365 days a year to gather information on product-related issues.
Responding to Product-related Issues
Basic Policy
If we receive any report of a major issue occurring in a product that we have sold, we have a system in place that includes the top management to ensure quick and accurate decisions on the steps and measures to take, so that we can take proper action while always placing top priority on not inconveniencing our customers. In addition, we will share information on major issues that occurred with regard to products across the entire Group promptly to strengthen our ability to respond to such issues.
For recalls in particular, we work on an ongoing basis to ensure that all the relevant products that were sold are returned and repaired, and apply these efforts to a wide array of sales channels.
Reporting Major Product Issues
A detailed list of information pertaining to important product-related and quality issues is posted on Mitsubishi Electric’s Japanese-language official website.
Accident Reporting Based on the Consumer Product Safety Act
In Japan, we promptly release appropriate information on issues in consumer products, which directly and deeply affect consumers.
Detailed information on our compliance with Japan’s revised Consumer Product Safety Act, which went into effect in May 2007, is available on Mitsubishi Electric’s Japanese-language official website.
Under its policy regarding the disclosure of accident information, the Mitsubishi Electric Group also discloses information on cases that are accidents related to products other than gas or oil equipment and that have not been identified as accidents caused by products or that have been determined as being uncertain as to whether they were caused by products.
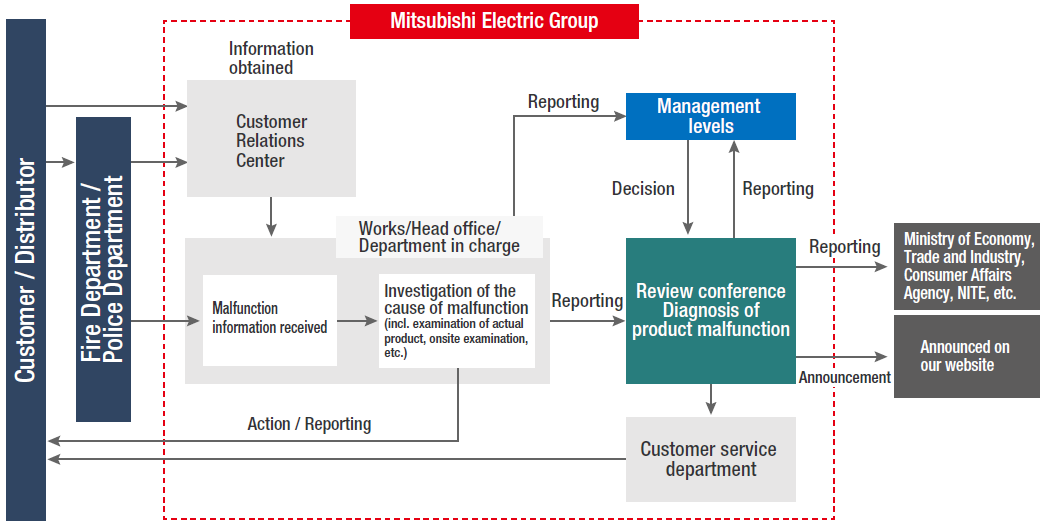