Hyper Cycle Systems Corporation, a member of the Mitsubishi Electric Group, has commercialized resource recovering and recycling from used home appliances and electronics. Information obtained from this plant is fed back to product designs to enhance the recyclability of products.
Environmental Considerations in Value Chain Management
Environmental Considerations in Value Chain Management
Mitsubishi Electric implements a range of initiatives that give consideration to the environment throughout the value chain, from the development of products through their use and recycling.

Implementation of Environmentally Conscious Design —Utilization of e-Pro System (Development)
The Mitsubishi Electric Group utilizes e-Pro System (product environmental information collection system) to centrally manage product environmental data such as CO2 emissions from product use and raw materials and packaging materials used. This system conforms to customer requirements to provide product data and is used in environmentally conscious design, by enabling environmental assessment and LC-CO2 to be implemented and fed back to design departments.
Additionally, to strengthen product designs that address social needs for decarbonization, internal subcommittee meetings are held to share information on laws and regulations in each country and best practices on environmentally conscious designs. These meetings also examine the validity of LC-CO2 calculations and product assessment items.
Resource Recycling Initiatives —Improving the Usage Rate of Recycled Plastics (Development)
As a part of its efforts to recycle plastic materials that have a high environmental impact, the Mitsubishi Electric Group facilitates use of recycled plastic for our product parts through environmentally conscious design.
As an example of our efforts in fiscal 2024, we have developed technology to recycle PC/ABS* collected through the recycling of home appliances into recycled PC/ABS with stable quality, high durability, and fire retardance for wireless communication terminals for sensors used in gas meter systems and other applications. This has enabled reductions of approximately 70% in the volume of new plastic used in these components and 57% in CO2 emissions compared to manufacturing PC/ABS from new raw materials. In addition, we are working to expand the use of recycled plastics to other applications, such as plastic boxes for wire EDM machines and home appliances.
- A plastic which is a blend of polycarbonate (PC) and acrylonitrile butadiene styrene (ABS)
The Mitsubishi Electric Group manages and evaluates its usage rate of recycled plastics, which was 8.3% in fiscal 2024.

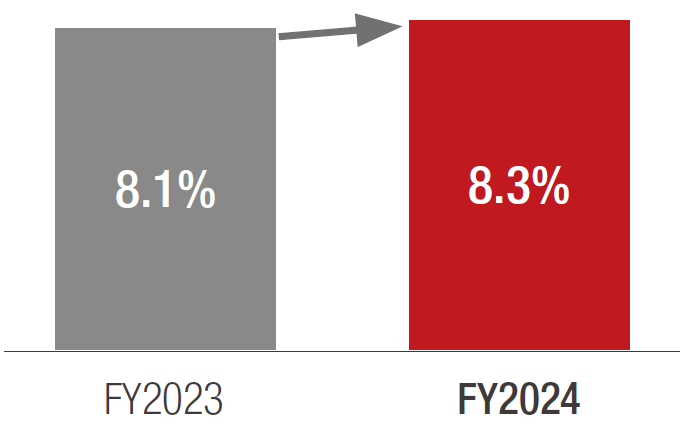
Reducing Greenhouse Gas Emissions from Plants and Offices (Production)
The Mitsubishi Electric Group is working to realize Environmental Sustainability Vision 2050 by promoting activities to reduce the emission of greenhouse gases (CO2 originating from energy use, SF6, HFCs, PFCs) from plants and offices.
Under the Environmental Plan 2023 (FY2022–2024), we aimed to reduce greenhouse gas emissions by more than 30% by fiscal 2024 compared to fiscal 2014. Toward achieving this target, we stepped up our efforts to thoroughly save energy and to expand the use of renewable energy in our plants and offices.
In fiscal 2024, greenhouse gas emissions decreased to a CO2-equivalent of 910 kt, down 41 kt from fiscal 2023. This reduction was the result of several factors: increased procurement of electricity from renewable energy sources; adoption of power purchase agreements (PPAs); and the facilitation of electrification of equipment and vehicles (company cars, forklifts, etc.). Additionally, production termination at one location due to business restructuring contributed to the decrease. In addition to establishing and operating energy-saving guidelines for buildings and production facilities, and promoting thorough energy saving in plants and offices, Mitsubishi Electric is also focusing on utilizing renewable energy. Going forward, we will flesh out further details of the road map for greenhouse gas emissions reduction and promote measures for even greater reduction, working steadily to achieve our targets.
Initiatives to Reduce CO2 Emissions Originating from Energy Use and Their Results
Working to reduce CO2 emissions originating from energy use, we systematically introduce and update high-efficiency and energy-saving equipment, improve operations, and extend energy conservation measures to production lines. In fiscal 2024, use of renewable energy and other measures in addition to these energy-saving measures reduced emissions by 12 kt from the previous fiscal year to 803 kt.
Half of this major achievement was due to the introduction of high-efficiency machinery, while cross-organizational activities for improving energy-efficient technologies also contributed solid results. These activities also focus on visualizing and reducing the wasteful use of utilities and production equipment.
In the classification system (SABC assessment) based on Japan’s Act on Rationalizing Energy Use, 11 out of 20 specific Group companies in Japan, including Mitsubishi Electric, have been recognized as excellent business operators (S Class) in terms of energy conservation.
Initiatives to Reduce SF6, HFCs and PFCs, and the Results
Three types of non-CO2 greenhouse gases are emitted by the Mitsubishi Electric Group in its business activities: SF6 (sulfur hexafluoride), HFCs (hydrofluorocarbons), and PFCs (perfluorocarbons).
SF6 is used inside gas-insulated switchgear for electrical insulation, as well as in the etching process during semiconductor and liquid-crystal display production. HFCs are used as refrigerants in air conditioners and refrigerators, while PFCs are used during the etching process in production of semiconductors and liquid-crystal displays.
In fiscal 2024, emissions were reduced by 29 kt year on year to 110 kt due to the switch to lower GWP* refrigerants, operational improvements, continued gas recovery and capture, and termination of operations at one location resulting from business restructuring.
- Global warming potential: A coefficient that indicates how many times stronger or weaker the effect of a greenhouse gas is compared to carbon dioxide.
Adoption of Renewable Energy
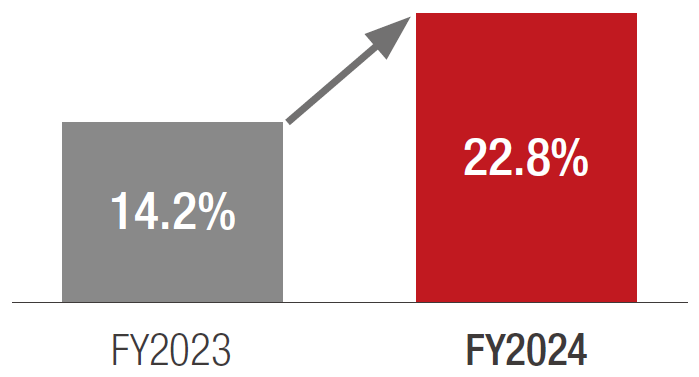
Renewable energy usage rate
The Mitsubishi Electric Group is expanding its adoption of renewable energy. The share of renewables in the Group’s total power consumption increased from 14.2% in fiscal 2023 to 22.8% in fiscal 2024.
Effective Use of Plastic Waste (Production)
Based on Japan’s Resource Circulation Strategy for Plastics, the Mitsubishi Electric Group is focused on effective use of plastic waste from its production sites, with a medium-term target of achieving 100% effective use of waste plastics by fiscal 2036.
Status of Initiatives by the Mitsubishi Electric Group (in Japan)
To improve the effective utilization rate of plastic waste emitted from our business operations, we conducted a survey of the present state of plastic waste at our production sites in fiscal 2022, and we are considering ways to enforce proper sorting and to conduct a review of plastic recycling companies.
In fiscal 2024, 26 kt of plastic waste were generated, which was unchanged from the previous year (26 kt), but the effective utilization rate of plastic waste significantly increased to 95.0%, achieving the target for fiscal 2024.
Going forward, we will endeavor to further control plastic waste output by promoting sharing of information on recycling companies among our production sites and visualization of plastic waste. We will also work to improve the material recycling rate of plastic waste.
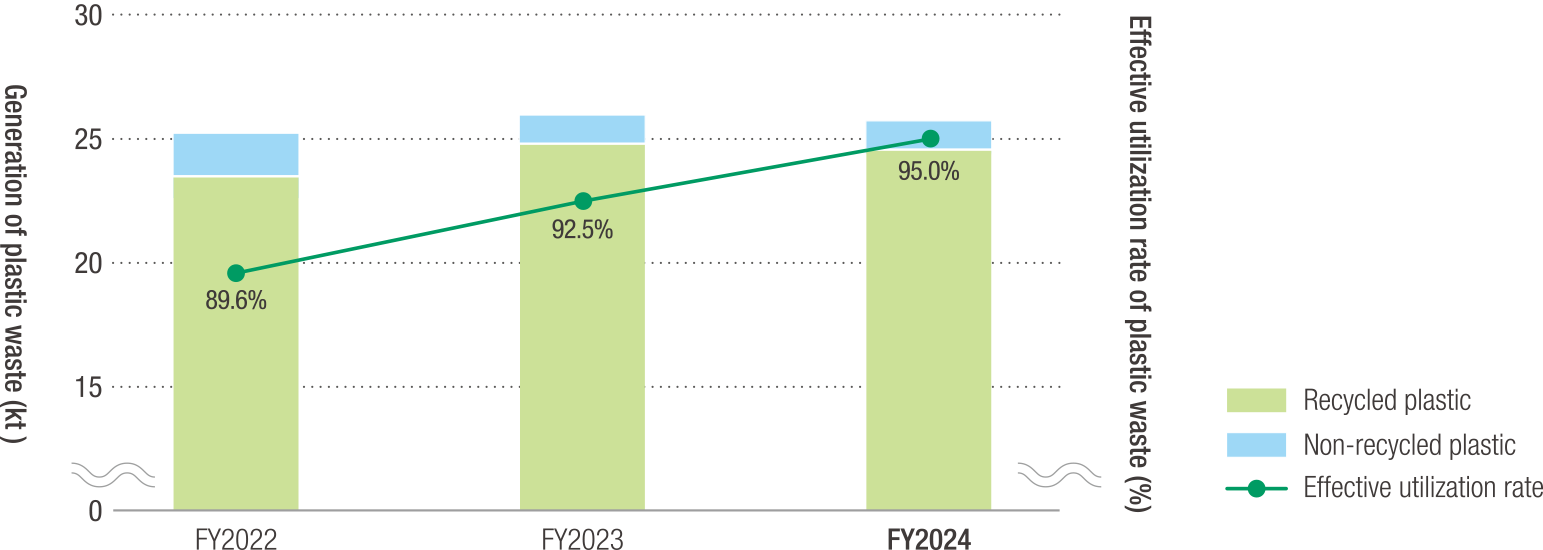
Status of Initiatives by the Mitsubishi Electric Group (Overseas)
Overseas laws, regulations, and waste treatment situations vary according to country and region. We work to assess the actual state of waste emissions and the status of recycling in order to establish targets suitable for each local situation, and we undertake various efforts to achieve those targets.
Specification and Disposal of Hazardous Wastes (Production)
The Mitsubishi Electric Group specifies hazardous wastes as shown below. The Group monitors their output and appropriately disposes of them in compliance with the laws and regulations of the regions in which its facilities are located. We also carry out material recycling and thermal recycling where we can in order to reduce final disposal (landfill) volume.
- Mitsubishi Electric Group in Japan: “Specially-controlled industrial wastes” specified by the Japanese Act on Waste Management and Public Cleaning
- Overseas associated companies: Hazardous wastes as defined by local laws and regulations
In fiscal 2024, total hazardous waste emissions of Mitsubishi Electric Group companies in Japan amounted to 1,432 tons, of which 436 tons were recycled. That of overseas associated companies totaled 5,311 tons, of which 2,689 tons were recycled.
Wastes containing polychlorinated biphenyl (PCB) are managed separately based on Japan’s Act on Special Measures concerning Promotion of Proper Treatment of PCB Wastes.
Reducing Water Usage (Production)
Managing Water Risk
Water risk is increasing worldwide with ever-more serious water shortages and pollution, as well as abnormal weather caused by climate change. This also affects the production of both raw materials and products, making corporate water risk management more important.
Water risk within the Mitsubishi Electric Group is evaluated as part of our corporate risk management framework. In fiscal 2024, in addition to assessing water stress and quality using Aqueduct*1 and Water Risk Filter*2 at approximately 170 production sites, including those of associated companies, we conducted assessments of species extinction risk using IBAT*3 (STAR). We then ranked the risk at each production site based on the results of these risk assessments and the business characteristics of each site (such as principal products and water usage accompanying production activities). We will consider setting water-related targets for high-risk sites, taking into account the circumstances of their watershed. We will also take measures to minimize any impact on the surrounding environment, such as ensuring compliance with wastewater standards in each region. In addition, during product development, we will strive to minimize the environmental impact of products, for instance, by evaluating product impact on water sources and assessing product lifecycles.
- 1 Water risk assessment tool developed by the World Resources Institute (WRI). Conducted assessment of “baseline water stress” and “coastal eutrophication potential.”
- 2 Water risk analysis tool developed and operated by the World Wide Fund for Nature (WWF). Conducted assessment of “baseline water depletion,” “blue water scarcity,” and “surface water quality index.”
- 3 Integrated Biodiversity Assessment Tool. Conducted assessment of Species Threat Abatement and Restoration Metric (STAR).
Response to High-Risk Sites
In fiscal 2020, the Mitsubishi Electric Group used Aqueduct to assess water risk, including water stress, and examined business characteristics at business sites in Japan and overseas. Sites with particularly high water risks are being managed as high-risk sites (total of five sites*4). To reduce water usage in high-risk sites, Environmental Plan 2025 sets forth a target of “reducing water usage per unit of sales by 6% or more by fiscal 2026 compared to fiscal 2020.” The five high-risk sites together account for roughly 7% of total water intake by the Mitsubishi Electric Group as a whole and roughly 9% of total sales.
After confirming the status of water conservation and reuse at water-using facilities in high-risk sites, we replaced water faucets with water-saving faucets and promoted the use of recycled water. As a result, water usage per unit of sales was 34% lower in fiscal 2024 than in fiscal 2020. We will continue to co-exist in harmony with local communities by implementing effective water risk measures in consideration of regional characteristics and circumstances at each production site, with a focus on high-risk sites.
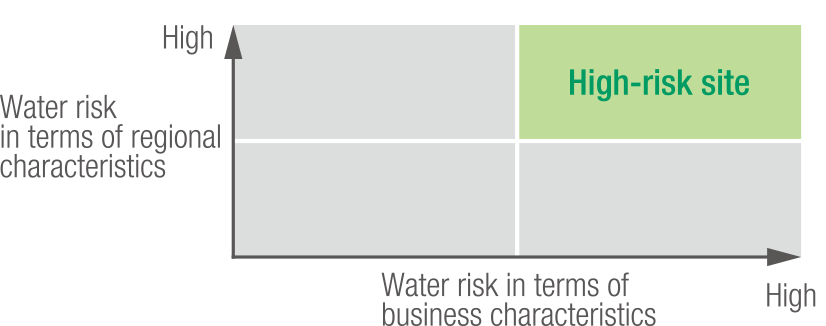
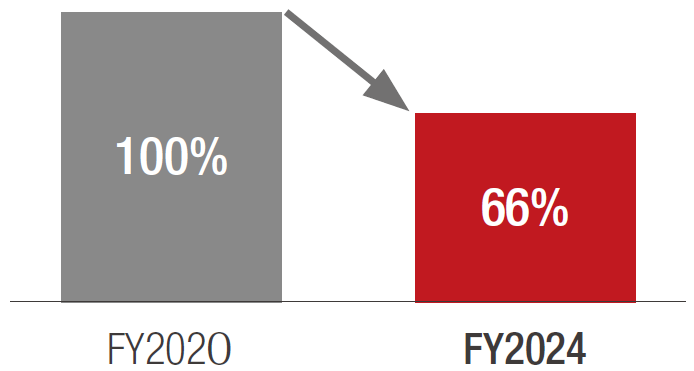
Status of Water Usage, Intake, Drainage, and Reuse
Status of Water Usage
The water usage of the Mitsubishi Electric Group in fiscal 2024 was 13,151,000 m³, of which 3,375,000 m³ was reused. The amount per unit of sales was 2.5 m³/million yen.
In Japan, we promoted recycle and reuse of water in production processes and use of purified wastewater for purposes such as toilet flushing and supply water for cooling towers. We also worked on reducing groundwater consumption through rainwater harvesting. Overseas, we also expanded the scale of water reuse and graywater utilization at our production sites.
Status of Water Intake
At production sites of the Mitsubishi Electric Group, water is taken to be used mainly for cooling, cleaning and adjusting the concentration of water-based paints, and as a solvent, an additive to materials and a heat medium. In fiscal 2024, the termination of operations at an LCD production site with high water usage brought the Group’s water intake down to 9,776,000 m³, a decrease of approximately 1,000,000 m³ compared to the previous fiscal year.
Status of Water Drainage
To avoid exceeding legal standard values set for each drainage point, the Mitsubishi Electric Group’s production sites have established voluntary standards, and they carefully manage water quality. When there is a certain drainage standard in place according to properties specific to the water area, such a standard is also incorporated into our standards.
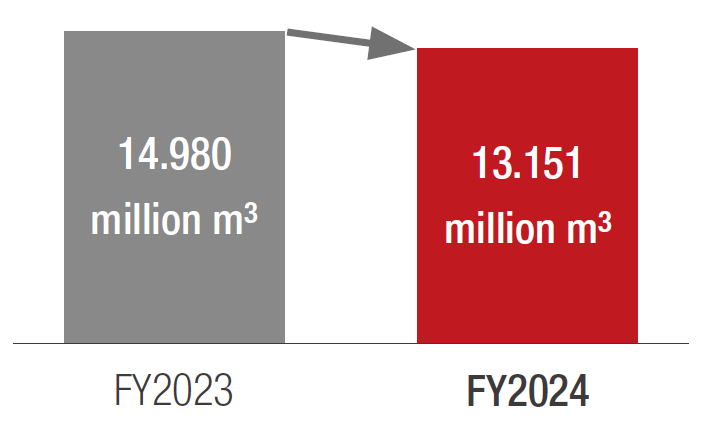
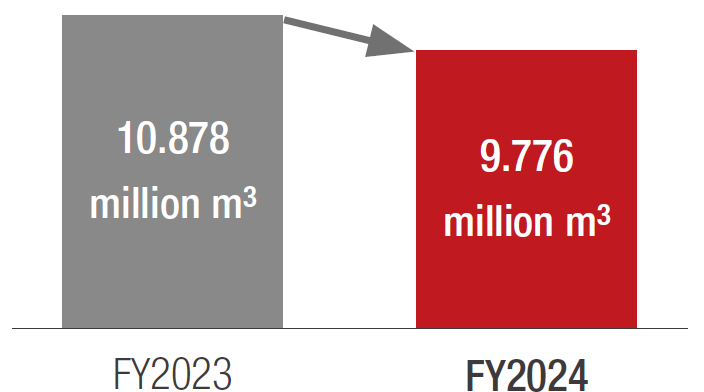
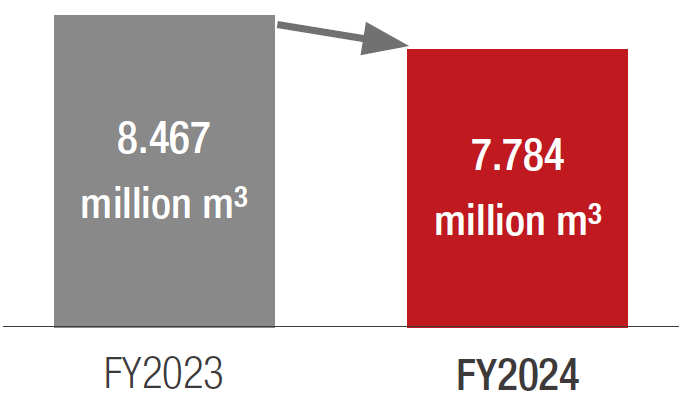
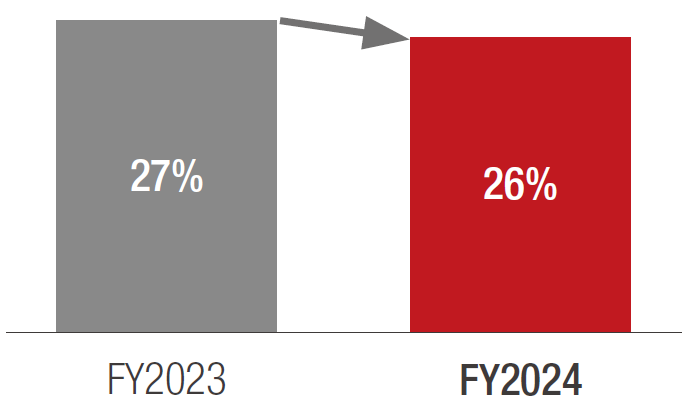
- 4 Following manufacturing companies located in Thailand:
- Mitsubishi Electric Consumer Products (Thailand) Co., Ltd.
- Siam Compressor Industry Co., Ltd.
- Mitsubishi Electric Automation (Thailand) Co., Ltd.
- Mitsubishi Elevator Asia Co., Ltd.
- Mitsubishi Electric Thai Auto-Parts Co., Ltd.
Managing Chemical Substances (Production)
The Mitsubishi Electric Group manages chemical substances by classifying those released from business sites and those contained in products into three levels, as stipulated in its Green Procurement Inspection Target Chemical Substance.
Managing Chemical Substances Released from Business Sites
Mitsubishi Electric utilizes an internal system to manage the release and transfer of chemical substances regulated by the PRTR Law*1 (PRTR*2 system) and volatile organic compounds (VOCs) that are released from its production sites in Japan. In fiscal 2024, we updated the system in accordance with the revision of the PRTR Law. In fiscal 2024, the Mitsubishi Electric Group (Japan) used 3,382 tons of chemical substances.
Managing the Chemical Substances Contained in Products
In order to comply with EU RoHS Directive,*3 EU REACH Regulation,*4 and other regulations, we register information on chemical substances contained in purchased materials and parts in our internal system in order to manage them.
- 1 Act on the Assessment of Releases of Specified Chemical Substances in the Environment and the Promotion of Management Improvement
- 2 Pollutant Release and Transfer Register. A system under which companies track the quantity of substances potentially harmful to human health or the ecosystem which are released into the environment or transferred outside a business establishment through waste materials, and report this data to government authorities. The authorities then use these reports and other statistics to produce estimates on release and transfer, and announce them publicly.
- 3 Directive on the restriction of the use of certain hazardous substances in electrical and electronic equipment
- 4 Regulation on registration, evaluation, authorisation and restriction of chemicals
Environmental Considerations in Logistics (Transportation)
The Mitsubishi Electric Group strives to improve transport efficiency and economy by visualizing logistics operations through quantitative evaluation and eliminating irrational irregular and, wasted efforts in operations, with the goal of realizing Economy & Ecology Logistics (Eco-Logistics) with little environmental impact.
Reducing the Use of Disposable Packaging Materials
The Mitsubishi Electric Group practices the 3Rs in packaging: reduce (simplify packaging), reuse (more returnable containers and packaging), and recycle (recycling of used packaging material).
In Japan, the Group’s total amount of packaging materials used in fiscal 2024 was 51 kt, and the amount per unit of sales was 13.4 kg/million yen. The Group continues to expand adoption of simpler packaging and the use of returnable containers and packaging.
The amount of packaging materials used by our 20 overseas associated companies was 53 kt, and the amount per unit of sales was 48.5 kg/million yen.
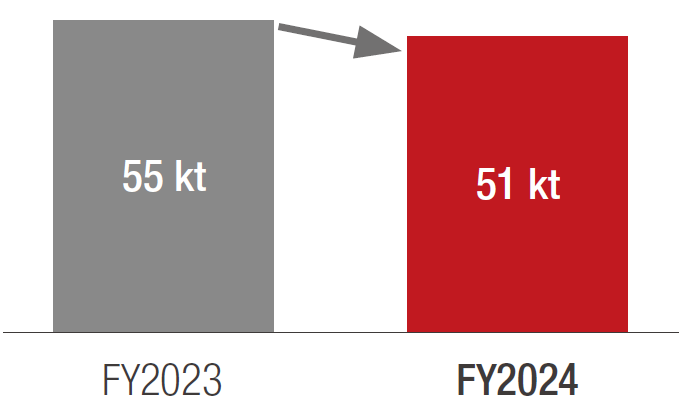
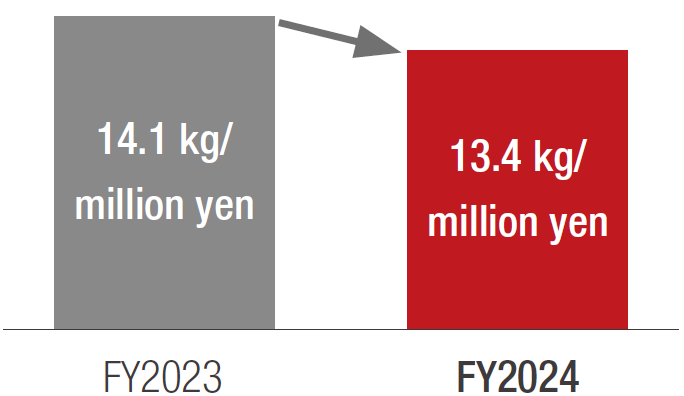
Reducing CO2 Emissions from Logistics
At Mitsubishi Electric Group companies in Japan, the following measures continue to be implemented in efforts to reduce CO2 emissions.
- Reviewing transportation routes
- Switching from truck transportation to rail transportation (modal shift)
- Reducing the number of trucks by improving load ratios (including Container Round Use)
In addition, overseas associated companies also reduced CO2 emissions by pursuing the optimal logistics based on the circumstances of each country.
As a result, the CO2 emissions of the Mitsubishi Electric Group totaled 491 kt-CO2, and the amount per unit of sales was 99.2 kg-CO2/million yen.
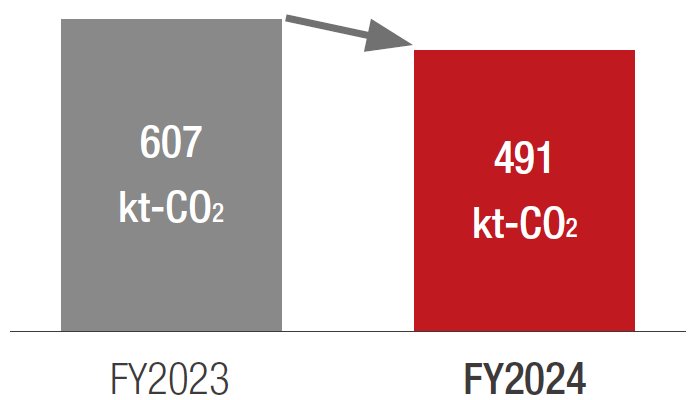
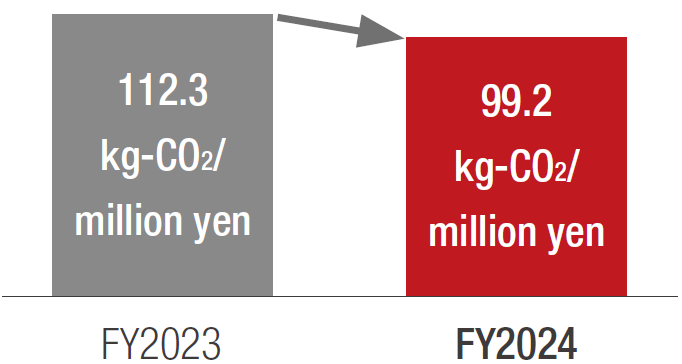
Contribution to Reducing CO2 Emissions from Product Usage (Use and recycling)
As more CO2 is emitted during product usage than during production, the Mitsubishi Electric Group has identified “reducing CO2 emissions from product usage” and “contributing to reducing CO2 emissions by product usage” as priority issues and is working to improve its products.
Evaluation of Reducing CO2 Emissions from Product Usage
Power consumed during product use is viewed as corresponding to the amount of CO2 emissions resulting from generating that power. Increasing product energy efficiency can lead to a reduction of CO2 emissions from product use.
The Mitsubishi Electric Group promotes initiatives to increase product energy efficiency by evaluating improvements in product energy efficiency using the new indicator shown below, beginning with models that are newly developed in fiscal 2022.

Evaluation of Our Contribution to Reducing CO2 Emissions by Product Usage
Among products of the Mitsubishi Electric Group, there are some that can help customers reduce CO2 during use. For example, using the Group’s heat pump system has greater potential to reduce CO2 emissions compared to using combustion-type heating and hot water systems. The Group’s inverters and power devices, as well, can reduce CO2 emissions during use, since they contribute to enhancing the energy efficiency of the final products they are embedded in.
Contribution to reducing CO2 emissions is calculated by comparing the use of a relevant product with the use of an alternative product that would likely be used if the relevant product did not exist. It is based on the following formula, with the alternative product as the reference product.

Beginning with models newly developed in fiscal 2022, the improvement in contribution to reducing CO2 emissions when a customer chooses to use a Mitsubishi Electric product is calculated using the new indicator shown below.

In fiscal 2024, we achieved an average improvement rate of 2.5% compared to the previous model thanks to improvements in a variety of products, including air conditioning fans and automotive equipment control products. We will continue our efforts to pursue greater energy efficiency and the contribution to reducing CO2 emissions as we develop new product models.
Improvement rate of newly developed models compared to previous models *
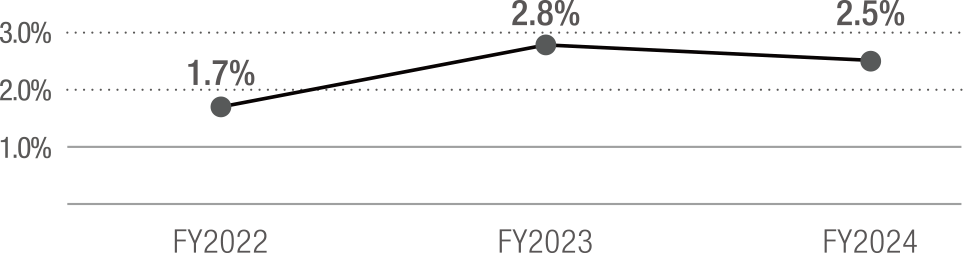
* Average improvement rate of annual power consumption and contribution to CO2 reduction compared to previous models
Breakdown of products relevant to “reducing CO2 emissions from product usage” and “contribution to reducing CO2 emissions by product usage”
Evaluation item | Product examples | Indicator used to evaluate improvement rate over previous models |
---|---|---|
Reducing CO2 emissions from product usage |
Monitoring, control, and protection devices for power generation plants and systems, railcar air-conditioning systems, electrical equipment for railcars, movable platform gates, vacuum circuit breakers, elevators, escalators, intelligent transport systems (ITS; ETC, smart interchanges), air conditioners, refrigerators, ventilation fans, electric fans, processing machines, LED light bulbs, residential lighting fixtures, etc. | Reduction in annual energy consumed during product usage |
Turbine generators | Improvement of power conversion efficiency | |
Optical communication network systems, wireless communication systems | Reduction in annual energy consumed per product performance | |
Automotive equipment control products | Reduction from the incorporation of products with power energy use, proportionally divided by weight | |
Contribution to reducing CO2 emissions by product usage |
Water heating systems (heat pump electric water heaters, electric water heaters) | Improvement of the contribution to reducing CO2 emissions by using heat pumps, in reference to combustion-type heating and hot water systems |
Inverters, power devices (power modules, high power devices) | Improvement in the contribution to reducing CO2 emissions gained by the incorporation of products with lower power loss | |
Total heat exchanging ventilation equipment, electrical equipment for railcars (control devices) | Improvement in the contribution to reducing CO2 emissions expected from the introduction of said products |
Recovery/Recycling of Used Home Appliances at a Specialized Recycling Plant (Use and recycling)
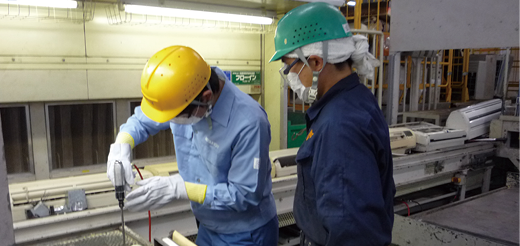
Closed-Loop Recycling of Plastic
Green Cycle Systems Corporation, a member of the Mitsubishi Electric Group, utilizes Mitsubishi Electric’s original technology for sorting of crushed mixed plastics into polypropylene (PP), polystyrene (PS), and acrylonitrile butadiene styrene (ABS) to recycle them into high-purity plastics that are equivalent to virgin materials. The Mitsubishi Electric Group is promoting closed-loop recycling using these recycled plastics again in Mitsubishi Electric home appliances.
Flow chart of Mitsubishi Electric Group closed-loop plastic recycling
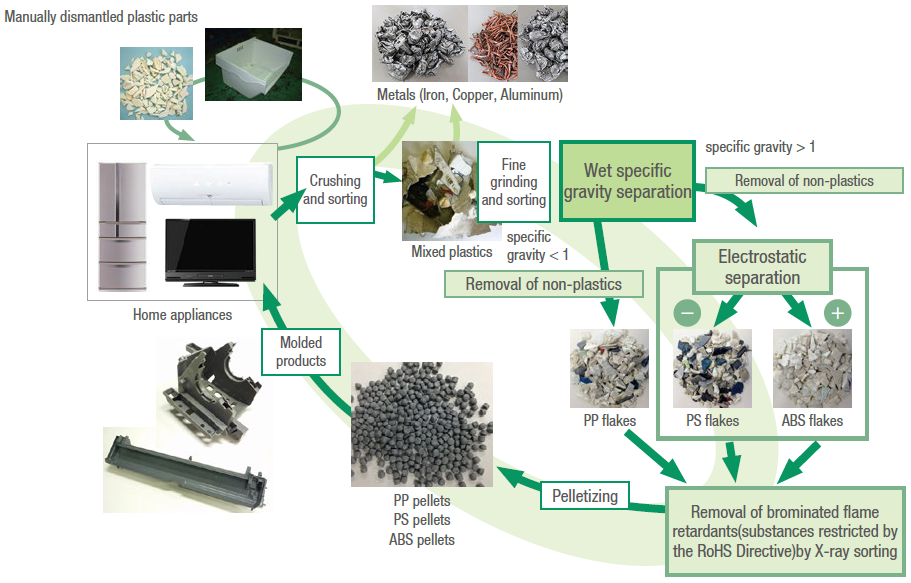
By utilizing our advanced plastics sorting technology cultivated over many years in the field of home appliance recycling, Mitsubishi Electric is promoting efforts to solve the problem of waste plastics in collaboration with companies in a variety of industries.
Topics
Creating a Service in the Recycling Business
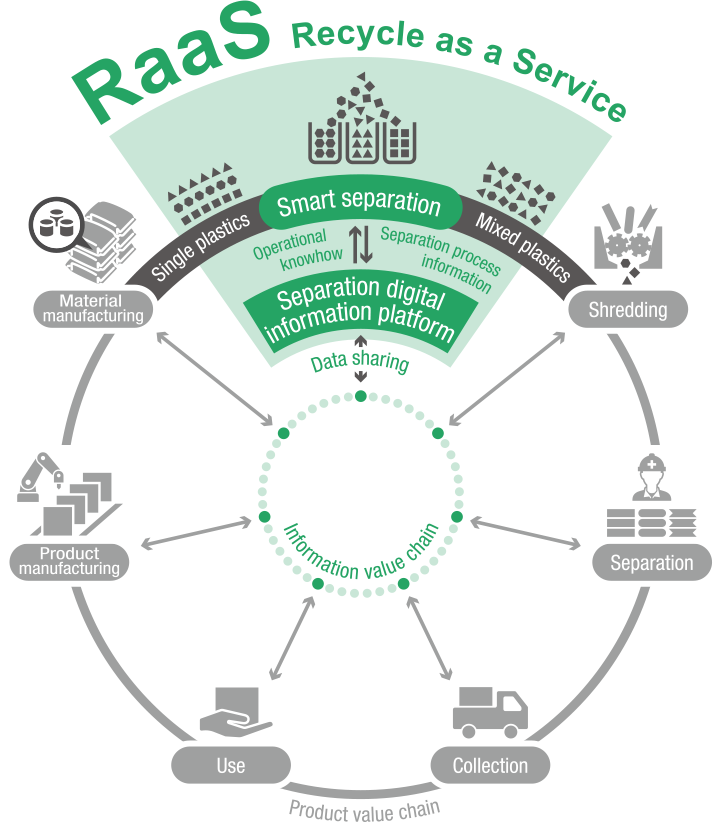
Position of RaaS in the value chain
Leveraging technology cultivated in the home appliance recycling business, the Mitsubishi Electric Group plans to offer its Smart Plastic Separation DX Solution RaaS*1 to enable utilization of its advanced plastics separation technology using static electricity (electrostatic separation) in the plastics recycling of customers.
The RaaS solution uses sensors to collect data on factors that affect electrostatic separation(raw material composition of the shredded plastic chips and input volume, etc.) and the results of separation, which is then analyzed using AI to automatically control the position of partitions and the voltage in the receptacles that collect the separated plastic. Such use of digital and smart technologies in electrostatic separation makes it possible to separate a variety of mixed plastics in a stable manner, thereby contributing to the production of highquality recycled plastic materials. The Mitsubishi Electric Group will expand the circle of resource circulation with the aim of realizing a circular economy by offering the RaaS solution to customers in a variety of industries beyond the home appliance industry.
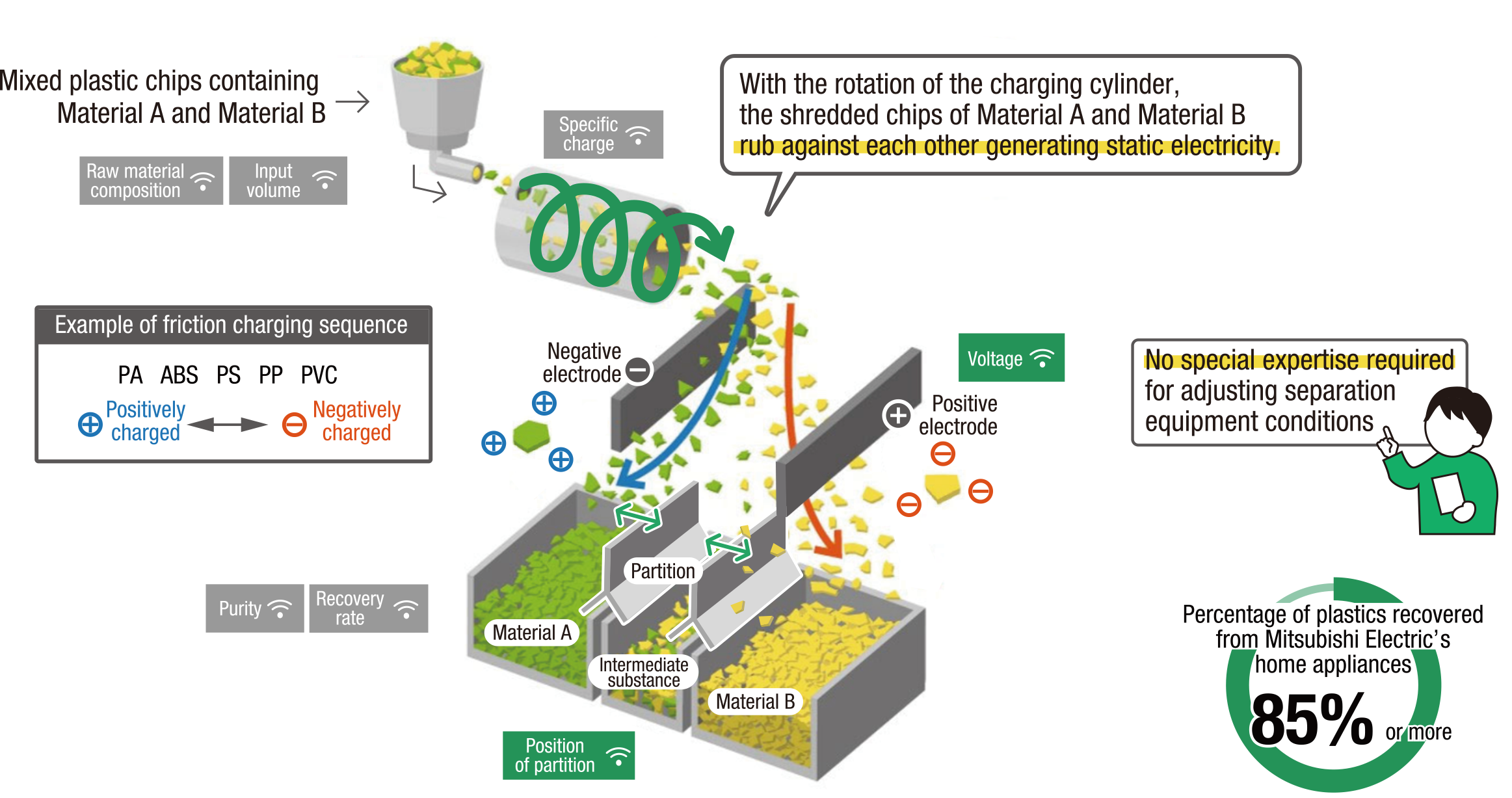
- 1 Recycle as a service